Machines for Rock Cutting: Mechanisms and Applications

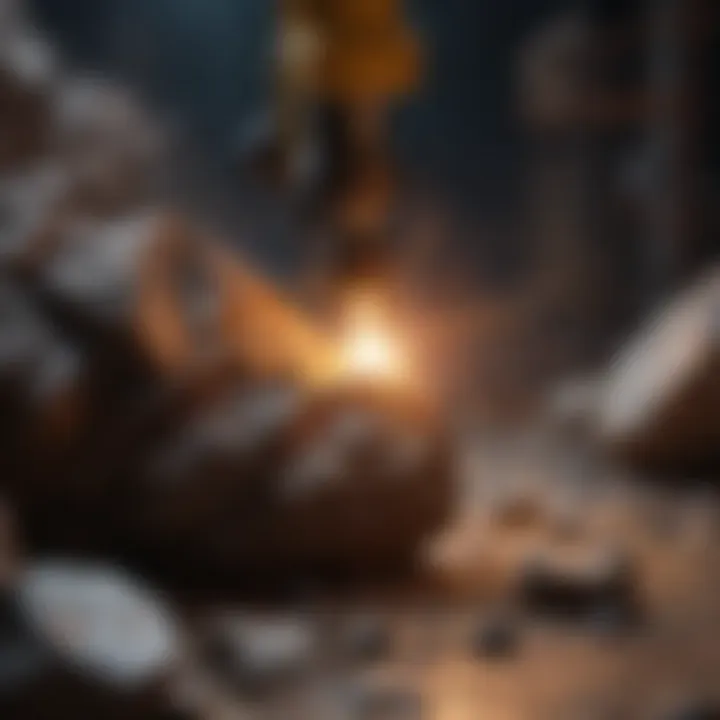
Intro
Rock cutting machines serve as a bridge between nature's unyielding landscape and the targeted manipulations of geology and construction. These machines transform rugged rock into usable material, whether it's for building infrastructure, extracting minerals, or enhancing collections of fossils. Understanding how these machines operate, their applications, and their evolution requires a closer examination. This journey will unveil the intricate interplay of technology and geology that defines the modern techniques and tools employed in rock cutting.
The significance of this exploration hinges not just on their current functionalities but also on how these machines have shaped industries over time. By examining their design, mechanisms, and the advancements that have driven their development, we gain insight into future possibilities.
Featured Collectible of the Month
Overview
As interest in rock and fossil collecting burgeons, it’s essential to keep an eye on significant collectibles that define the route for enthusiasts. This month, Petrified Wood captures our attention due to its unique composition and the story it tells about the earth's history. Comprising inorganic materials, this fossilized form of wood can reveal ancient climate conditions and biological systems, thus making it a fascinating subject of study and collection.
Historical Significance
Petrified wood has played a vital role in geology and paleontology. Its formation involves the gradual replacement of organic wood with minerals, typically silica, over millions of years. Collectors often find themselves mesmerized by the vibrant colors and intricate patterns unique to specific areas like the Petrified Forest National Park in Arizona.
The historical context stretches back to indigenous tribes who utilized petrified wood for tools and construction. In modern times, its discovery has helped scientists piece together our planet’s vast history. Collecting these specimens not only satisfies a personal hobby but also contributes to ongoing research in geology and evolution.
"Collecting rocks isn’t just a pastime; it’s an exploration of ancient stories that shaped our world."
Identification Techniques
Identifying various forms of stones, especially those like petrified wood, requires a keen eye and understanding of visual characteristics.
Visual Characteristics
- Texture and Patterns: The best approach is to observe the grain and color patterns. Petrified wood often displays a banded texture, which varies across specimens.
- Weight: Compared to regular wood, petrified wood is significantly heavier due to the mineral content, often feeling dense in hand.
- Color Variation: Natural variations can occur based on minerals present during its formation. These colors can range from vibrant reds to deep blues.
Resources for Identification
To further hone identification skills, enthusiasts can consult various resources:
- Books on Geology and Paleontology - These often provide visual guides and detailed descriptions of various specimens.
- Wikipedia - Offers a broad overview and specific entries on fossils and geology.
