Essential Tools for Cutting Rocks: A Detailed Guide
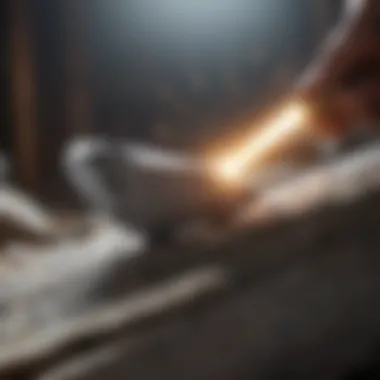
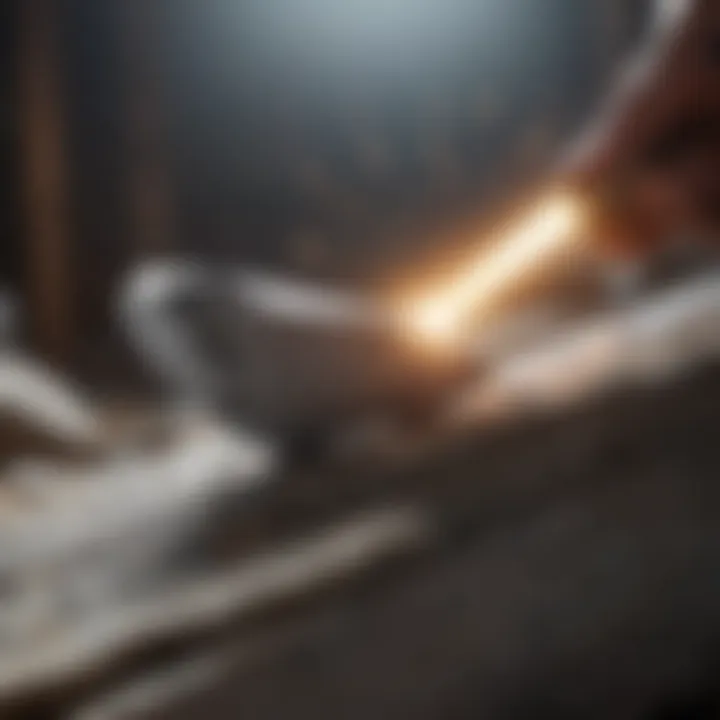
Intro
Cutting rocks is an age-old craft with evolving techniques and tools that cater to a variety of needs. From artistic pursuits like sculpture creation to practical applications in geology, the demand for precise and effective tools remains consistent. This article delves into essential instruments for cutting rocks, examining their specifications, appropriate uses, safety measures, and maintenance practices.
Understanding the available tools is crucial. Each instrument boasts unique features that make it suitable for specific tasks. An artist’s requirements differ starkly from those of a researcher gathering samples. Thus, selecting the right tool can greatly affect project outcomes.
The significance of rock cutting tools extends into both aesthetic and scientific realms. Artists transform raw materials into masterpieces, while researchers unearth geological information critical for understanding Earth's composition. This comprehensive guide aims to clarify the distinctions among various rock cutting tools and their best applications.
Readers will find a wealth of knowledge designed to enhance their effectiveness and efficiency in rock cutting. The following sections offer an insightful exploration of tools, helping users make informed decisions based on their project needs.
Featured Collectible of the Month
Overview
This month, we spotlight a remarkable rock tool: the diamond blade saw. Known for its exceptional cutting precision, the diamond blade saw utilizes diamond segments that provide superior durability. Ideal for both soft and hard rock, this tool caters to professionals and hobbyists alike who seek accuracy in their cuts.
Historical Significance
The use of diamond saws can be traced back to ancient civilizations, where artisans recognized the natural hardness of diamonds. Over centuries, advancements in technology have made diamond blades widely accessible. Their history reflects the innovations in material science and engineering that have shaped the rock cutting industry.
