Mastering Vibratory Rock Polishers: Techniques & Tips
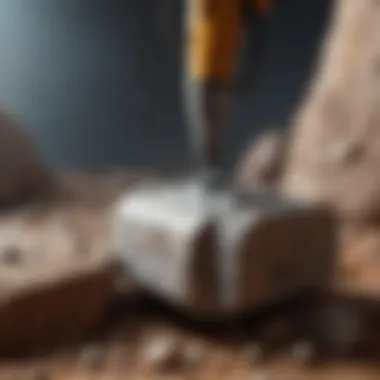
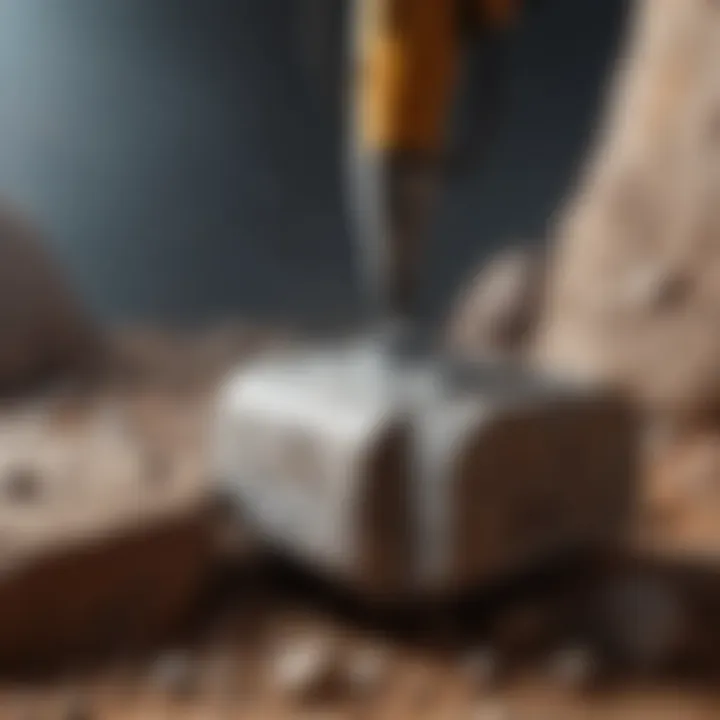
Intro
A vibratory rock polisher is a fascinating tool for enthusiasts aiming to enhance their collection of polished stones. This device operates by creating a vibrational motion, which facilitates the effective polishing of rocks through abrasive action. Understanding how it functions, the applications it serves, and the techniques involved can greatly improve outcomes for users. This article aims to delve into these aspects, especially focusing on the practical tips and insights that both novices and seasoned collectors can benefit from.
Featured Collectible of the Month
Overview
Each month, various rocks and minerals capture the attention of collectors. This month's featured collectible highlights the amethyst, known for its stunning purple hues and extensive applications in jewelry making and healing. Not only is amethyst aesthetically pleasing, but its geological properties make it a significant specimen for any collector.
Historical Significance
Amethyst has a rich history. Used by ancient civilizations, it was believed to protect its wearer from intoxication and promote mental clarity. Its prominence in royal adornments also traces back to those times, elevating its status even further. Understanding the historical context enriches the collector's experience and deepens appreciation for this unique mineral.
Identification Techniques
Identifying various rocks, especially when collecting, requires keen observation and understanding of their characteristics. Adopting systematic techniques can significantly aid in this process.
Visual Characteristics
Visual inspection serves as the first step in identifying a rock. Specific traits include:
- Color: The most apparent trait.
- Luster: Shiny or dull finishes provide clues.
- Texture: Smooth, rough, or granular surfaces can indicate compositions.
- Shape: Irregular versus rounded outlines can suggest forming processes.
Mastering these visual characteristics allows for quick differentiation between various types of rocks.
Resources for Identification
Several resources exist for rock identification. Utilizing these sources makes identifying new specimens easier:
- The Mineralogical Society of America (www.minsocam.org)
- Rock Identification Guides by local geological institutions
- Online communities, such as Reddit's rockhounding subreddits, where enthusiasts share experiences
Preface to Vibratory Rock Polishers
The vibratory rock polisher is an essential tool for many rock and fossil collectors. Its ability to produce smooth and shiny finishes on stones makes it a valuable device in the lapidarycraft. Understanding its functionalities not only helps hobbyists but also professionals to enhance their techniques. By familiarizing oneself with the vibratory rock polisher, collectors can achieve results that reflect both skill and quality.
Definition and Purpose
A vibratory rock polisher is a mechanized device designed for the purpose of polishing raw gemstones and other minerals. Unlike traditional tumblers that utilize a rotating mechanism, vibratory polishers rely on vibration to create a more efficient and faster polishing process. The central purpose of this machine is to transform rough stones into beautifully polished gems. This transformation not only elevates the aesthetic appeal of the rock but also highlights its unique characteristics. Such a process satisfies both aesthetic desires and the scientific curiosity surrounding geology.
The polisher operates by combining the rocks with abrasive media and water in a bowl. As vibrations occur, the materials inside the bowl collide, removing rough surfaces and imperfections. This specific method can cater to various rock types and desired finishes.
Historical Context
The concept of polishing stones has ancient roots, dating back thousands of years. Early artisans would use manual methods, sometimes working with rudimentary tools to achieve desired finishes. As technology advanced, the introduction of motors and efficient designs revolutionized the lapidary arts.
The vibratory rock polisher emerged as a significant innovation in the 20th century. It marked a shift toward automation in the polishing process. Collectors soon recognized the advantages of this method. Not only does it reduce the time required for polishing, but it also delivers consistent results with less manual intervention. The evolution of this device reflects the growing appreciation of gemology and the increasing demand for polished stones in various industries.