- Community Forums like Reddit - Engage with other collectors to exchange tips and insights.
- Britannica - A reliable source for historical and scientific information.
- Local Collectors' Groups on Facebook - These often host discussions and events, fostering a sense of community among enthusiasts.
Over time, understanding these machines and the materials they cut will not only enhance the experience for hobbyists but also preserve the ecological and historical narratives captured within each rock and fossil.
Prolusion to Rock Cutting Machines
Rock cutting machines represent a cornerstone technology in various industries, from mining to construction, where precise manipulation of geological materials is critical. The advent of these machines has transformed the ways in which professionals work with rock, allowing for efficiency and accuracy that manual methods simply cannot offer. This section aims to highlight the importance of rock cutting machines by exploring their overall impact and significance in today’s intricate world.
One of the primary benefits of utilizing rock cutting machines lies in their ability to enhance productivity. Traditional methods of cutting rock were labor-intensive and often led to inconsistencies in size and quality. With the machinery designed explicitly for rock cutting, operators can realize not only faster completion times but also maintain high standards of precision. Imagine cutting a granite slab for a countertop; the machine guarantees a consistent thickness and smooth edges, minimizing waste and reducing the need for subsequent manual finishing.
Moreover, these machines bring a level of safety that manual labor cannot match. Handling large and heavy rock pieces poses risks of serious injury. Rock cutting machines mitigate these dangers by mechanizing the process, enabling fewer human interventions during critical cutting operations. This shift allows workers to focus more on monitoring and less on strenuous physical labor.
But the considerations extend beyond mere efficiency and safety. Each rock cutting technology has been refined through continual innovation and understanding of materials. Modern rock cutting machines often use advanced cutting techniques tailored to the specific characteristics of the rock type. For instance, diamond wire saws offer superior performance on harder stones like granite or quartzite due to their precision and speed. Likewise, CNC rock cutting machines elevate the process by automating intricate designs, merging art and functionality.
As we delve deeper into this article, we will explore various types of rock cutting machines, the intricacies of their mechanisms, and the applications that underscore their importance in sectors like geology and construction. By comprehensively discussing these facets, we aim to provide a rich understanding that appreciates the technological advancements that have shaped the rock cutting landscape.
Types of Machines for Cutting Rock
In the realm of geology and construction, rock cutting machines play a pivotal role. Their very existence allows for not just the extraction of minerals, but also the crafting of architectural marvels from sturdy stones. Understanding the various types of machines available for cutting rock is essential, as each type comes with unique benefits and specific applications that cater to different project requirements. The advancements in these machines haven't just increased efficiency and precision; they have also heightened the safety and economic viability of rock cutting processes. Here we will discuss four main types of machines that stand out in the industry.
Diamond Wire Sawing Machines
Diamond wire sawing machines are indispensable in the world of rock cutting. Utilizing a wire embedded with diamonds, these machines slice through even the toughest materials with remarkable ease. The primary advantage of this technology is its efficiency—diamond wire saws operate faster and require less power than traditional cutting methods. Moreover, the precision obtainable with diamond wire saws minimizes waste, conserving valuable resources.