Identification Techniques
Visual Characteristics
Identifying the right tools starts with understanding their visual characteristics. Different rock cutting tools have distinct shapes, sizes, and materials used in their construction. For instance, a diamond blade has a smooth edge and a metallic core, while a chisel presents a sharp angled tip and a sturdy handle.
Resources for Identification
- Wikipedia: Offers a wealth of information about various types of rock tools and their uses.
- Britannica: Provides insights into the history and development of rock-cutting techniques.
- Reddit: Join communities focused on rock hobbies, where experienced collectors share knowledge.
- Facebook: Engage with groups dedicated to rock cutting and collecting to learn about tools and techniques from other enthusiasts.
"Selecting the right tool for cutting rocks can significantly improve both the process and the final product. Knowing the specific characteristics of each tool is essential for success.”
This guide serves as a foundation for understanding the essential tools used in rock cutting, setting the stage for deeper exploration into individual tools and techniques. We will proceed to examine specific tools next, ensuring you are well-equipped for your rock-related endeavors.
Intro to Rock Cutting Tools
Rock cutting tools are fundamental in various fields, from art to geological research. They enable individuals and industries to manipulate natural materials with precision. Understanding the types of tools available and their specific applications enhances the effectiveness of any rock-related project. This section will explore the value of knowing the cutting tools and the ultimate benefits they bring.
Understanding the Need for Cutting Rocks
Cutting rocks serves several purposes. Artists often wish to transform raw stone into sculptures or decorative items. Engineers might need rock cuts for construction projects, ensuring stability and safety. In geology, precise cuts can reveal internal structures or fossil content, critical for research. The varying hardness of rocks necessitates different tools that can accommodate specific requirements.
Being equipped with the right tools results not only in better outcomes but also in improved efficiency. It reduces time spent on projects and prevents damage to materials. Therefore, understanding the tools one requires is indispensable for success.
Historical Overview of Rock Cutting Techniques
Throughout history, the methods of cutting rocks have evolved significantly. In ancient times, rudimentary tools such as chisels and hammers were commonly used, often made from stone or metal. Techniques relied heavily on manual labor and basic understanding of material properties.
With the advent of the industrial age, new methods emerged. Mechanized tools became popular, increasing both speed and precision in cutting. The introduction of diamond tools in the late 20th century revolutionized the industry, allowing for cleaner cuts with less wear on the tools. Understanding these historical developments sheds light on the current options available and aids in appreciating advancements in technology.
"The evolution of rock cutting techniques showcases human ingenuity and adaptability in utilizing natural resources."
Today, rock cutting tools range from simple hand tools to sophisticated industrial machines. Each advancement brings unique benefits, catering to various needs. Knowing this history gives users insight into their tool choices, shaping their projects effectively.
Types of Rock Cutting Tools
The selection of appropriate rock cutting tools plays a crucial role in achieving the desired results in various projects, from artistic creations to geological research. Understanding these tools helps users make informed choices, ensuring both efficiency and safety. Each category of tools has its unique features, benefits, and operational nuances. By exploring hand tools, power tools, and industrial cutting machines, readers can gain a thorough insight into when and how to use each type effectively.
Hand Tools Overview
Hand tools for cutting rocks remain relevant in numerous applications, especially for small-scale projects. Their simplicity and effectiveness allow users to undertake detailed work without the complexity of powered machinery. Here, we examine three essential hand tools: chisels, hammers, and saws.
Chisels
Chisels are a vital tool for cutting and shaping rocks. Their primary aspect lies in the sharp, angled blade, which is designed to split stone precisely. This characteristic makes them a popular choice in sculpting and masonry. A unique feature of chisels is their adaptability to various stone types, such as granite or marble. However, they require manual force, which can limit effectiveness on harder rocks.