"The vibratory rock polisher represents a convergence of craftsmanship and technology, enabling collectors to explore their passion for earth sciences more effectively."
In today’s world, the vibratory rock polisher remains a cornerstone in many workshops. Its relevance spans various domains, from casual collectors to professional jewelers. Understanding its principles and techniques is key for anyone looking to maximize the potential of their polishing endeavors.
Principles of Operation
Understanding the principles of operation is critical for optimizing vibratory rock polishers. This section addresses the core mechanisms that enable effective polishing and highlights the benefits that come with comprehending these principles. When users grasp how their equipment works, they can adapt their techniques, troubleshoot issues, and achieve superior results.
Vibration Mechanics
The mechanics of vibration are fundamental in a vibratory rock polisher. The device operates on the principle of oscillation, where the motor creates a repetitive motion. This motion is transferred to the tumbler, generating a combination of circular and linear movements. The intensity and frequency of these vibrations can significantly influence polishing effectiveness.
The setting of vibration frequency must be matched to the type of media and rocks involved. Too much vibration can lead to over-polishing or even damage to delicate stones. Ideally, the user should start with a moderate vibration setting and observe the effects before making adjustments. If operations cause excessive wear, users can recalibrate the vibration to a kinder setting. The fine-tuning of these motions can yield not just smoother surfaces but truly distinct finishes of varying degrees.
Energy Transfer
Energy transfer plays a key role in how efficiently the polishing process occurs. In vibratory rock polishers, energy is imparted from the motor through a drive system to the tumbler. The materials used in the bowl and liner significantly affect this energy transfer, influencing the overall performance of the polisher.
Proper selection of materials for the bowl and liner can enhance energy transfer efficiency. For instance, polyethylene is commonly used as a liner due to its durability and low friction properties. A well-designed energy transfer system reduces wear on the motor and extends the lifespan of the machine.
Understanding the concept of energy transfer allows users to make informed decisions about their equipment and media. It emphasizes the need for regular maintenance to ensure mechanisms remain clean and free from obstructions. Maintaining the components aids in preventing energy losses that could compromise polishing results.
"Understanding how your vibratory rock polisher works is as essential as knowing the best techniques for polishing. The synergy between mechanics and energy efficiency determines success in achieving a desired polish."
In summary, familiarity with vibration mechanics and energy transfer is indispensable for anyone looking to enhance their rock polishing experience. By leveraging this knowledge, hobbyists and collectors can maximize the functionality of their polishers and achieve exceptional results.
Key Components of a Vibratory Rock Polisher
Understanding the key components of a vibratory rock polisher is essential for both novices and seasoned users. Each element plays a crucial role in the overall functionality and effectiveness of the machine. The right combination of these components not only improves polishing outcomes but also impacts the longevity and maintenance of the equipment.
Tumbler Design
The tumbler design is a primary factor that influences how the rocks are polished. It affects the movement and position of the media and rocks within the machine. A well-designed tumbler ensures uniform action, which is critical for consistent polishing results.
The shape and size of the tumbler can vary, impacting the speed and efficiency of the polishing process. For instance, a larger tumbler allows for more rocks and media, leading to more efficient batch processing. Additionally, the shape can affect how rocks tumble and interact with the polishing media. Users should consider their specific needs and the types of materials they commonly polish when selecting a tumbler design.
Motor and Drive System
The motor and drive system serve as the beating heart of the vibratory rock polisher. This component provides the necessary vibration and movement that initiates the polishing process. A powerful and reliable motor is crucial for smoothly running the polisher at various speeds.
Users need to evaluate both motor horsepower and torque based on expected usage. A motor that is too weak may lead to inconsistent results or even mechanical failure. On the other hand, an overly powerful motor can cause excessive vibrations, leading to premature wear and tear. Thus, finding the right balance is important to ensure optimal functioning.
Bowl and Liner Materials
The materials used for the bowl and liners of a vibratory rock polisher can significantly affect its performance and durability. Often made of rubber or plastic, the choice largely depends on the intended use.
Rubber bowls are generally quieter and can provide better cushioning for the rocks, whereas plastic might be lighter and easier to clean. Additionally, different liner materials can impact how effectively the polishing media and rocks interact, potentially influencing the final finish of the polished materials.
Key Points to Remember:
- Bowl Material: Stabilizes the tumbling action and reduces noise.
- Liner Material: Influences the lifespan of the polisher and the quality of the finish.
- Compatibility: Ensure that the chosen materials match the abrasive media used.
"The effectiveness and longevity of your vibratory rock polisher largely depend on the quality of its components."