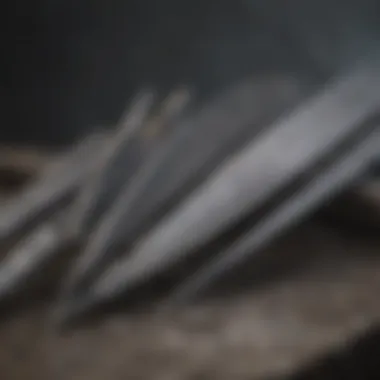
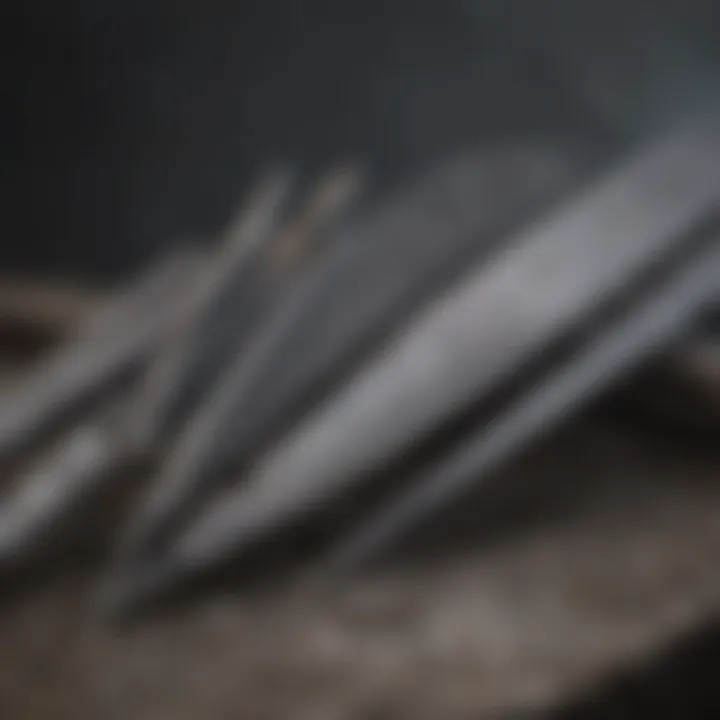
A notable feature of diamond wire saws is their versatility. They can be used to cut various materials, such as granite, marble, and concrete, making them a favorite among stone fabricators and quarry operators. The reduced vibration and noise levels also contribute to a safer working environment—a win-win for professionals. However, these machines require skilled operators to manage their intricate controls effectively, a factor to be considered when investing in such equipment.
CNC Rock Cutting Machines
Computer Numerical Control (CNC) rock cutting machines have transformed how rock and stone are processed, bringing a significant leap in precision and automation. These machines are guided by computer systems, allowing for intricate designs and repeatability that is hard to achieve manually. CNC machines enable operators to create complex shapes and patterns in the rock, which is crucial for industries such as architectural stone processing.
One of the main draws of CNC rock cutting machines is their ability to work around the clock, producing consistent results without fatigue. However, this automation comes with a price; proper programming and maintenance are critical for optimal performance. Additionally, operators must have a thorough understanding of the software controlling the equipment. As such, investment in training might be necessary to realize the full potential of these machines.
Hydraulic Stone Splitters
Hydraulic stone splitters represent a different approach to rock cutting, focusing on splitting rather than slicing. These machines generate force through hydraulic systems to split large blocks of stone along predetermined lines. What sets them apart is their capability to handle substantial blocks efficiently, making them incredibly useful in the quarrying sector.
The splitters are particularly advantageous in environments where precision cuts are less critical than achieving substantial quantities of material quickly. They work effectively with various types of stones, enhancing their utility across different projects. On the downside, the machine's nature means it can be less versatile compared to other cutting methods—fine details and intricate designs might not be achievable with this technology. Consequently, one must assess the intended application carefully when opting for hydraulic splitters.
Wet and Dry Cutting Machines
Wet and dry cutting machines offer another avenue for cutting rock, with each method providing distinct advantages depending on the material and environment. Wet cutting machines use water to cool the blade and reduce dust during the cutting process, making them ideal for materials like concrete and stone, where dust can become a health hazard.
These machines not only improve safety but also enhance cutting quality by minimizing heat, a common issue that can warp or damage both materials and cutters. In contrast, dry cutting machines prioritize speed and are often more portable. However, they generate significant dust, which necessitates additional safety equipment and measures to protect the operator's health.
When choosing between wet and dry cutting machines, factors such as the material, cutting environment, and safety protocols must guide the decision. Ultimately, understanding the specific requirements of a project will lead to more informed equipment choices, enhancing both productivity and safety.
Mechanisms Behind Rock Cutting
Understanding the mechanisms behind rock cutting is vital to grasping how different machines operate within geology, construction, and fossil extraction. These mechanisms influence efficiency, precision, and ultimately, the effectiveness of the work being done. By diving deeper into this area, one can appreciate how cutting techniques and advancements in material science play significant roles in the evolution of rock-cutting technologies.
Cutting Techniques and Their Efficiencies
When it comes to cutting rock, the techniques employed vary significantly. Each method comes with its own set of efficiencies, tailoring the approach to the type of rock being worked on and the desired outcome.