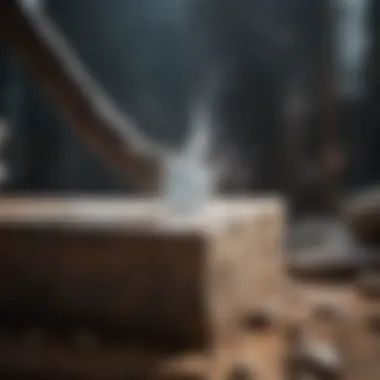
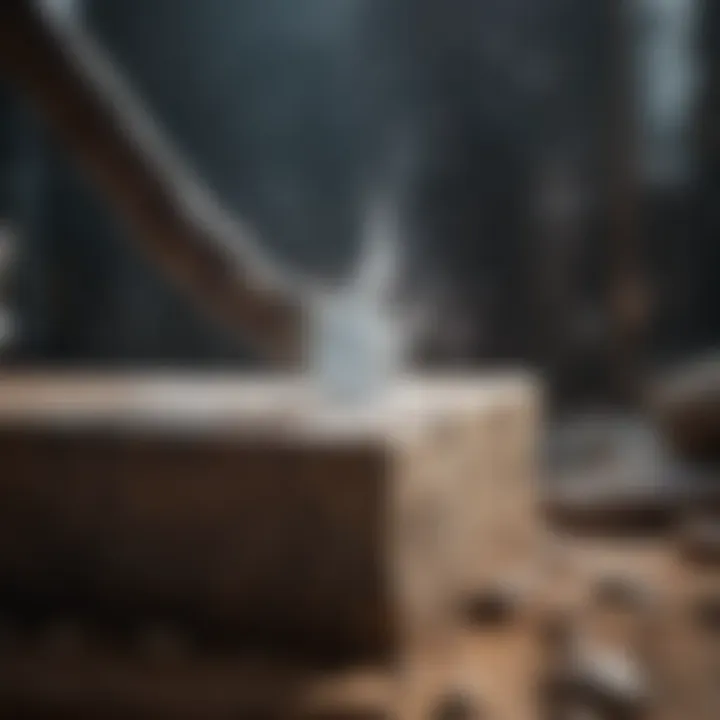
Hammers
Hammers serve as a companion tool for chisels, providing the necessary force to drive a chisel into the rock. The key characteristic of hammers is their weight, which can vary to suit different tasks. They are beneficial for initial rough cuts and breaking larger stones into manageable pieces. One advantage is the ability to control the striking force, but improper use may lead to accidents or inefficient cuts.
Saws
Saws designed for rock cutting come in various forms, suited for different cutting styles. Unlike chisels, saws allow for smoother edges and more refined cuts. A significant feature of saws is their blade design, which often incorporates diamond or carbide tips for enhanced cutting performance. While effective for precise work, saws can require more maintenance and careful handling compared to chisels and hammers.
Power Tools Overview
When more power and efficiency are needed, power tools become invaluable for rock cutting tasks. This section covers three prominent power tools: angle grinders, diamond wire saws, and rotary tools.
Angle Grinders
Angle grinders are versatile tools capable of cutting and shaping rock efficiently. Their key feature is the rotating disc that provides rapid cutting action. This makes angle grinders a popular choice for projects requiring speed and efficiency. The unique aspect is their ability to use various attachments; however, they can produce substantial dust and require proper safety measures to operate safely.
Diamond Wire Saws
Diamond wire saws are advanced tools designed for cutting stone with speed and precision. Their notable aspect is the diamond-embedded wire that cuts through rock effortlessly. This quality makes them beneficial for larger-scale projects, such as quarrying or block cutting. The disadvantage is the higher cost, which may limit their accessibility for casual users.
Rotary Tools
Rotary tools offer exceptional flexibility with their precise cutting abilities. The key characteristic of these tools is the high-speed rotation that allows for intricate detail work. They are beneficial for small projects, such as crafting and detailed sculpting. However, their capacity for larger cuts may be limited, making them less effective for heavy-duty tasks.
Industrial Cutting Machines
For large-scale operations, industrial cutting machines play a pivotal role. This section focuses on wet saws, bridge saws, and water jet cutters.