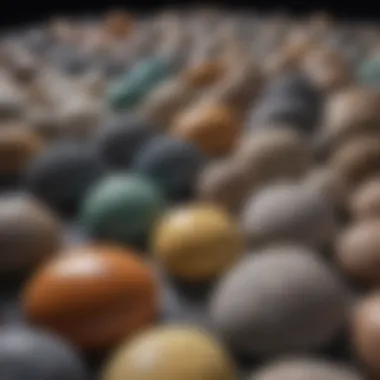
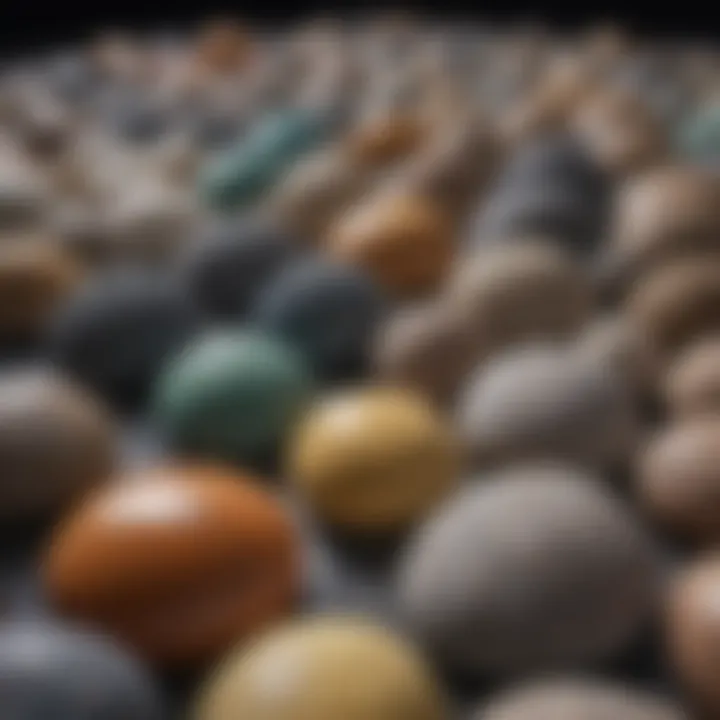
In summary, selecting the right key components for a vibratory rock polisher is vital to maximizing the effectiveness of the polishing process. By considering design, power, and material quality, users can enhance their polishing experiences and achieve impressive results.
Choosing the Right Media
Choosing the right media in vibratory rock polishing is crucial for achieving desirable results. The media you select can significantly affect the efficiency of the polishing process, as well as the final appearance of the rocks. Different types of abrasive media can produce varying degrees of smoothness, shine, and texture, directly impacting the quality of your polished rocks.
When you opt for a specific type of media, consider the hardness and abrasiveness, as well as the size and shape. Each medium interacts differently with the surface of the rocks being polished. Not only does the choice of media determine how quickly the rocks get polished, it also influences the wear on the machinery and the overall longevity of the polishing process. Thus, making an informed decision on media selection is not insignificant but essential for optimal operation.
Types of Abrasive Media
There are several types of abrasive media used in vibratory rock polishing. Each has its unique properties and benefits:
- Ceramic Media: Often favored for its durability, ceramic media can provide a smooth finish and high polish. It usually comes in various shapes and sizes, allowing for customization based on the type of rock being polished.
- Plastic Media: This type is generally gentler and is beneficial for softer stones or where less aggressiveness is desired. They can help achieve a uniform finish without scratching the surfaces as much as harder media.
- Natural Abrasives: Materials like walnut shells or corn cob can be used for final polishing stages. They are less aggressive, useful for achieving a high-gloss shine without damaging the rocks.
- Graded Silica: This is a common choice for initial grinding and smoothing. Its varied grit sizes allow for tailored polishing processes based on the type and condition of the stones.
Factors Affecting Media Selection
Several factors influence the selection of the appropriate media for your vibratory rock polisher:
- Rock Type: Different types of rocks require different media. For example, harder rocks may necessitate more aggressive media, while softer stones might benefit from gentler options.
- Desired Finish: The finish you aim for also dictates your choice. If a high polish is needed, softer media may be the last step in your polishing process while harder media is essential for the initial grinding.
- Machine Type: The capabilities of your particular vibratory rock polisher can limit or enhance your media options. Ensure that your selected media is compatible with your machine’s specifications.
- Cost and Availability: Budget constraints might also play a role in your media choice. Therefore, consider both the financial implications and the availability of different media types.
Choosing the right media is not just about beauty; it is the backbone of successful polishing.
Operating a Vibratory Rock Polisher
The operation of a vibratory rock polisher is a critical aspect for anyone interested in the craft of rock polishing. Understanding how to effectively operate this tool can lead to superior polishing results and efficient use of time and resources. The vibratory rock polisher, when used correctly, produces smoother and shinier rocks that enhance their aesthetic appeal.
Preparation of Rocks
The first step in operating a vibratory rock polisher is the preparation of rocks. Properly preparing the rocks is vital for achieving the desired finish. Before placing rocks in the tumbler, ensure that they are clean. Remove any dirt, mud, or debris that may interfere with the polishing process. Use a brush or cloth for thorough cleaning.
Here are some specific steps to follow during preparation:
- Sorting: Group rocks by size and type. This helps in achieving uniform polishing results as different types of rocks may require different polishing times.
- Initial Assessment: Inspect each rock for visible flaws. This can help to identify rocks that may not polish well due to cracks or inclusions.
- Water: Use water as a lubricant during the initial phase. Ensure the tumbler is filled to the correct level, avoiding overfilling, which can cause slippage and inconsistent results.
- Abrasive Media: Choose the right abrasive media based on the type of rock. Harder rocks like agate need more aggressive media than softer varieties.
Preparing the rocks accurately sets the foundation for a successful polishing process.
Polishing Process
Once the rocks are prepared, the polishing process can begin. This is where the vibratory action of the rock polisher comes into play. The movement created by the machine helps to smooth out the rough edges and surfaces of the rocks, contributing to a shiny finish.
The polishing process involves several phases:
- Grading Phases: Start with coarser grits to remove any imperfections and progress to finer grits. Each grit should be used for a specific duration, depending on the hardness of the rock.
- Polishing Compound: In the final stages, apply a polishing compound designed for vibratory polishers. This compound is crucial for achieving a brilliant finish. Monitor closely for signs of wear or degradation in the media during this phase.
"Achieving the desired results often requires patience and repeated cycles of polishing."