- Diamond Wire Sawing: This method utilizes a steel wire embedded with diamond segments. Its efficiency lies in the ability to make intricate cuts with minimal waste, which is particularly beneficial when precision is paramount. Diamond wire saws are ideal for slicing through extremely hard materials, such as granite or marble.
- CNC Systems: Computer Numerical Control (CNC) rock cutting machines offer high precision and automation. They enable intricate designs and replicable cuts. The efficiency here comes from reduced labor costs and a decrease in human error, making them suitable for projects requiring consistent results.
- Hydraulic Splitters: These machines rely on the power of hydraulics to create fissures in rock. The efficiency of this technique is in its speed and ability to manage thick slabs, with less risk of cracking or damaging the material. It’s particularly useful in quarrying.
- Wet vs. Dry Cutting: Each technique has its merits; wet cutting reduces dust and keeps tools cool, while dry cutting is often quicker but creates more debris. The choice between the two can significantly affect efficiency depending on the context of the job.
Ultimately, understanding the nuances of these methods helps users select the right technique for their specific needs, leading to better project outcomes.
Role of Material Science in Cutting Tools
Material science intricately shapes the tools used in rock cutting. The properties of the materials used not only determine their longevity but also their efficiency and effectiveness in various cutting processes.
- Tool Composition: Cutting tools often feature advanced composites and alloys designed to withstand extreme conditions. For instance, high-speed steel is favored in scenarios where heat resistance is critical, while carbide tips are known for their hardness, making them suitable for abrasive materials.
- Surface Treatments: Techniques like coating or carburizing enhance the performance of cutting tools. These treatments increase resistance to wear, which is crucial for maintaining efficiency over time.
- Research Advances: Continuous research and development within the field of material science push the boundaries of what cutting tools can achieve. Innovations such as nanotechnology could lead to the creation of lighter and stronger materials that reduce energy consumption during cutting operations.
"Advancements in material science not only extend the life of cutting tools but also enhance the precision of rock cutting, reinforcing the foundational aspects of rock manipulation."
Applications of Rock Cutting Machines
In the unfolding landscape of industry and science, rock cutting machines stand out as pivotal tools that transcend their basic function of slicing through solid stone. Their applications span various domains, from extracting valuable materials to artistic endeavors, thus playing a significant role in both economic development and cultural heritage. Understanding these applications not only highlights their versatility but also underscores their relevance in advancing technology and sustainability.
Mining and Quarrying
Mining and quarrying are perhaps the most apparent applications of rock cutting machines. In these sectors, efficiency is paramount. Machines like diamond wire saws and hydraulic cutters slice through granite, limestone, and quartz with precision that manual methods can’t match. This provides several advantages:
- Increased Efficiency: Machines operate faster than manual methods, significantly reducing extraction time.
- Cost-Effectiveness: Although initial investment might be high, the long-term savings in labor and time often outweigh these costs.
- Safety: Operating heavy machinery reduces the risk involved with manual rock extraction, a dangerous endeavor in many environments.
Moreover, the use of machines in these settings minimizes waste. When machines are calibrated correctly, they can cut thin slices of rock, leaving behind less debris and enhancing the yield of usable material. This is beneficial not only economically but also environmentally, as it lessens the need for excess resource extraction.