Wet Saws
Wet saws utilize water to cool the blade during the cutting process, significantly reducing dust and friction. Their essential aspect is the continuous water flow, which prevents overheating. Wet saws are beneficial for cutting harder materials like granite and quartz. However, they require access to a water source, which may limit their portability in some scenarios.
Bridge Saws
Bridge saws are engineered for precise straight cuts. Their key feature is a fixed blade that moves across a stationary stone, providing exceptional accuracy. They are ideal for large projects that demand consistency and precision. The downside is that they are usually bulky and require significant floor space.
Water Jet Cutters
Water jet cutters use high-pressure water mixed with abrasives to cut through rock. The unique feature is their ability to create intricate patterns without generating heat. This makes them beneficial in applications where material integrity is vital. However, the initial investment is high, and operational costs can also add up quickly.
Understanding the right cutting tool according to the project requirements allows users to achieve optimal results efficiently.
Technical Specifications of Cutting Tools
Understanding the technical specifications of rock cutting tools is vital for both efficiency and effectiveness in any rock-related project. These specifications can significantly influence the way tools perform. Various elements, such as material composition, operational parameters, and design features, contribute to how well a tool can handle different types of rock. There are many benefits to knowing the technical specifications, including the ability to choose the most suitable tools for specific tasks and to optimize the overall cutting process.
Material Composition and Its Importance
Diamond Blades
Diamond blades are notable for thier ability to cut through hard materials. They consist of metal cores that have diamond segments attached, lasered or sintered onto the edges. This structure provides exceptional durability and longevity, making them a popular choice in rock cutting. The key characteristic of diamond blades is their high cutting efficiency. They are particularly useful for cutting granite, marble, and other dense rocks. Unlike other types of blades, which may wear down quickly, diamond blades maintain their sharpness over extensive use.
However, they can be relatively expensive compared to other options. Their unique feature of having a segmented design facilitates heat dissipation, reducing the risk of damage during prolonged periods of cutting. This heat management is a major advantage you cannot overlook in terms of performance. On the downside, improper use can lead to chipping or burning of the material being cut.
Tungsten Carbide Tips
Tungsten carbide tips are another critical component in rock cutting tools. They are commonly used for bits and blades because of their density and hardness. The key characteristic is their ability to withstand extreme conditions without breaking or wearing out swiftly. Tungsten carbide is a beneficial choice when working with softer types of rock or when it is essential to maintain precision during cutting tasks. Their unique feature is the high resistance to wear, which results in long-term performance.
Nevertheless, tungsten carbide tips may not be as effective on very hard materials compared to diamond blades. This could be seen as a drawback in specific situations where harder rocks are involved. Even so, their affordability and effectiveness make them a popular choice in the rock cutting industry.
Operational Parameters
Operational parameters play a vital role in the effectiveness and safety of rock cutting processes. These parameters include cutting speed, RPM, and torque, which can vary according to different tools and materials.
Cutting Speed
Cutting speed is crucial in achieving optimal results during rock cutting. It refers to the speed at which the cutting edge of a tool moves across the material being cut. The key characteristic of cutting speed is that it affects both the quality of the cut and the tool's longevity. Choosing the right cutting speed can enhance both efficiency and accuracy in cutting. Furthermore, different materials require different speeds for effective cutting; for example, soft rocks may be cut at higher speeds compared to harder ones.