- Duration: The time taken for polishing can vary. Regular checks should be done to ensure rocks are not over-polished or left to process for too long, which can dull the edges.
Success in the polishing process comes from careful monitoring and adjustment. Remember to always follow the manufacturer's guidelines in operations to enhance the overall effectiveness of the vibratory rock polisher.
Advanced Techniques for Polishing
Advanced techniques in rock polishing are vital for both hobbyists and professionals who seek to elevate their outcomes. Mastering these techniques can allow users to tailor their polishing processes, thus enhancing the quality and aesthetics of the final product. Through a careful examination of customizable polishing cycles and methods to achieve specific finishes, enthusiasts and collectors can significantly improve their results.
Customizing Polishing Cycles
Customizing polishing cycles is essential for adapting the process to various rock types and desired finishes. This involves adjusting parameters such as time, frequency, and media choice to optimize outcomes for specific materials. Different rocks react uniquely during polishing, and understanding the inherent characteristics of each can lead to more refined results.
When setting up a polishing cycle, consider the following:
- Duration: Increase or decrease cycle time based on the hardness of the rock. Softer rocks may require shorter cycles, while harder rocks can withstand longer periods.
- Frequency: Some machines allow users to adjust the vibration frequency. Experimenting with this setting can enhance polishing efficiency.
- Media Combination: Combining different types of abrasive media throughout the cycle can yield a smoother finish. Start with coarser media and progress to finer grades.
By customizing these aspects, users can influence the polishing outcome significantly.
Achieving Specific Finishes
Achieving specific finishes requires a thorough understanding of both techniques and materials. This is where attention to detail is pivotal. Different finishes may be desired, from a high-gloss sheen to a more matte appearance. Each finish presents its own set of requirements and methodologies.
To achieve a high-gloss finish:
- Final Media Selection: Use fine polishing compounds such as cerium oxide or aluminum oxide. This choice can drastically influence the gloss level.
- Buffing Time: Allocate adequate buffing time during the final polishing stage. Extended polishing often enhances shine.
- Surface Conditioning: Post-polishing, conditioning the surface with a soft cloth can eliminate micro-abrasions, adding to the polish quality.
For a matte finish, consider:
- Coarse Media Usage: Utilize finer grit media and avoid high-gloss polishing agents.
- Controlled Polishing Time: Limit the duration of polishing to prevent any potential glossiness.
"Adjusting your approach based on the desired outcome is crucial in rock polishing. Being meticulous ensures that each project results in a tangible representation of your skills."
Understanding the nuances of customization and finish achievement not only enriches the user's capabilities but also deepens the satisfaction derived from the craft. Integrating these advanced techniques into regular practices can significantly enhance the overall rock polishing experience.
Maintenance and Care
Maintaining a vibratory rock polisher is essential for optimal performance and longevity. Regular upkeep not only ensures effective polishing results but also prolongs the equipment's lifespan. Neglecting maintenance can lead to mechanical issues, inconsistent results, and even costly repairs. Understanding the necessary care techniques will empower users to achieve the desired finish on their rocks while reducing the need for professional servicing.
Regular Cleaning Practices
Cleaning the vibratory rock polisher is a straightforward yet important task. After each use, it is crucial to remove all residual polishing media and any remnants of rocks. This prevents contamination that may affect future polishing sessions. A few key cleaning practices should be incorporated:
- Disassembly: Carefully disassemble the polisher according to the manufacturer’s instructions. This ensures all areas can be thoroughly accessed and cleaned.
- Media Removal: Empty the polishing media, and separate it if necessary. Different types of media may not mix well, leading to inefficiencies.
- Wipe Down Surfaces: Use a soft cloth or brush to clean the bowl and tumbler surfaces. Ensure there are no sticky residues or deposits left behind.
- Inspection: While cleaning, check for any wear and tear. Look for cracks or damages in the bowl, liners, or any other components.
These practices will help in maintaining both the functionality and cleanliness of the polisher, leading to enhanced polishing results.
Identifying Mechanical Issues
Mechanical issues can arise due to multiple factors, such as improper usage or lack of regular maintenance. Being proactive in identifying these problems can save time and resources in the long run. Common signs of mechanical issues may include:
- Unusual Noises: Listen for grinding, rattling, or any noise that is out of the ordinary during operation. Such noises could indicate loose components or problems with the motor.
- Vibrational Irregularities: If the polisher does not vibrate consistently, this could suggest imbalances in the load or changes in the mechanical integrity.
- Inconsistent Polishing: Noticing uneven finishes on rocks may indicate that the motor is malfunctioning or that there is an issue with the polishing media.
It is vital to regularly perform checks and routine maintenance. Having a solid understanding of these potential mechanical issues will ensure that users can address them promptly, maintaining both efficiency and quality in rock polishing.
"Regular care is not just about keeping the machine clean but includes comprehending its operational health."
By incorporating these practices and being attentive to any signs of wear or malfunction, users can ensure their vibratory rock polisher operates smoothly and delivers optimal polishing results for years to come.