Architectural Stone Processing
In the world of architecture, rock cutting machines play a crucial role in crafting aesthetically pleasing structures. Architects and designers utilize a variety of stone materials, and machines help shape these into intricate designs suitable for facades, countertops, and sculptures. Key aspects of architectural stone processing include:
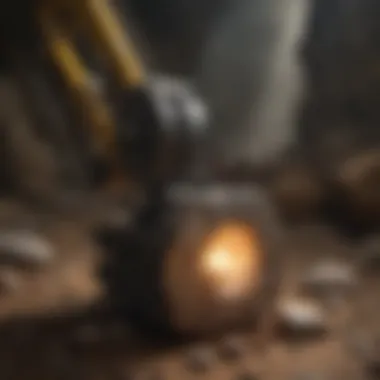
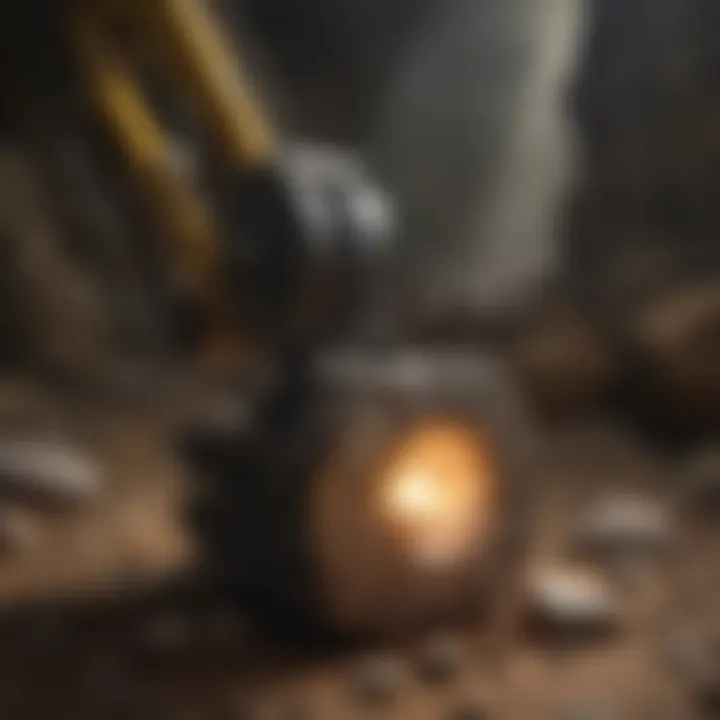
- Precision Cutting: CNC machines can be programmed to create detailed and complex shapes, allowing for creativity without compromising structural integrity.
- Finishing Techniques: Beyond cutting, machines also assist in finishing stones, giving surfaces a polished look that enhances their visual appeal.
- Material Variety: From marble to basalt, machines enable users to work with various types of rock, each having unique textures and colors, expanding artistic possibilities.
The importance of architectural stone processing cannot be overshadowed. A well-cut stone not only contributes to the building's aesthetic value but also its longevity, tying back to the skills of rock engineering through the ages.
Fossil Extraction Techniques
The extraction of fossils requires not just precision but also delicate handling. Here, specialized rock cutting machines come into play to ensure that the fossils remain intact during the extraction process. These techniques are particularly important because:
- Preservation: Fossils are often fragile, and machines like water jet cutters ensure that they can be removed from matrix rock with minimal damage.
- Efficiency in Discovering: Advanced rock cutting tools help paleontologists reveal more fossils in less time, enhancing research opportunities and scientific discoveries.
- Improved Analysis: With better extraction methods, studies can be carried out on fossils with great detail, leading to more accurate understandings of past life forms.
The intersection of technology and paleontology not only enriches our knowledge of prehistoric times but also indicates how rock cutting machines mold our understanding of our planet's history.
*"Rock cutting machines are more than just tools; they are bridges that connect our past with our present, offering us glimpses into both geological wonders and architectural marvels."
Historical Development of Rock Cutting Machines
The journey of rock cutting machines reflects an intersection of human ingenuity and the demands of our environment. This section digs into the historical trajectory of these machines that have transformed how we extract resources from the earth. The development of rock cutting technology is not just about the tools themselves but also illustrates the evolution of society's relationship with geological materials, offering insights that benefit both practitioners and scholars alike. Understanding this history is crucial for appreciating contemporary advancements and anticipating future innovations.
Evolution of Cutting Technologies
The quest to carve through stone is as old as humanity itself. Early techniques relied heavily on manual tools—think flint and later iron chisels. As civilization evolved, so did the understanding of geology and material properties. In the late 1800s, diamond-tipped tools started to gain traction. These tools, often fitted to circular saws, drastically improved cutting efficiency.
As we moved into the 20th century, innovation accelerated with the introduction of electrically powered machinery. This era brought hydraulic systems that allowed for greater force and precision in the cutting process. The emergence of Computer Numerical Control (CNC) machines in the late 20th century marked another significant leap. These machines offered unprecedented control and repeatability in cuts, enabling complex designs that were once inconceivable.