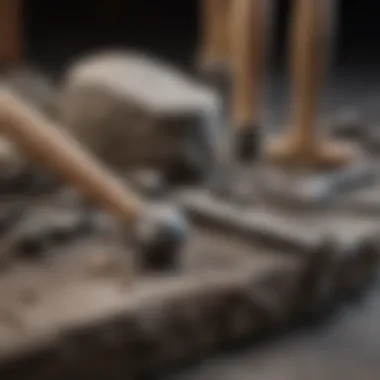
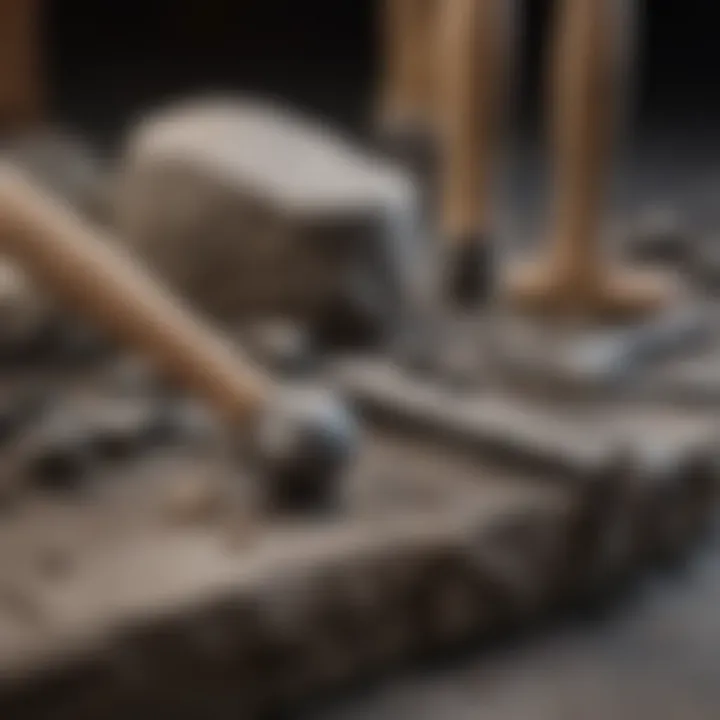
The unique feature of cutting speed is that it must be balanced with feed rate to avoid tool damage. If the cutting speed is too high, it can lead to excessive wear or failure of the cutting tool. Conversely, too low a speed may result in poor cuts. Therefore, careful consideration of the specific rock being cut is essential for optimal performance.
RPM and Torque
RPM, or revolutions per minute, is another critical operational parameter that influences cutting tool performance. This measurement indicates how many times the tool's cutting edge circles in a minute. High RPM can lead to faster cutting, but it can also increase the risk of overheating.
Torque, on the other hand, is the force that causes the cutting tool to turn. The key characteristic of torque is that it relates closely to the material being cut. Higher torque is usually needed for denser materials. The combination of RPM and torque is what makes the cutting process effective or not.
In terms of usability, both torque and RPM need to be optimized based on the tool and rock type. A major advantage of understanding these parameters is the opportunity for fine-tuning the cutting process, leading to more efficient operations. On the downside, incorrect RPM settings can lead to tool failure, which is both costly and time-consuming to rectify.
Safety Considerations When Cutting Rocks
Safety is an integral part of any activity that involves cutting rocks. Understanding the risks involved and taking appropriate measures can significantly reduce potential injuries. This section covers essential safety considerations that every individual should keep in mind when working with rock cutting tools. It emphasizes the importance of using protective gear and maintaining awareness of the dangers present while operating tools.
Personal Protective Equipment
Gloves
Gloves are an essential component of personal protective equipment (PPE) when cutting rocks. They protect the hands from sharp edges, abrasions, and impact injuries. A key characteristic of gloves suitable for rock cutting is their material; often, they are made of durable leather or synthetic fibers that offer both protection and dexterity. This combination makes gloves a beneficial choice for rock cutting activities, as they can enhance grip while reducing the risk of cuts.
Unique features of gloves include reinforced fingertips and cut-resistant linings, which can provide additional safety. While gloves significantly reduce the risk of injury, they may decrease sensitivity when handling smaller or delicate pieces. Hence, it is crucial to choose gloves that balance protection with the necessary tactile feedback.
Goggles
Goggles are another critical piece of protective equipment. They protect the eyes from flying debris, dust, and potential chemical splashes when using certain cutting tools. A defining characteristic of safety goggles is their ability to form a secure seal around the eyes. This seal ensures that no particles can enter during cutting operations. Goggles are a favorite among rock cutters due to their versatility and ease of use.