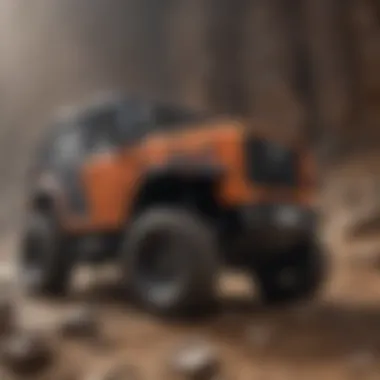
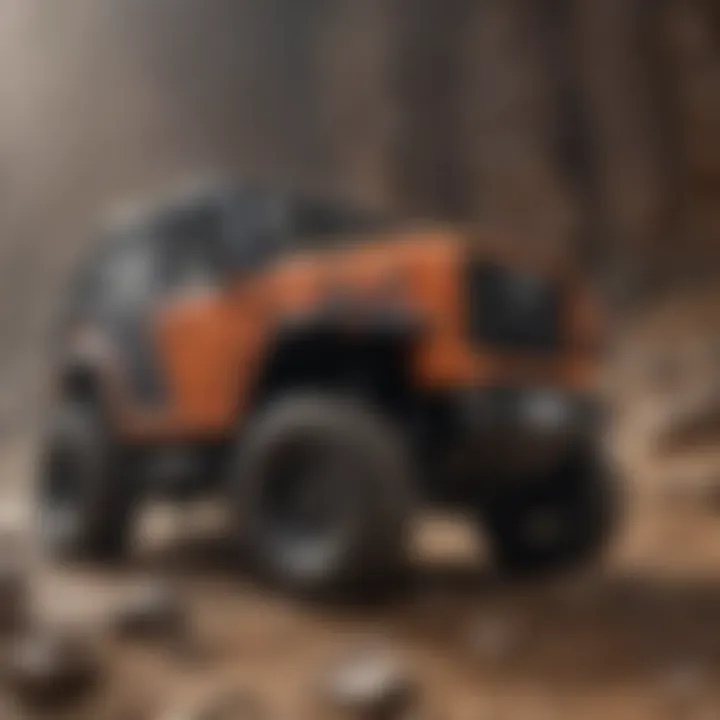
Troubleshooting Common Issues
Troubleshooting common issues with vibratory rock polishers is a critical aspect of ensuring optimal performance and achieving desired polishing results. Understanding these challenges not only enhances the user experience but also extends the lifespan of the equipment. Addressing issues as they arise helps maintain the quality of the polishing process, ultimately leading to better results for both amateur hobbyists and professional collectors.
Inconsistent Results
Inconsistent results can be a source of frustration for rock polishers. Factors contributing to this issue often include improper media selection, incorrect processing times, or variations in the materials being polished.
To start, it is vital to ensure the right type of abrasive media is being used for the specific rocks. Each rock type may respond differently to the polishing process. A quartz crystal, for example, might require different abrasives compared to a more delicate gemstone.
Next, processing times should be carefully monitored. Over or under-polishing can lead to uneven surfaces, causing inconsistent finishes. Users can experiment with different cycle times to find the optimal duration that suits the type of rock and media combination being used.
Finally, variations in the rocks themselves may cause inconsistencies. Imperfections or differences in density between stones can affect the overall output. To manage these variations, it is advisable to batch similar rocks together during polishing.
Noise and Vibration Problems
Noise and vibration problems are common complaints among users of vibratory rock polishers. Excessive noise can indicate underlying mechanical issues, while abnormal vibrations can signal that components are not functioning as intended.
Firstly, regular maintenance and checks should be conducted on the motor and drive systems. Ensure all connections are tight and check for any signs of wear or looseness within the tumbler design. Misalignments or foreign objects can create excessive noise and vibrations.
Secondly, the bowl and liner materials may play a role in noise levels. Some materials absorb sound better than others. If noise is a concern, considering upgrades to high-damping materials may help mitigate this issue.
"Proper troubleshooting is the first step to mastering the art of rock polishing."
Addressing these concerns can ultimately lead to more satisfying results and help users unlock the full potential of their vibratory rock polishers.
Best Practices for Enhancing Polishing Results
Enhancing polishing results is vital for achieving high-quality finishes in vibratory rock polishing. Practitioners, whether hobbyists or professionals, must understand and implement best practices to optimize the polishing process. Solid fundamentals combined with advanced techniques can significantly improve outcomes. Proper techniques can help achieve uniform polishing, reduce processing time, and prevent damage to the rocks.
Layering Techniques
Layering techniques involve using multiple types of abrasive media in a carefully calculated sequence during the polishing process. This method enhances results by gradually refining the surface of the rocks. For instance, starting with a coarse medium allows for the removal of rough edges and imperfections. After this initial phase, a medium-grade abrasive should follow, smoothing the surface further. Finally, a fine abrasive will bring a high-gloss finish.
To effectively implement layering techniques, consider these points:
- Sequential Abrasive Use: Always start with the coarsest media and progress to finer grades. This ensures that larger imperfections are addressed first.
- Timing: Allow sufficient time with each layer. Rushing between stages can result in less optimal finishes.
- Media Compatibility: Ensure that the abrasives used at each stage are compatible in terms of hardness and wear characteristics. Mismatched media can lead to inefficient polishing.
- Frequency of Layer Changes: Monitor the effectiveness regularly. If a particular layer does not yield favorable results, adjust the media choice or modify the duration of use.
This approach is not universal and might require adjustments based on the specific types of rocks being polished. Experimenting can lead to personalization of the polishing process which achieves the best results for individual needs.
Temperature and Humidity Control
Maintaining appropriate temperature and humidity levels is critical in the polishing process. Environmental factors can influence not only the efficiency of the vibratory polisher but also the final results on the rocks. If the environment is too cold or too humid, the polishing medium may not function effectively, leading to inconsistent finishes.
Key considerations include:
- Ideal Temperature Range: Aim for a temperature range between 60°F to 75°F. At this range, the media works optimally, and the movements of the rocks are less likely to be hindered.
- Humidity Levels: A humidity level between 30% and 50% is generally ideal. High humidity can lead to media clumping, while low humidity can cause dryness and inconsistent finishes.
- Environmental Monitoring: Use thermometers and hygrometers to monitor conditions accurately. Adjust indoor climates using heating or dehumidifying equipment if necessary.
