Exploring Lapidary Cutting Machines: A Comprehensive Guide
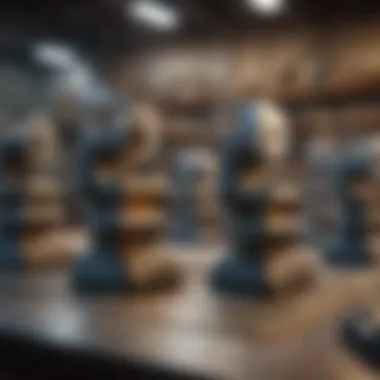
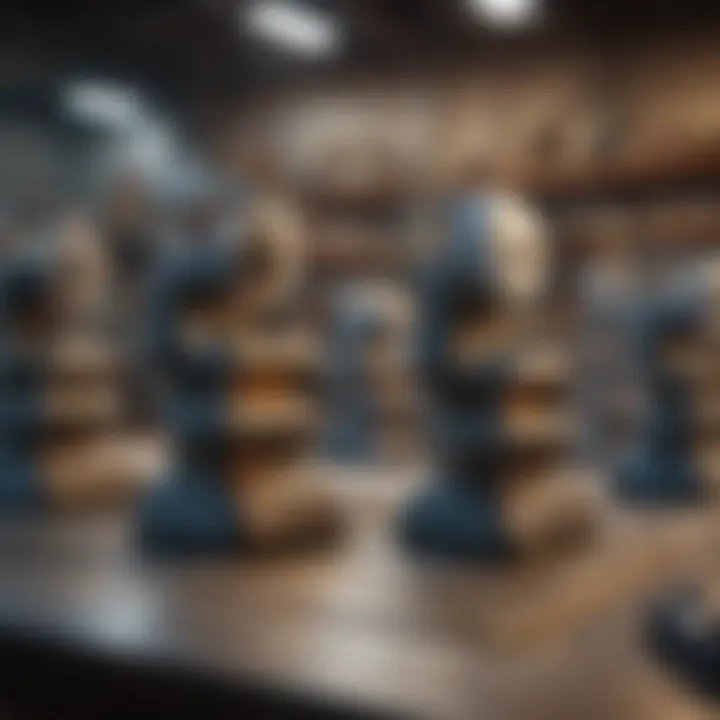
Intro
Lapidary cutting machines play an indispensable role in the world of gemstone and mineral collection, offering enthusiasts the ability to shape, polish, and craft exquisite pieces from raw stones. These machines are not just tools; they are gateways into a craft that blends art, science, and history. As many collectors find themselves drawn to this fascinating world, understanding the different types of lapidary machines available, their functions, and the techniques involved becomes crucial. This article unlocks the myriad possibilities that lay within the realm of lapidary work, ensuring that whether you're new to this art or a veteran in the field, you'll have the insights needed to make informed decisions about your tools and processes.
Having a comprehensive grasp of lapidary cutting machines not only enhances one’s collecting experience but also deepens appreciation for the intricate artistry that goes into crafting stunning gemstones. So, let’s embark on this journey to explore the machinery that brings nature’s beauty to life.
Featured Collectible of the Month
Overview
Every month, the lapidary community showcases a standout specimen that captures attention. This month, we spotlight the captivating Fire Agate. Known for its stunning concolorations and depth, Fire Agate isn't just a gem; it’s a narrative written in rock, ever-changing under the light. Its cutting requires precision and technique, making it an optimal choice for both budding lapidarists and seasoned experts. This versatile stone can be shaped into captivating cabochons or stunning beads, allowing for a wealth of creative possibilities.
Historical Significance
Fire Agate has a rich history that transcends borders. Native American cultures revered this unique stone, believing it held protective qualities. Furthermore, the geological formation of Fire Agate, characterized by its iridescence and intricate layers, showcases the raw power of volcanic activity. It's a testament to nature's artistry that beckons many lapidary artists to explore its depths further.
Identification Techniques
Visual Characteristics
Identifying quality gemstones like Fire Agate relies on keen observational skills. Key visual indicators include:
- Color: Varying from deep reds to subtle oranges and greens, each piece can present a spectrum when light hits it just right.
- Luster: Its shiny, almost glass-like finish can reflect the craftsmanship that has gone into polishing.
- Inclusions: Tiny imperfections or patterns within can increase its uniqueness, telling stories of its geological journey.
Resources for Identification
To further hone identification skills, collectors can utilize various resources:
- Books: Literature on gemstones often includes images and descriptions to help with recognition.
- Online Forums: Platforms such as reddit.com allow for community-driven discussions where enthusiasts can share tips and insights.
- Local Gem Shows: Meeting fellow collectors and observing specimens firsthand often deepens practical knowledge.
"Mastering the art of identification is like unlocking a secret door; each gemstone has a story waiting to be understood."