"The advancements in rock cutting technologies are a testament to human resilience—crafting tools not only to shape our environment but also to redefine our capabilities."
Milestones in Rock Cutting Engineering
Several key milestones in rock cutting engineering have punctuated its history:
- The Introduction of Electric Machines: The first electric saws came into play during the early 1900s, making cutting more efficient and less labor-intensive.
- Development of Diamond Wire Saws: The late 1980s saw the introduction of diamond wire saws, which revolutionized quarrying and made intricate stonework possible without traditional saw marks.
- CNC Technology Adoption: With CNC machines coming into the limelight in the 1990s, precise cuts allowed architects and engineers to push the boundaries of design while maximizing resource efficiency.
Each of these milestones illustrates a significant technological leap, laying the groundwork for today’s machines. Collectors of rocks and fossils benefit from these advancements as the tools of the trade evolve, allowing for more delicate and precise methods of extraction and preparation.
Overall, the historical development of rock cutting machines demonstrates a dynamic interplay between technology, industry needs, and scientific understanding. As we look back, we can appreciate how far we've come and what the future holds for this fascinating field.
Current Trends in Rock Cutting Technologies
The rock cutting industry is witnessing an exciting phase of evolution, where innovation and sustainability converge. As a vital part of geology, construction, and mineral harvesting, understanding these trends offers insight into how machines adapt to the growing demands of efficiency and safety. Here, we spotlight the two major currents shaping the machine landscape: automation, along with robotics, and sustainability efforts. These elements not only enhance operational efficacy but also align with contemporary environmental standards and industry best practices.
Advancements in Automation and Robotics
In the rapidly changing world of rock cutting, automation has become a game-changer. Machines are now equipped with state-of-the-art technologies that minimize human intervention, enhancing precision while maximizing productivity. Companies are integrating robotic systems that can perform repetitive tasks with minimal errors, a far cry from traditional methods that often relied on manual labor.
The integration of Artificial Intelligence (AI) plays a crucial role here. These intelligent systems analyze data in real-time, optimizing cutting paths and adjusting cutting speeds to adapt to varying rock hardness. This not only saves time but reduces wear and tear on cutting tools, resulting in longer service life and reduced costs.
Moreover, remote operation capabilities allow operators to control machines from safe distances, reducing workplace accidents. Imagine a rock cutting machine performing intricate cuts, all while an operator engages from the comfort of a control room, sipping their coffee. This shift demonstrates not just a trend in machinery, but a transformation in workplace dynamics itself.
Sustainability in Rock Cutting Practices
With the growing emphasis on environmentally responsible practices, sustainability is at the forefront of rock cutting technologies. The traditional methods often raised concerns about waste and resource depletion. However, modern machines are taking considerable strides toward greener operations.
One of the noteworthy developments is the use of water-efficient cutting techniques. These methods significantly lower water consumption, a critical factor in many regions where water scarcity is a pressing issue. By adopting water recycling systems, operators can not only reduce environmental impact but also cut costs. In addition, advancements in material science have led to the development of cutting tools that last longer and require less frequent replacement, reducing both material consumption and waste.
Furthermore, companies are increasingly adopting practices that ensure compliance with environmental regulations. Many now conduct rigorous assessments of the ecological impact of their operations, striving to mitigate harm and promote rehabilitation of areas disturbed by mining and cutting activities.
"Technological innovation is reshaping the rock cutting industry, enhancing efficiency while promoting sustainability."