- Batch Homogeneity: Ensure that all rocks and media are at similar temperatures and humidity levels before starting the polishing cycle. This helps in achieving uniformity in results.
Controlling temperature and humidity effectively enhances the polishing experience. Optimal conditions yield smoother surfaces and a more appealing finish, reinforcing the overall quality of the rock polishing practice.
Properly adhering to best practices is not just about achieving a shine, but creating an entire sensory experience that reflects the nature of the materials used.
Safety Considerations
Safety considerations play a crucial role when utilizing vibratory rock polishers. The risk of injury can arise not just from the machinery itself but also from handling the materials used in the polishing process. Understanding these aspects is vital for both inexperienced and seasoned users. Not only does adhering to safety protocols protect the individual using the machine, but it also enhances the overall effectiveness of the polishing operation.
Personal Protective Equipment
When operating a vibratory rock polisher, wearing the right personal protective equipment (PPE) is essential. It serves as the first line of defense against accidents and exposure to harmful materials. Here are key components of PPE to consider:
- Safety Glasses: Protects eyes from dust and flying debris during the polishing process.
- Dust Masks or Respirators: Minimizes inhalation of harmful particles released during polishing.
- Gloves: Prevents skin contact with abrasive materials and chemicals often used in the polishing process.
- Ear Protection: Essential for prolonged exposure to noise produced by the polisher, which can cause hearing damage over time.
These items not only reduce the chance of injury but also promote a more comfortable working environment. Staying protected is not just a recommendation; it is an integral part of responsible operation practices.
Handling and Storage of Materials
Proper handling and storage of abrasive materials and chemicals used in the polishing process are equally important. Disregarding safe practices can lead to accidents and health issues over time. Some considerations include:
- Storage Location: Always store materials in a cool, dry place away from moisture, which can impact effectiveness and safety.
- Labeling: Clearly label all containers to avoid confusion and to ensure proper usage. Misuse of materials can lead to dangerous outcomes.
- Disposal Methods: Follow local regulations when disposing of used polishing media and chemicals. Improper disposal can harm the environment and may result in legal consequences.
"Safety is not just a priority, it is an essential component of any successful operation."
Incorporating these safety considerations into your practice is not just beneficial; it is imperative for anyone involved in rock polishing. Aside from protecting personal health, following these guidelines ensures a smoother process and better results.
Vibratory Rock Polishers in Different Applications
Vibratory rock polishers play a significant role in various settings, ranging from hobbyist environments to commercial operations. Understanding these different applications is essential for anyone interested in maximizing the utility of their rock polisher. This section examines how vibratory polishers are used across different contexts, the benefits they bring, and key considerations to keep in mind.
Hobbyist Uses
Hobbyists often utilize vibratory rock polishers to refine their collections of stones and fossils. For enthusiasts, the primary appeal lies in the ability to achieve a polished finish on a variety of materials, enhancing natural beauty. The use of vibratory polishers allows hobbyists to process multiple batches of rocks simultaneously. This efficiency boosts productivity without compromising quality.
Key Benefits for Hobbyists:
- Versatility: Suitable for a wide range of materials, including quartz, agate, and even softer stones.
- Time Efficiency: Vibratory polishers can cut down polishing time significantly compared to traditional rotary methods.
- Improved Aesthetics: Polished stones exhibit better color and shine, enhancing their visual appeal for display or crafting.
In this hobbyist context, proper selection of abrasive media is crucial for achieving the desired finish. For instance, using a finer grit in the final stages of polishing can lead to a more brilliant luster. Additionally, many hobbyists appreciate the ability to experiment with different media and polishing compounds to refine their techniques over time.
Commercial Applications
In commercial settings, vibratory rock polishers are employed for larger scale operations involving geological or decorative materials. Businesses involved in gemstone processing, jewelry making, or decorative stone supply heavily rely on these machines to maintain consistent quality.
Considerations for Commercial Use:
- Scalability: Vibratory polishers can be adjusted to handle varying volumes of materials, from small batches to large-scale processing.
- Cost-Effectiveness: Faster polishing processes translate into higher output, enabling businesses to meet demand more effectively.
- Quality Control: Consistent results are critical for commercial enterprises. Properly maintained vibratory polishers can deliver uniform finishes across large batches of stones.
"In industries where appearance directly impacts value, the use of vibratory polishers can significantly influence a company's reputation and profitability."
The importance of maintaining these machines cannot be understated within commercial applications. Regular checks on components and timely servicing can prevent costly downtimes and ensure peak performance. Overall, the integration of vibratory polishers into commercial workflows enhances productivity while ensuring product quality.
In summary, whether for hobbyist enjoyment or commercial gain, understanding the applications of vibratory rock polishers allows users to leverage their features effectively. Each scenario presents unique advantages and operational considerations, all of which contribute to the efficient polishing of stones.