In this vibrant lapidary world, where tools and techniques converge, understanding the strengths and subtleties of lapidary cutting machines transforms an enjoyable hobby into an all-encompassing passion. Stay tuned as we delve further into the intricacies of selecting, maintaining, and operating these incredible machines throughout the article.
Prelims to Lapidary Cutting Machines
In the world of minerals and gemstones, lapidary cutting machines represent a critical juncture between raw natural beauty and artistic expression. These machines serve not just as tools for cutting, but elevate the mundane activity of shaping stones into a craft steeped in precision and creativity. As we delve into the numerous facets of lapidary cutting machines, it becomes evident that understanding their intricate workings not only empowers collectors and artisans but also enhances the appreciation of the gems themselves.
Definition and Purpose
Lapidary cutting machines are specialized instruments designed to cut and polish stones, transforming rough materials into polished gems ready for personal adornment or professional display. At their core, these machines encapsulate the blend of mechanical ingenuity and artistry that defines lapidary work. They offer a systematic methodology for achieving shapes and finishes unattainable by mere hand tools. Beginners may start with basic models, while seasoned collectors often invest in sophisticated types that provide advanced functionality.
The essence of these machines lies in their purpose—to unlock the potential of the stones. Using various cutting techniques, they shape and smooth stones, bringing out their unique colors and patterns. Each machine—from diamond blade saws to grinder-polishers—offers distinct advantages that meet diverse needs. This functionality allows lapidaries to adapt their approach based on the material being worked on as well as the desired outcome.
Historical Context
The lapidary art dates back thousands of years, with origins steeped in ancient cultures and civilizations who sought to harness the beauty of gemstones. While early lapidaries relied on rudimentary tools such as simple chisels and hand-held grinding stones, the development of mechanical machines transformed this art form dramatically. Initially, these innovations were simple contraptions but have since evolved significantly through the ages.
In the late 19th century, the advent of industrialization propelled the design and functionality of lapidary equipment. Factories began producing reliable cutting machines, which made lapidary work more accessible. By the mid-20th century, variations in styles and technologies proliferated, catering to both hobbyists and professional lapidary artists alike. Accessible equipment encouraged the rise of gemstone appreciation and collection that we're familiar with today, leading to a vibrant community devoted to lapidary arts.
As we explore the types, mechanics, and applications of these machines, it becomes clear that they stand as more than just tools; they are a bridge between nature’s bounty and human creativity.
Types of Lapidary Cutting Machines
Understanding the various types of lapidary cutting machines is crucial for any gemstone or mineral enthusiast. Each machine serves a distinct purpose, catering to specific needs in the lapidary process. Whether shaping a rough gemstone into a polished stone or preparing a fossil for display, selecting the right equipment can make all the difference in the quality of the final product.
When considering the types of lapidary cutting machines, it’s essential to weigh factors like efficiency, cost, and usability. Some machines offer unparalleled precision, while others provide flexibility for various tasks. A well-informed choice can lead to improved results and a more enjoyable crafting experience.
Diamond Blade Saws
Diamond blade saws are considered the workhorses of the lapidary world. They utilize a blade embedded with diamond particles, allowing them to cut through hard materials with ease. This makes them particularly effective for slicing through tough stones like granite or quartz. The durability of these blades ensures they stay sharp longer than standard blades, minimizing the frequency of replacements.
Using a diamond blade saw can significantly reduce the amount of time and effort needed to shape your stones. They produce cleaner cuts and enable lapidaries to create intricate designs that would be nearly impossible with other tools.
However, one should be mindful of the costs involved. While diamond blades can be pricier upfront, their longevity often makes them a worthwhile investment for serious collectors.
Wet Saws
Wet saws come equipped with a water reservoir that continuously cools the blade during cutting. This unique feature is not just a luxury; it’s a necessity when working with delicate or thin materials, as it significantly reduces the risk of cracking. The moisture also minimizes dust, creating a cleaner workspace that is safer for the operator’s lungs.
For those focusing on intricate designs and precision, a wet saw might be the ideal choice. They are particularly useful for intricate cuts in softer stones like opals or softer minerals that require a gentler touch. The downside is that these machines often require a more substantial commitment in terms of setup and maintenance. Users need to ensure that the water system is functioning properly to avoid issues while cutting.
Trim Saws
Trim saws fill a specific niche in lapidary cutting. They are ideal for making precise cuts in smaller pieces, perfect for trimming gems to a desired size or ensuring intricate details are properly defined. The saws operate at lower speeds than their larger counterparts, which provides the control needed for delicate work.
Although they might not handle larger stones, trim saws makes up for this by allowing lapidaries to focus on fine details. Collectors appreciate employing trim saws for finishing touches on their projects. Due to their compact size, they can fit in various workshop spaces, making them a practical choice for both amateurs and seasoned professionals.