The unique feature of goggles is the anti-fog coating that many models come equipped with, ensuring clear visibility even in humid conditions. While they do a fantastic job at protecting the eyes, some users may find goggles uncomfortable if worn for extended periods, making it necessary to consider options that provide comfort as well as safety.
Respirators
Respirators are vital for any cutting activity that generates dust or fumes. They protect the respiratory system from inhaling harmful particles that may be released into the air. Key characteristics of good respirators include proper fit and effective filtration capabilities. These traits make respirators an essential choice for anyone involved in rock cutting, especially in environments where fine dust or chemicals are prevalent.
A unique feature of modern respirators is the availability of models designed specifically for different types of hazards. This includes particulate respirators and chemical respirators, which cater to various use cases. While they excel in providing safety, they can sometimes be uncomfortable during prolonged use. Thus, selecting the right respirator that meets safety standards while also being comfortable is essential for effective protection.
Handling and Operating Tools Safely
To ensure the safe handling of rock cutting tools, it's crucial to understand proper techniques and usage protocols. Operators should always be trained in the specific functions of the tools they are using. This includes selecting the right tool for the material and project, as well as following manufacturer guidelines.
Never attempt to operate a tool without understanding its functionality and safety features. Always inspect the tools before use to identify any wear or damage. Ensure workspaces are clean and organized to minimize the chances of accidents.
Common Risks and How to Avoid Them
Flying Debris
Flying debris is a common hazard when cutting rocks, especially with power tools. As the tool makes contact with the rock, fragments can break off and travel at high speeds. This can cause serious injury to the eyes and skin. Key characteristics include the unpredictability of debris direction and size, which makes it a significant concern for operators.
To mitigate risks associated with flying debris, it's crucial to always wear appropriate PPE, such as goggles and face shields. Setting up barriers or using dust suppression techniques can help contain debris and enhance safety.
Noise Exposure
Prolonged exposure to noise is another risk that often goes unnoticed. Rock cutting tools, especially power tools, can emit high-decibel sounds that may lead to hearing damage over time. A key characteristic of noise exposure is that it is cumulative; even short-term exposure can add up in damaging the ear.
To avoid noise exposure risks, wear hearing protection such as earplugs or earmuffs. It’s best to work in environments that allow for decreased sound levels whenever possible. Regular breaks during prolonged usage can also help manage noise fatigue.
Chemical Hazards
Chemical hazards may arise when using cutting tools that involve lubricants, solvents, or other materials that can produce harmful vapors. The key characteristic of chemical hazards is that they can be both immediate and long-term health risks. Understanding how to handle these chemicals safely is crucial.
Avoiding chemical hazards requires proper ventilation and using suitable respiratory protection. It's also important to become familiar with Material Safety Data Sheets (MSDS) for any chemicals in use. Maintaining a clean workspace by properly storing and disposing of chemicals will further minimize exposure risks.
Best Practices for Cutting Rocks
Cutting rocks demands precision and careful handling. Understanding the best practices enhances safety and improves results. Whether engaging in artistic projects or geological studies, following best practices ensures the right approach is applied to every rock cutting task.