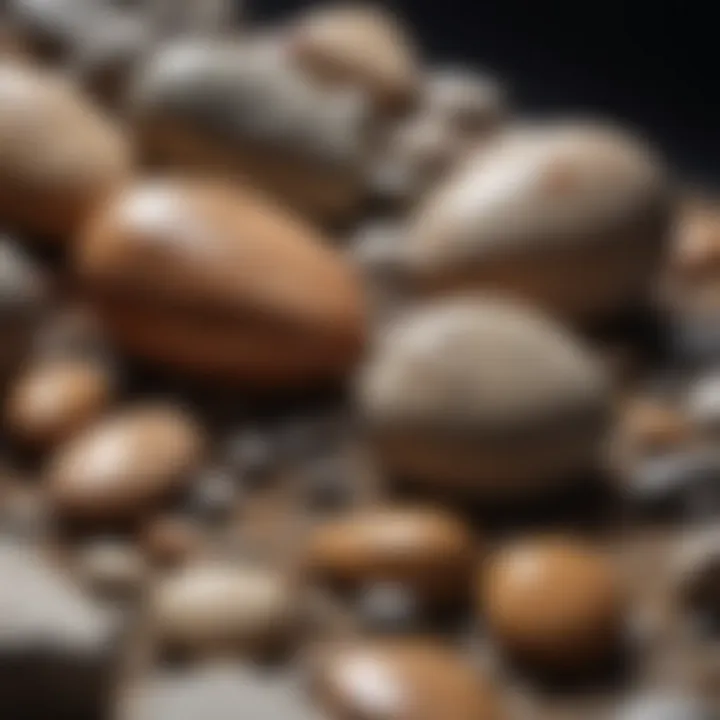
Environmental Impacts
The increasing popularity of vibratory rock polishers among hobbyists and professionals alike has led to crucial discussions about the environmental impacts associated with their usage. This section will delve into the practices and considerations needed to minimize the ecological footprint while maximizing the benefits of polishing rocks.
Waste Management Practices
Effective waste management is essential when using vibratory rock polishers. The abrasives and materials used during the polishing process can generate waste that may impact the environment. Here are some key practices to consider:
- Proper Disposal: Used abrasive media and slurry should not be simply discarded. Instead, research local guidelines for disposal or recycling of such materials. Many regions have waste management systems that can handle these kinds of products safely.
- Minimizing Waste: Consider using a specific amount of media and maintaining a careful approach to avoid excessive loss. It is possible to reuse some media, allowing for efficient operation without constant replenishment.
- Cleaning Procedures: After each polishing session, thorough cleaning of the workspace and equipment is vital. Dust and particles can become airborne and lead to pollution. Ensure that these materials are collected and dealt with appropriately to maintain a clean environment.
"Sustainable practices in waste management are not just beneficial for nature; they encourage responsible collecting habits in the rock polishing community."
Sourcing Sustainable Materials
Selecting sustainable materials is another aspect of reducing environmental impacts. This process explores both the media used for polishing and the rocks being processed. Here are aspects to consider:
- Eco-Friendly Products: Choose abrasives that are sourced in an environmentally friendly manner. Look for suppliers who prioritize sustainable harvesting and production methods. These products often have a smaller carbon footprint.
- Local Sourcing: When possible, sourcing materials locally can significantly minimize transportation emissions. This not only supports local businesses but also reduces the carbon emissions associated with long-distance transportation.
- Natural vs Synthetic: Evaluate the benefits of natural abrasives compared to synthetic ones. Natural materials may be less harmful to the environment, while some synthetic options can offer consistent performance. Strike a balance based on your specific polishing needs and ecological values.
By being mindful of waste management and material sourcing, enthusiasts can contribute positively to the environment while enjoying their hobby. This commitment to sustainable practices will ultimately foster a more responsible community among rock collectors.
Future Trends in Rock Polishing Technology
The evolution of technology in almost every industry impacts the tools and methods used by enthusiasts and professionals. In the realm of rock polishing, vibratory polishers stand as a testament to this trend. Staying attuned to future developments in rock polishing technology not only enhances the effectiveness of these tools but also expands the horizons for creativity and efficiency among rock and fossil collectors. Understanding trends such as innovations in design and digital integration can lead to a more refined and effective approach to polishing rocks.
Innovations in Design
Recent advancements in design focus on increasing the efficiency and effectiveness of rock polishing. Manufacturers are emphasizing compact designs that save space without sacrificing performance. These new models often incorporate improved motor systems that provide better vibration control and uniform energy distribution.
Other designs are also considering ergonomic principles, making machines easlier to use. User-friendly interfaces help collectors adjust settings quickly to suit specific polishing needs. Enhanced bowl shapes allow for better media movement and help prevent dead spots where rocks may not receive proper polishing. Collectors should be aware of these features when investing in a new polisher, as they can affect the overall outcome of the polishing process.
New materials are also being explored for the bowl and liner, which can impact durability and maintenance. For example, composite materials have emerged as alternatives that resist wear and tear better than traditional materials. These innovations not only extend the lifespan of the equipment but also contribute to the overall quality of the polished rocks.
- Key elements in design innovations include:
- Improved vibration control
- Ergonomic adjustments
- Advanced materials for durability
Digital Integration
The digital age brings a new dimension to rock polishing, enabling enthusiasts to leverage technology for better results. Digital integration encompasses the use of smart technology, allowing for heightened precision in adjusting polishing parameters. Collectors can now set and monitor cycles through mobile applications or built-in screens, giving them real-time feedback on performance.
Such capabilities enable more accurate fine-tuning of timing, vibration intensity, and rotation speeds, resulting in optimized polishing processes. The ability to store and analyze data from previous batches can inform future practices, leading to improved outcomes.
Moreover, digital integration can facilitate easier troubleshooting. Advanced sensors can detect anomalous vibrations or irregular performance, alerting the user before more serious issues arise. This leads to less downtime and more successful polishing sessions.
As the technology landscape continues to evolve, users must stay informed about these advancements. Embracing digital integration not only elevates the polishing experience but also fosters a deeper understanding of the factors that lead to superior results.
"Innovations in design and digital integration are not just trends; they reshape how collectors engage with their craft."
Regulatory Considerations
Regulatory considerations play a crucial role in the operation and use of vibratory rock polishers. Compliance with these regulations ensures the safe use of equipment, protects environmental integrity, and fosters a responsible approach to rock polishing practices. For enthusiasts and professionals alike, understanding these guidelines can enhance operational efficiency and reduce risks associated with improper use.