Reverse Polishing Machines
As the name suggests, reverse polishing machines specialize in polishing rather than cutting. They provide a different function in the lapidary workflow by taking rough stones and giving them a smooth, shiny finish. The mechanism often involves a turning disc and polishing compounds that create an attractive sheen on the surface.
These machines excel at adding the final touch to completed pieces, instilling a sense of satisfaction in the lapidary. However, they can take some practice to master, as getting the right balance of pressure and timing is crucial for optimal results. A poorly executed polish can lead to a lackluster appearance, so one must tread carefully.
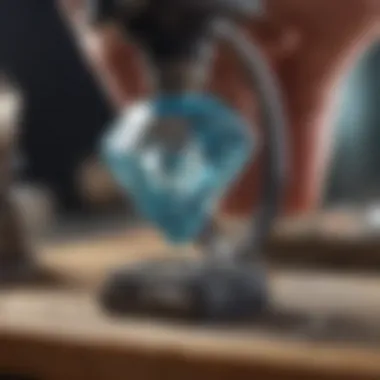
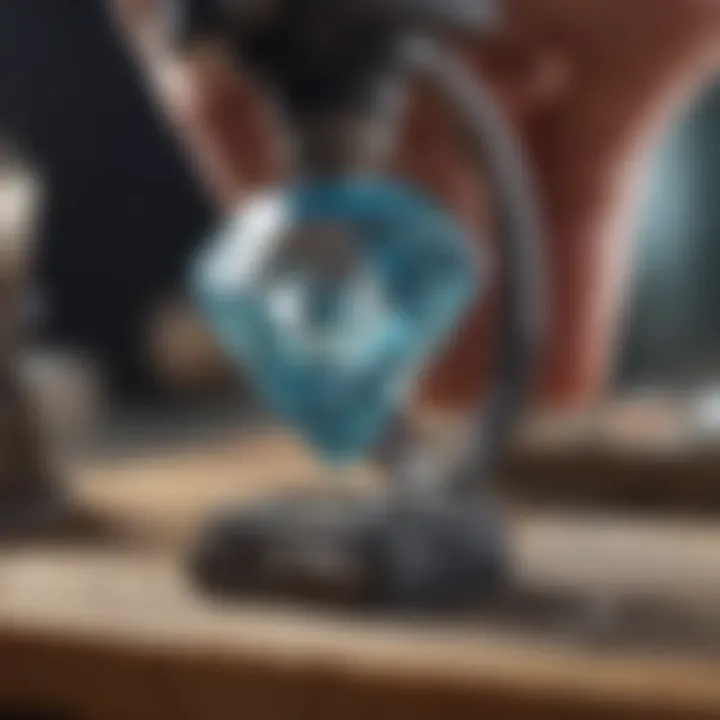
Grinders and Polishers
While similar to reverse polishing machines, grinders and polishers serve a broader purpose. Grinders remove material aggressively, reshaping stones before they undergo final polishing. On the other hand, polishers refine the surface further, achieving a mirror-like finish that truly highlights the stone’s natural beauty.
Investing in a grinder and polisher set can be a game-changer for gem enthusiasts. They allow for a more hands-on approach to shaping and finishing stones, inviting creativity. However, due to their two-in-one function, they often weigh more than dedicated machines and come with a slightly steeper learning curve.
In summary, understanding the different types of lapidary cutting machines empowers collectors to make educated decisions tailored to their specific needs. Each machine, with its unique capabilities, plays a pivotal role in the world of lapidary, driving the craft forward with every slice and polish.
Mechanics Behind Lapidary Cutting Machines
Understanding the mechanics behind lapidary cutting machines is crucial for both budding enthusiasts and seasoned collectors. This knowledge forms the backbone of effective gemstone crafting and satisfies the need for precision in creating stunning pieces. The subtleties in design, functionality, and performance can make a considerable difference in outcomes. Whether transforming raw stones into polished gemstones or preparing fossils for display, a solid grasp of how these machines operate enhances not only the user's skills but also the quality of the final product.
Understanding Abrasive Techniques
Abrasive techniques are fundamental to lapidary work, serving as the method through which materials are transformed into workable gemstones. In simpler terms, abrasives are the gritty materials that wear away the stone.
There is a range of abrasives used, from diamond powders to silicon carbide. Diamond is often favored due to its hardness—it's the toughest mineral on earth, making it well-suited for cutting through various materials. The effectiveness of cutting largely depends on the size of the abrasive particles. Finer particles can achieve a smoother finish, but they take longer to cut away material, while coarser particles are quicker but leave a rougher surface.