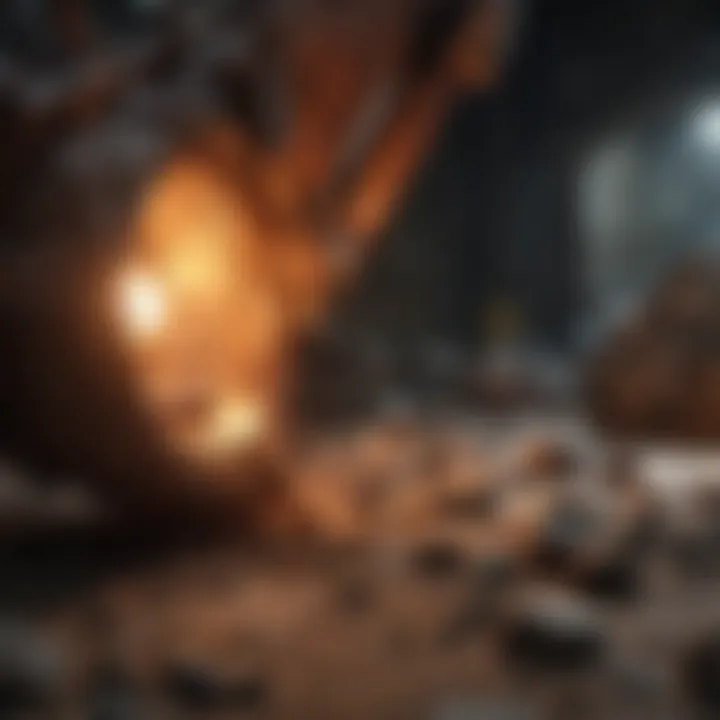
Future Directions in Rock Cutting
Considering the ever-evolving landscape of rock cutting technologies, the focus on future directions is paramount for various stakeholders. Knowledge about emerging trends and potential advancements helps both professionals and enthusiasts stay relevant in a rapidly changing industry. The integration of innovative technologies stands to enhance efficiency while ensuring safety and sustainability. Thus, this section seeks to elucidate the significant aspects that are shaping the future of rock cutting, including novel tools and intelligent systems that redefine operational capabilities.
Innovations on the Horizon
The realm of rock cutting is on the brink of significant transformation, driven by relentless innovation. One of the most exciting advancements includes the development of smart cutting tools that optimize performance through real-time data analysis. For instance, manufacturers are now experimenting with advanced sensor technologies that provide feedback on cutting parameters, such as speed and pressure. This data can then be analyzed to adjust the cutting process dynamically, which minimizes wear and tear on equipment while maximizing cutting precision.
Moreover, there is an increasing emphasis on eco-friendly cutting practices. Industry professionals are exploring alternatives to traditional fossil-fuel-powered machines, such as electric and hybrid models. These options tend to produce less noise and emissions, thus addressing concerns regarding environmental impact. Sustainable choices in rock cutting not only enhance public perception but also align with global movements toward greener technologies.
In addition to sustainability, the research into replacing conventional blades with diamond-coated lasers is another noteworthy innovation. Lasers possess the ability to cut through rock with remarkable precision and minimal dust creation. It’s an exciting prospect that stands to revolutionize the architecture and mining sectors by producing cleaner and more efficient cuts. The future is looking bright for these advanced tools and techniques.
Integration of AI in Cutting Processes
Artificial Intelligence (AI) is gradually making its presence felt across various industries, and rock cutting is no exception. The integration of AI into rock cutting processes could lead to unprecedented operational efficiency. For example, intelligent algorithms could predict equipment failure before it occurs, thereby reducing downtime and costs associated with repairs.
Furthermore, AI can enhance cutting strategy formulation by analyzing historical data to determine optimal parameters for each unique cutting situation. This can lead to improved material relief and increased productivity. As the algorithms learn from ongoing operations, it’s likely they will be able to make adjustments on-the-fly, pushing the boundaries of what is currently achievable in rock cutting.
In summation, the future of rock cutting is underpinned by innovations that include smart tools and AI-driven processes. As these advancements continue to unfold, they promise to deliver enhanced efficiency, sustainability, and safety. For rock and fossil collectors, staying informed on these developments is key to maximizing their endeavors in the field.
Safety and Environmental Considerations
Rock cutting involves powerful machines and techniques, presenting various challenges related to safety and environmental impacts. Understanding these considerations is essential for operators and managers, ensuring not only the protection of individuals involved in rock cutting but also the preservation of the environment surrounding the cutting site.
Addressing safety in rock cutting is a top priority, as the machinery can pose risks not just to the operators but also to nearby workers and passersby. The noise levels, the risk of flying debris, and the potential for accidents, such as slips, trips, or falls must be managed through strict protocols and the right equipment. Furthermore, compliance with relevant regulations ensures that the operations minimize hazards while maximizing productivity.