Choosing the Right Tool for the Job
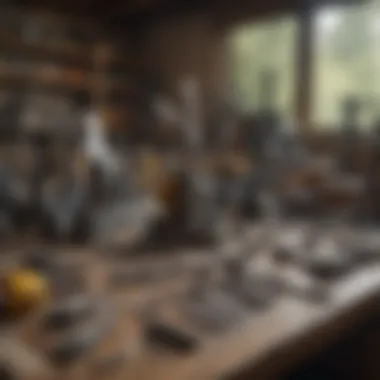
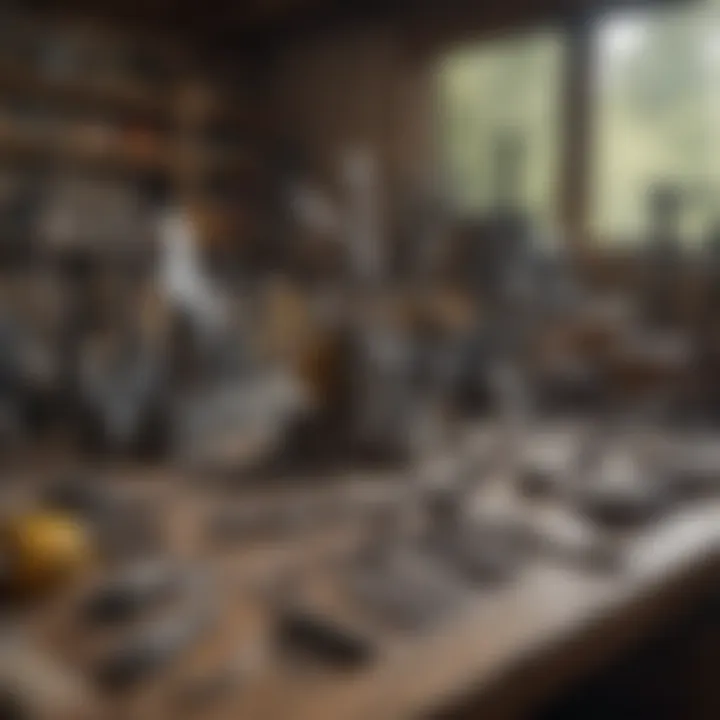
Selecting the appropriate tool is crucial. Each task demands different tool characteristics. For instance, if you are making small cuts, hand tools like chisels may be adequate. For larger projects, power tools or industrial machines become necessary. Consider the rock type as well. Hard stones may require diamond blades, while softer stones can be processed with standard blades. Choosing the right tool prevents frustration and increases efficiency in your work.
Techniques for Effective Cutting
Employing the right techniques significantly impacts the outcome of your rock cutting endeavors.
Angle and Pressure
The angle at which you cut influences both the quality of the cut and the tool's lifespan. Holding the tool at the correct angle reduces chipping and ensures cleaner lines. For example, a 30-degree angle can often yield optimal results depending on the rock. Additionally, applying the correct amount of pressure is vital. More pressure does not always lead to faster cutting. In fact, excess pressure can cause damage to the rock and the cutting tool. Therefore, being mindful of pressure allows for better control and precision in each cut.
Cutting Patterns
Establishing cutting patterns is essential, especially when working on larger pieces. Patterns help organize the cutting process and ensure that all parts are effectively addressed. For instance, a grid pattern can divide a large rock into manageable sections. This approach not only aids in systematic cutting but also enhances the overall efficiency of the project. However, one must be cautious of cutting too deep in one stroke. Moderate depths can reduce the risk of cracking and breaking, providing overall better integrity in the cut rock.
"Adopting best practices is not just about enhancing results but also ensuring safety for the cutter."
Understanding these fundamental aspects of cutting rocks empowers users. Knowledge about tool selection and cutting techniques brings both safety and efficiency to any rock-cutting project.
Maintenance of Rock Cutting Tools
The maintenance of rock cutting tools is a vital aspect of ensuring their longevity and efficiency. Proper care not only enhances tool performance but also reduces safety hazards during operation. Investing time in maintenance can prevent minor issues from becoming major ones, which could result in costly replacements or accidents.
Regular maintenance includes cleaning, sharpening, and inspecting tools for signs of wear. Each of these elements contributes to optimal performance, extending the useful life of the tools. Furthermore, a proactive approach to maintenance fosters a work environment that emphasizes safety, reliability, and productivity.
Cleaning and Storage Recommendations
Cleaning rock cutting tools after use is crucial for removing debris, dust, and any residues that could lead to corrosion or degrade the effectiveness of the tools. Tools should be wiped down with a dry cloth or brush to eliminate loose particles. A mild detergent can be used for tools exposed to concrete or stone dust. After cleaning, ensure the tools are completely dry before storage.