Moreover, the grit quality matters. You might think of it like choosing a knife; a dull knife won't get the job done, just as low-quality abrasives will struggle to cut through harder stones. Understanding the right balance between abrasive type, size, and quality enables lapidaries to select the appropriate methods for their specific projects. Here are a few points to consider:
- Grit Size: Coarse (60-150 grit) for shaping, medium (180-400 grit) for smoothing, fine (600-2000 grit) for polishing.
- Bond Type: Metal, resin, and ceramic bonds each have unique applications and durability.
- Cooling Methods: Using water or oil to cool the blade and reduce friction will help in maintaining blade integrity and prolonging its lifespan.
"Choosing the right abrasive is just like selecting the right tool for the job; it can make or break your work."
Motor and Blade Configurations
The motor and blade configurations play a vital role in the performance of lapidary cutting machines. At the heart of these machines lies the motor, which supplies the necessary power to operate the blades. It can make a significant difference in the cutting efficiency and the kind of stones you can work with.
- Motor Power: Generally measured in horsepower, a higher power rating enables faster cutting and allows you to work on harder materials. A motor with under one horsepower may struggle with tough stones, while those with over two horsepower can handle more demanding tasks.
- Blade Types: The choice of blade impacts not only the kinds of cuts you can achieve but also the smoothness of the finish. For instance, a diamond blade is excellent for hard stones but may not be ideal for softer materials like alabaster.
Blades also come in various thicknesses and lengths, tailored to specific cutting needs. Thicker blades offer durability but can be less flexible, while thinner blades provide precision but may wear down faster. When selecting a blade, be mindful of:
- Thickness: Thinner blades for intricate work, thicker for robust slicing.
- Tooth Design: Straight, serrated, or segmented teeth have impacts on the type of cuts made.
- Cooling Features: Blades equipped with cooling channels reduce heat buildup, preventing damage during prolonged use.
Understanding the delicate balance between motor specifications and blade types empowers lapidary workers to tailor their machines to diverse challenges, ultimately enhancing their craftsmanship. As the field of lapidary work evolves, keeping an eye on innovations in these structures can offer even greater efficiency and precision.
Applications of Lapidary Cutting Machines
The versatility of lapidary cutting machines is one reason they hold a privileged position in the hearts of gemstone aficionados and hobbyists alike. From crafting exquisite jewelry to enhancing scientific study, the applications extend far beyond mere cutting. Understanding these applications illuminates the significance of these machines in the lapidary world, enhancing not only the aesthetic appeal of stones but also their functional uses.
Gemstone Shaping
When it comes to gemstone shaping, lapidary machines are not just tools; they are extensions of the creator's imagination. With a diamond blade saw or a wet saw, enthusiasts can transform unyielding raw stones into beautifully polished gems. The initial shaping process is crucial; the angles and cuts can significantly affect the gemstone's final appearance and brilliance.
These machines allow users to work on diverse materials ranging from softer stones like turquoise to the more robust quartz. Each type demands specific techniques, ensuring that the gem retains its structural integrity while achieving the desired aesthetic. This shift from raw to refined emphasizes not just skill, but also a deep knowledge of materials.
Key Considerations in Gemstone Shaping:
- Accuracy: Precision in cuts enhances the beauty of the final piece.
- Tool Selection: Different saws cater to different hardness levels in stones.
- Skill Level: Each enthusiast’s expertise will influence the shaping process.
Fossil Preparation
Fossil preparation is another fascinating application for lapidary machines, enabling collectors, archaeologists, and enthusiasts to reveal nature's ancient secrets. The preparation process often involves delicate work, benefiting greatly from the versatility of wet saws and grinders. Here, precision is paramount, as the goal is to preserve the integrity of a fossil while also highlighting its unique features.
The techniques employed in fossil preparation differ from those in traditional gemstone shaping. Fossils may require more gentle handling, as the materials can be brittle or fragile. With the right lapidary tools, one can uncover remarkable details within a fossil, breathing life into something that’s been hidden for millions of years. This not only adds academic value but also enhances aesthetic appreciation.
Key Benefits of Fossil Preparation:
- Preservation: Maintaining the original structure of the fossil is crucial.
- Clarity of Detail: Lapidary techniques improve visibility of the fossil's features.
- Educational Value: Well-prepared fossils can serve as valuable teaching tools.
Artistic Stone Work
Artistic stone work allows lapidary cutting machines to shine in creative domains. Artists can utilize these tools to stretch their imaginations, crafting objects ranging from sculptures to functional art pieces. The aesthetic appeal of art is elevated through the meticulous shaping and polishing that these machines facilitate.
The techniques employed in artistic stone work can lead to intricate designs, where every cut tells a story. For instance, a lapidary artist might take advantage of a reverse polishing machine to achieve a mirror-like finish, allowing the beauty of the stone to radiate under different lighting conditions.
Considerations in Artistic Stone Work:
- Innovative Techniques: Blending different materials can create unique story pieces.