By integrating best practices into their routines, companies can protect their workforce and contribute positively to their communities. This proactive approach can lead to reduced accidents and improved morale and productivity.
"An ounce of prevention is worth a pound of cure."
This saying highlights that implementing safety measures is far more effective than dealing with accidents post-factum.
Best Practices for Safety in Rock Cutting
Implementing safety measures can drastically reduce risks associated with rock cutting. Here’s how:
- Personal Protective Equipment (PPE): Workers should always wear appropriate PPE, including helmets, safety glasses, ear protection, and high-visibility clothing.
- Regular Equipment Maintenance: Conducting frequent checks and maintenance of machines extends their lifespan and ensures they operate safely.
- Training: Ongoing education for workers on the operation of machines and emergency procedures is essential. This includes understanding all risks associated with the machinery.
- Safety Zones: Establishing exclusion zones around cutting operations can prevent unauthorized personnel from accessing dangerous areas.
- Accident Protocols: Clear procedures must be in place for handling accidents, including first aid measures and reporting guidelines.
By adhering to these best practices, organizations can foster a culture of safety that prioritizes the well-being of workers without compromising productivity.
Environmental Impact and Mitigation
The environmental footprint of rock cutting is another pressing concern. The activities involved can disrupt ecosystems, generate waste, and consume significant energy. However, measures can be taken to mitigate these adverse effects:
- Waste Management: Rock cutting often produces waste materials that can be disposed of improperly. Establishing effective waste management systems can minimize landfill contributions. Instead, recycling and reusing off-cuts can reduce waste.
- Water and Energy Conservation: Utilizing technology that promotes the efficient use of water and energy can help lower the environmental footprint. For example, high-efficiency machines can cut energy use while wet cutting can minimize dust and noise pollution.
- Dust Control: Dust generated from cutting can be a nuisance and a health hazard. Implementing dust control measures, like water sprays or dust suppression agents, can protect both workers and the surrounding environment.
- Environmental Impact Assessments (EIA): Before a rock cutting operation begins, conducting an EIA can identify potential negative effects on local ecosystems. This proactive approach helps in developing strategies that mitigate these impacts.
By adopting environmentally conscious practices, companies not only uphold their ethical responsibilities but also contribute to sustainable development in the industry.
In summary, prioritizing safety and environmental considerations in rock cutting aligns with both operational efficiency and responsible stewardship of technological advancements.
Culmination
Summary of Key Points
- Importance in Diverse Fields: Rock cutting machines have applications well beyond quarrying. They are crucial for archaeological digs, architectural stone processing, and fossil extraction. Each machine type has tailored functionalities that meet unique needs.
- Technological Advancements: The evolution of these machines is closely linked to advancements in technology. From diamond wire saws to CNC machines, each innovation enhances precision, efficiency, and safety during the cutting process.
- Safety and Environment: Understanding the safety measures is as vital as knowing the machines. Implementing best practices can mitigate risks while considering the environmental impact is essential in modern geology and construction.
- Future Prospects: The integration of AI and automation is set to revolutionize rock cutting, promising even greater efficiencies and reducing human error. Innovations on the horizon can further refine processes, pushing the boundaries of what is possible.
This article serves as a vital guide for rock and fossil collectors, engineers, and industry professionals to appreciate the complexities involved in rock manipulation and the relevance of these machines.
Final Thoughts on the Future of Rock Cutting
The future of rock cutting machines holds great promise as technology continues to evolve. With innovations in materials and automation, we can expect machines to become more efficient and eco-friendly. The potential integration of artificial intelligence systems can lead to smarter machines that predict wear and adapt cutting strategies in real time, reducing unnecessary material loss.
Moreover, as sustainability becomes a pressing concern, the industry will likely see a shift towards practices that minimize environmental impact. This could include the development of machines that operate with less noise and vibration, or that use water and air instead of harsh chemicals to reduce dust emissions.
As we look to the future, it’s essential that both enthusiasts and professionals stay abreast of these developments. With careful attention to safety and environmental considerations, the pursuit of effective rock cutting will continue to benefit not only industry operators, but also those passionate about rock and fossil collecting.