Storage is equally significant.
- Tools should be kept in a dry, dark place to avoid moisture damage.
- Hanging tools on pegboards or placing them in designated toolboxes can prevent physical damage and extend their lifespan.
- Avoid overcrowding as it increases the risk of tool damage and can make retrieval difficult.
Sharpening Cutting Tools
Methods of Sharpening
Sharpening methods play a crucial role in maintaining the cutting effectiveness of tools. Hand sharpening with whetstones offers precision and control, making it a favored choice for some users. On the other hand, bench grinders provide faster results but require more skill to avoid overheating the tool edges. The specific aspect of sharpening methods lies in achieving the right angle for optimal cutting performance. The key characteristic here is that each method has unique advantages depending on the tool and user experience.
Using a diamond sharpening stone is a beneficial choice because of its durability and effectiveness on tough materials like tungsten carbide. However, it can be an expensive option. In contrast, traditional whetstones are more economical but may require frequent replacement.
Frequency of Sharpening
Frequency of sharpening is another important consideration. Regular inspection of the cutting tools defines when they need sharpening. A good rule is to sharpen after a set number of uses, or whenever cutting performance noticeably declines. The key characteristic in determining sharpening frequency centers around assessing the tool's performance and cutting accuracy.
Typically, those who cut large volumes of material will find that tools dull quicker, necessitating more frequent sharpening. However, sharpening too often can lead to premature wear on the tools, compromising their structural integrity. Balancing these factors ensures efficiency without sacrificing tool lifespan.
Signs of Tool Wear and When to Replace
Recognizing the signs of tool wear is crucial to safe and effective rock cutting. Common indicators include visible nicks on blades, reduced cutting efficiency, and increased effort required during use. Additionally, excess vibration can signify wear, which could lead to tool failure if not addressed.
Replacing tools at the right time ensures that projects can proceed without interruption. Thus, understanding when tools have reached the end of their useful life is necessary for maintaining productivity and safety in rock cutting endeavors.
Remember: Maintaining tools not only preserves their function but also enhances safety for all users.
Culmination
In this comprehensive examination of rock cutting tools, we highlight the significance of understanding the various options available for those involved in rock and fossil collection. As the article outlines, each tool serves a unique purpose and is designed with specific materials and techniques in mind. Grasping these elements not only enhances the efficiency and effectiveness of the cutting process but also ensures safety during operations.
Summary of Key Points
The following key points summarize what we discussed in this article:
- Diversity of Tools: Tools range from simple hand tools like chisels and hammers to advanced machinery such as water jet cutters.
- Material Composition: The choice of materials, like diamond blades and tungsten carbide, dramatically impacts cutting performance.
- Safety Precautions: Employing proper Personal Protective Equipment (PPE), such as gloves and goggles, minimizes the risks involved.
- Maintenance Practices: Regular cleaning, sharpening, and monitoring for signs of wear are vital for prolonging tool life.
- Best Practices: Selecting the right tool and employing correct techniques ensure optimal cutting results.
Final Thoughts on Selecting and Using Rock Cutting Tools
When selecting rock cutting tools, consider the specific requirements of your project. Each tool has strengths and limitations based on its design and intended use. It is crucial to not only pick the right tool but also to understand how to use it optimally.
- Skill Level: Beginners may benefit from simpler, hand-held tools before advancing to more complex machinery.
- Project Type: Assess whether you require precision cutting for delicate tasks or robust tools for larger volumes.
- Environmental Conditions: Some tools perform better under specific conditions, such as wet cutting processes to manage dust and heat.
"Choosing the right tool greatly influences both the results and safety in rock cutting endeavors."
The overall goal should be to enhance both your skill and the quality of your work. By applying the knowledge gained from this article, you will be better equipped to make informed decisions, ensuring successful outcomes in your rock cutting activities.