- Focus on Detail: Precision cutting and finishing techniques are essential.
- Material Choice: The choice of stone can vastly alter the overall effect.
"The true craftsmanship lies not just in what you create, but in how you interpret the stone itself."
In summary, the applications of lapidary cutting machines are broad and impactful. Whether shaping gemstones, preparing fossils, or delving into artistic stone work, these machines play a crucial role in transforming raw materials into treasures. For rock and fossil collectors, the ability to apply these techniques can significantly enhance both their collections and the appreciation for the art involved.
Selecting the Right Machine
Choosing the right lapidary cutting machine can make or break your entire stoneworking experience. It goes beyond just picking a shiny piece of equipment; there are numerous factors to consider. Each machine serves its purpose, yet not every tool fits every task. Therefore, understanding your specific needs and preferences becomes crucial for achieving successful lapidary outcomes.
Factors to Consider
When it comes to selecting the ideal lapidary machine, a handful of vital factors can guide your decision. These considerations ultimately influence your ability to work effectively and the quality of the results you’ll achieve.
Materials Used
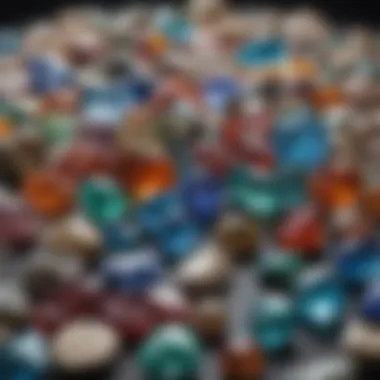
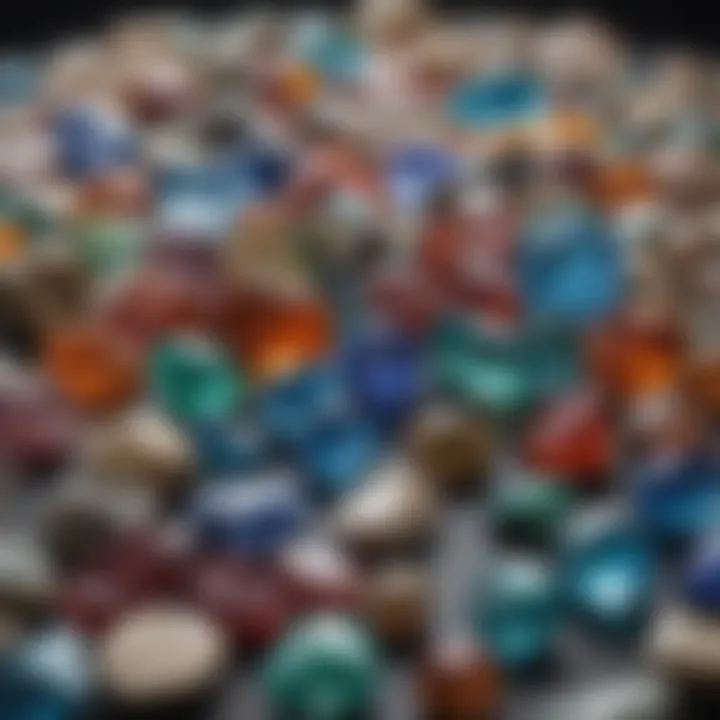
The kind of materials you'll be working with significantly affects your choice of machine. Certain stones, like soft agates, can be cut with less aggressive machines, while harder gems like sapphires require more robust tools. Using specialized blades tailored for specific materials is a common practice that can save time and decrease frustration. The key characteristic of materials in this context is hardness, as it often dictates the type of machine needed.
For instance, resin-bonded blades are particularly effective for softer materials, while diamond blades shine with tougher stones. Choosing the right material blend improves not only cutting efficiency but also prolongs the lifespan of your equipment, leading to greater satisfaction in the long run.
Budget Constraints
Ah, the budget—a frequent party pooper in the world of lapidary work. Determining how much you're willing to spend can narrow down the options significantly. Machines range from inexpensive entry-level models to high-end industrial versions. You need to assess what you can afford while also considering the returns on your investment.
A good rule of thumb is to remember that you often get what you pay for. Cheaper machines might initially seem appealing, but they may lack durability or precision. This can lead to additional costs down the line, which may quickly overshadow your savings. Finding a balance between quality and cost is essential.
Space Availability
Space can sometimes feel like a luxury in specialized workshops. The dimensions of your workspace must coincide with the machine size. Some machines can be impressively hefty, requiring not just floor space but also adequate ventilation and power supply placements. A cluttered work area can impede both safety and efficiency.
Consequently, knowing your layout ahead of time can help in choosing a machine that fits without crowding your space or making the environment unsafe to work in. Wall-mounted grinders might work wonders for those short on floor space, but they can add a level of complexity in installations and accessibility.