A strong emphasis on regulatory measures helps establish a baseline for best practices in the polishing industry. Adhering to safety standards can prevent accidents in the workshop, while environmental regulations mitigate risks of pollution and resource depletion. When hobbyists or commercial users are informed about the regulations, they can make better choices regarding equipment maintenance, material sourcing, and waste management.
Compliance with Safety Standards
Compliance with safety standards is essential for anyone operating a vibratory rock polisher. These standards may vary by region but generally include guidelines on equipment design, maintenance, and operator safety.
- Personal Protective Equipment (PPE): Using appropriate PPE, such as goggles and gloves, is vital to safeguard against flying debris and chemical exposure during the polishing process.
- Equipment Safety: Operations should include regular inspections to ensure all parts are functioning properly. This includes checking for wear and tear on the motor and the bowl.
- User Training: Proper training on the operation of the polisher can significantly reduce accidents. Workshops or online courses can be highly beneficial for novices or even seasoned users looking to refresh their knowledge.
"Adhering to safety guidelines helps create a safer working environment, protecting both the operator and the community."
Environmental Regulations
Environmental regulations are crucial for ensuring that rock polishing does not harm the ecosystem. As enthusiasts and businesses alike engage in this craft, it is essential to consider the environmental implications of their actions.
- Waste Management: Proper disposal of polishing media and waste materials is a primary concern. Participants should be educated on how to handle, store, and dispose of these materials responsibly.
- Sourcing Sustainable Materials: Users should prioritize sourcing polishing supplies that have a lower environmental impact. This includes selecting non-toxic abrasives and eco-friendly additives.
- Minimizing Waste: Implementing practices that reduce waste, such as re-using polishing media or employing recycling techniques, is increasingly becoming a standard in responsible rock polishing.
Overall, staying informed about regulatory considerations is vital for anyone involved in rock polishing. It not only enhances personal safety and environmental protection but also contributes to the sustainability of the hobby and industry as a whole. Understanding and following these regulations ensures that the vibrant world of rock polishing can continue to thrive.
Community and Resources
Understanding the role of community and available resources is crucial for anyone involved in using vibratory rock polishers. This segment offers insights into how such engagement fosters learning and sharing of best practices among rock collectors and enthusiasts. The vibratory rock polishing process can often seem solitary, but establishing connections within the community enhances knowledge exchange and troubleshooting capabilities. Participants can benefit from diverse experiences, leading to improved polishing techniques and outcomes.
Networking Opportunities
Networking within the rock polishing community serves several purposes. Engaging with fellow enthusiasts opens vistas to learn about new equipment, advancements in technology, and innovative polishing techniques. This also encourages shared experiences, where both novices and experts contribute their insights.
For example, joining groups on platforms like Facebook or forums such as reddit.com allows enthusiasts to interact, ask questions, and showcase their polished rocks. These connections can lead to:
- Collaboration: Partnering with others for larger projects, sharing tools, or participating in group events.
- Community Events: Attendance at rock shows or polishing demonstrations can vastly improve one’s skills and understanding of techniques.
- Mentorship: Experienced users are often willing to guide newcomers, providing personalized tips that accelerate the learning process.
Educational Resources and Workshops
Integrating educational resources into your polishing journey can significantly elevate your skill level. Workshops, both in-person and virtual, provide structured learning environments featuring hands-on experience and direct guidance from experienced instructors. Many local geology clubs offer workshops that focus specifically on the mechanics and techniques involved in using vibratory polishers.
Beyond workshops, there are also abundant online resources. Websites like Britannica provide foundational knowledge about rocks and minerals, while platforms like Wikipedia can offer insights into polishing techniques and materials used.
Additionally, engaging with instructional videos on various platforms can be beneficial. These visual aids can help users understand the nuances of setting up a polisher, selecting the right media, or diagnosing common issues.
In summary, the vibratory rock polishing community is a vital asset to anyone looking to improve their skills. Networking opportunities encourage sharing and collaboration, while educational resources and workshops provide the foundation and advanced techniques that are essential for success in the challenging yet rewarding world of rock polishing.
Closure
In this article, we have delved into the multifaceted world of vibratory rock polishers. Understanding this equipment is essential for anyone invested in rock and fossil collecting. The insights provided here offer valuable guidance on how to maximize polishing results and ensure the longevity of the tools in use.
Summarizing Key Insights
To summarize, vibratory rock polishers operate on principles of vibration and energy transfer, which enhance the polishing process. Key components such as tumbler design and media selection play crucial roles in achieving effective results. Additionally, advanced techniques such as customizing polishing cycles can significantly change the finish of the rocks processed. Maintenance practices are equally vital, as they prolong the operational life of the polisher, ensuring optimal performance.
Individuals engaging with their polishers will note the particular importance of safety considerations and proper handling of materials. As knowledge accumulates, the outcomes from using a vibratory rock polisher improve. By focusing on these aspects, collectors can effectively navigate the complexities of rock polishing.
Encouraging Exploration and Experimentation
Encouragement for exploration and experimentation is integral to the growth of skills in rock polishing. Each type of rock has unique characteristics, and trying different techniques can yield unexpected and rewarding finishes. Experimentation can involve varying polishing times or changing media types to observe the effects on different stones.
Moreover, joining communities and exploring educational resources can broaden understanding. Engaging with others in the field may introduce innovative ideas and techniques. Sharing insights and learning from experienced collectors can foster deeper knowledge and improve polishing results further.
"The journey of polishing rocks is not solely about achieving a perfect shine but also about the learning process and discovery that comes along with it."