Popular Brands and Models
Now that you may have a better grasp of factors to consider, it’s also useful to get acquainted with reputable brands in the lapidary industry. Each brand tends to offer unique features that target various needs within the craft.
Some popular choices include:
- Tile saws from MK Diamond for their high accuracy and reliability.
- Gemstone polishing machines by Covington Engineering, known for their robust construction.
- Grinders from Your Brand, well-regarded for their user-friendly design.
These brands each bring their specialties to the table. The right model can ensure longer-lasting performance and, ultimately, a more satisfying lapidary experience.
Selecting the right lapidary cutting machine is not merely a task; it’s an art. The more attention you pay to the details, the better your results will be.
Maintenance of Lapidary Cutting Machines
Taking care of lapidary cutting machines isn't just a good habit; it's essential for their longevity and performance. Proper maintenance practices ensure that these valuable tools operate at their best, allowing enthusiasts to work seamlessly on their projects. If you're engaged in the craft of lapidary work, overlooking maintenance can lead to frustrating results. It could also escalate costs by necessitating repairs or even replacements of equipment too soon.
Not only does regular upkeep extend the life span of your machines, but it also enhances safety for the operator. Moreover, when machines are well-maintained, they provide the desired precision in cutting and polishing, leading to better results in your gemstone creations. A clean and properly functioning machine helps one achieve smoother finishes and sharper cuts, which are crucial in lapidary arts.
An understanding of effective cleaning procedures and blade maintenance is vital. These methods don't just keep your tools looking shiny and new—they play a pivotal role in the functionality and efficiency of the machines.
Regular Cleaning Processes
A routine cleaning schedule is a fundamental aspect of maintaining lapidary tools. The accumulation of dust, debris, and residue from the cutting process can hinder performance over time. Here are a few steps to follow for effective cleaning:
- Daily Wipe Down: After each session, take a moment to wipe down the machine's surfaces using a soft cloth. This helps remove particles that could scratch or damage the surface over time.
- Deep Clean Weekly: Once a week, conduct a more thorough cleaning. Disassemble parts that easily come off and clean them separately to reach every nook and cranny. Use warm water and a gentle detergent to avoid potential corrosion.
- Check for Residue: Pay particular attention to the blade area and any grooves where dirt can build up. A build-up may obstruct precision cutting, leading to less-than-ideal results.
- Lubrication: Regularly lubricate moving parts as per manufacturer instructions to ensure smooth operation and reduce wear.
These processes are not just time-consuming tasks but are essential activities that contribute significantly to the machine’s overall efficiency.
"A clean machine is a happy machine; it’s as simple as that!"
Blade Replacement and Care
A blade is arguably the heart of a lapidary cutting machine. Giving attention to blade replacement and proper care affects the overall quality of your cuts and the timing of machine usage. Here are some considerations:
- Recognizing Wear and Tear: Knowing when to replace blades can save you from mishaps while working. Look for signs of dullness or frayed edges. If the results of your cuts begin to appear ragged or rough, it might be time for a change.
- Choosing Quality Blades: Not all blades are made equal. Invest in high-quality blades that are appropriate for the type of material you are cutting. Different materials require different blade specifications.
- Proper Installation: When replacing blades, ensure that they are installed correctly. Follow the manufacturer's guidelines carefully to avoid any safety issues or damage to the machine.
- Storage of Blades: Store blades in a dry place and clean them after use. Utilizing blade protectors can prevent accidental nicks and preserve their lifespan.
Maintaining your machine and its components with these steps in mind can transform an amateur stone enthusiast into a polished artisan.
Safety Considerations
When engaging in any lapidary activities, safety takes the front seat in ensuring a smooth, successful, and injury-free experience. The nature of cutting and shaping stones comes with inherent risks, such as flying debris and exposure to harmful dust. Understanding safety considerations not only protects individuals but also enhances the quality of work produced. This section delves into protective gear, which is paramount for safeguarding oneself against these hazards, as well as workshop safety protocols that establish a secure working environment.
Protective Gear
Goggles
Goggles are non-negotiable when it comes to lapidary work. Their primary role is to protect the eyes from particles that can fly off during cutting or grinding processes. It's easy to underestimate this piece of equipment until something happens, like a small rock fragment hitting the eye. The key characteristic of goggles is their ability to create a comprehensive barrier — unlike regular glasses, they fit snugly around the face and prevent foreign materials from slipping in.
One unique feature of many modern goggles is the anti-fog property. This gets rid of the annoyance of fogged lenses during extended tasks, allowing for a clear view of intricate details as they are cut or polished. While some may consider goggles optional, the reality is that neglecting this gear could lead to severe injuries requiring medical attention. Investing in quality goggles is not just smart, it's essential.
Respirators
Respirators serve a different yet equally vital purpose in lapidary work. They help protect individuals from inhaling harmful dust and particulates generated during the cutting and shaping of stones. The key characteristic of respirators lies in their filtration systems which can filter out fine dust, ensuring cleaner air during operation. For anyone working in a space where stone dust is a regular occurrence, a good respirator becomes a beneficial companion.
A unique aspect of some respirators is their replaceable filters. This feature allows users to maintain and adapt their equipment to various types of stones, effectively controlling exposure to potentially harmful dust. Nonetheless, it's crucial to ensure the proper fit of the respirator for it to function effectively, otherwise the ability to filter out contaminants becomes compromised. Proper education and awareness around their usage can make a significant impact on health over time.
Workshop Safety Protocols
Creating a safe workspace does not end with personal protective equipment. Implementing workshop safety protocols is equally critical. Here are a few key points to consider:
- Ventilation: Ensuring that the workspace is adequately ventilated can drastically reduce exposure to harmful dust and fumes.
- Organizational Practices: Maintaining a clutter-free workspace reduces the chances of accidents and provides a focused area to work in, minimizing distractions.
- Emergency Preparedness: Knowing the location of first-aid kits and having a clear plan for emergencies can make a difference in critical situations.
Techniques in Lapidary Work
Lapidary work isn't just about cutting and polishing stones; it’s an art form that requires skill and knowledge of various techniques. As the world of gemstones and minerals continues to flourish, these techniques become ever more significant. Understanding how to execute these methods accurately can make a substantial difference in the quality of the final product, whether you're shaping a prized gem or crafting a unique piece of art.
Basic Cutting Techniques
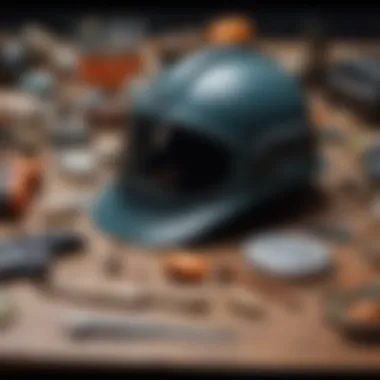
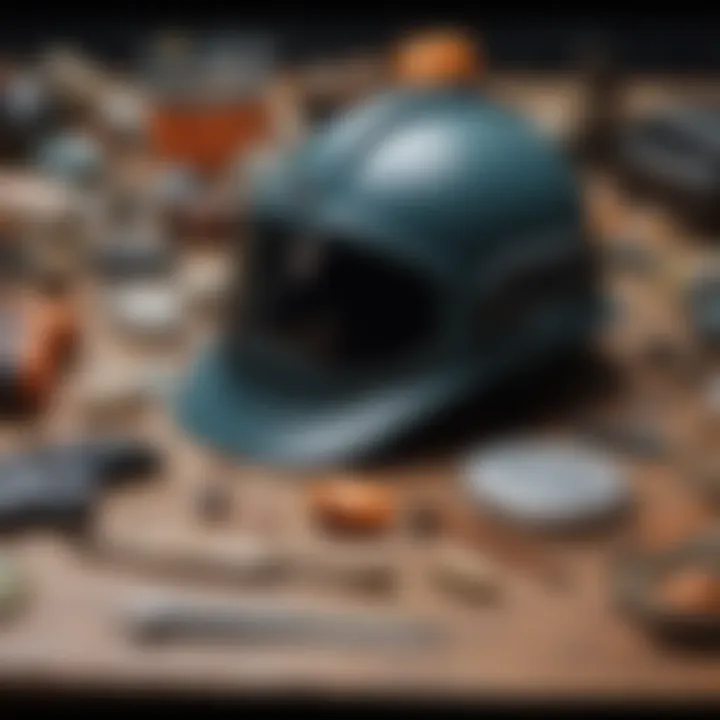
Cutting gemstones can seem daunting, but there are fundamental techniques that every lapidary should master. Here’s a closer look at some of the core methods:
- Sawing: Often the first step, sawing involves precise cuts to remove excess material. Utilizing tools like diamond blade saws, lapidaries can split stones smoothly to prepare them for shaping.
- Grinding: After sawing, the next step often involves grinding the edges. This process helps refine the stone’s shape and prepares it for polishing. A good grinder can’t be overlooked, as it determines the ease with which one can achieve the desired shape.
- Shaping: Here, lapidaries sculpt the stone using specialized grinding wheels. Each wheel has a different texture and grit, allowing for gradual refinement of the stone’s shape and surface.
"Mastering basic cutting techniques is like laying the foundation of a house; without it, other levels collapse."
Together, these techniques help to prepare the stone for the next phase: polishing. Understanding the nuances of each technique is crucial, as this knowledge can prevent costly mistakes and enhance the quality of the work produced.
Polishing and Finishing Techniques
Once the cutting process is complete, polishing brings the stone to life, leading to that brilliant gleam that aficionados admire. The right approach can elevate a rough stone to a stunning gem, showcasing its color and allure. Key methods include:
- Cerium Oxide Polishing: Often regarded as a holy grail among lapidaries, cerium oxide is used to achieve a glass-like finish on quartz and glass-like surfaces. This powder, when mixed with water, creates a slurry that can be applied to polishing wheels.
- Leather Pads: These pads can be used with polishing compounds to buff and shine areas that require more attention. This technique is ideal for achieving that ultimate shine on softer materials.
- Buffing: This process adds the final touch. Using a buffing machine with various compounds helps to smooth the surfaces of the stone, enhancing its luster. Different compounds create different finishes, tailoring the result to the stone's unique properties.
Mastering these polishing techniques can not only boost the aesthetic appeal of the stones but also protect them from future wear and tear. Each finisher holds its own value, preserving the beauty of the stone for generations to come.
In summary, the techniques involved in lapidary work require precision, patience, and a willingness to learn. From basic cutting techniques to intricate polishing methods, every step contributes to the final product’s beauty and functionality. Accumulating knowledge in these areas empowers rock and fossil collectors to not only appreciate the art form but also to create works that truly reflect their vision.
Challenges in Lapidary Cutting
In the intricate world of lapidary cutting, enthusiasts often face hurdles that can make their journey quite an endeavor. Understanding these challenges is crucial for those involved in this craft. Whether you're a hobbyist, a collector, or someone looking to create stunning pieces, being aware of potential pitfalls and limitations is something that could save you time, resources, and frustration in the long run.
Material Variability
One of the first challenges that lapidary artists encounter is the variability of the materials they work with. Each stone has its own unique characteristics, affecting how it can be manipulated. For example, softer stones like alabaster are easier to shape but can be prone to chipping, while harder stones like quartz or agate can be more resistant but require specialized techniques and equipment.
"The beauty of a stone may dazzle the eye, but its tendencies can surprise the unprepared."
This disparity can lead to unexpected results when attempting to achieve a desired cut or finish. Not only do you need to familiarize yourself with each type of stone's properties, but you also have to adjust your approach. Factors such as grain orientation, fractures, and inclusions can complicate the cutting process.
For those navigating this terrain, it’s advisable to have a range of tools at your disposal, accommodating the specificities of various stones. Understanding the following can be a game changer:
- Stone Hardness: Knowing the Mohs hardness scale helps you pick the right abrasives.
- Grain Patterns: Assessing how the stone is structured can lead to better finishing techniques.
- Fracture Handling: Techniques for cutting around fractures to maintain the integrity of the piece.
Equipment Limitations
Even the most skilled lapidary artist can run into challenges due to equipment limitations. While many devices may seem like they’re perfect for every task, the truth often is that they have their own constraints. For instance, a basic trim saw might not be able to handle thicker or denser materials effectively, leading to uneven cuts or excessive wear on the blade.
The type of lapidary machine chosen plays a significant role here. For example, older models may lack the precision required for intricate carvings, while budget machines may not have the durability necessary for extensive use.
Consider these points:
- Motor Power: Insufficient power can limit cutting speed and accuracy.
- Blade Quality: The quality of the blade determines not just the effectiveness of cutting but also the potential for finishing the stone accurately.
- Versatility: Some machines offer features that allow for more than one type of cutting or polishing, which can save time and money in the long run.
Future of Lapidary Technology
The realm of lapidary work has evolved remarkably over the decades, and as we gaze into the crystal ball of technological advancements, the future looks intriguing. The importance of discussing the future of lapidary technology lies in its potential to reshape how gemstone enthusiasts and collectors work with their tools, pushing the boundaries of creativity and efficiency. As innovation steers the industry, it becomes imperative to understand not just the tools but also how these advancements can enhance the craft, opening doors to unprecedented techniques and sustainability in our approaches.
Innovations in Machine Design
Let’s face it, lapidary cutting machines are not just machines. They are gateways to creativity, and with recent innovations, they are becoming smarter and more user-friendly. Manufacturers are increasingly integrating advanced technologies into their designs. One notable trend is the shift toward computerized systems with programmable settings. These systems allow lapidary artists to automate their processes, optimizing cuts with precision.
The development of better ergonomic designs has also been crucial. Machines are now built to minimize physical strain on the user. This is significant for long hours of work when fatigue can lead to mistakes. Lapidary artisans can now focus more on the art rather than the hassle of managing cumbersome equipment.
Furthermore, the incorporation of enhanced cooling mechanisms, such as mist cooling systems, is proving beneficial. This avoids overheating during cuts, prolonging the life of the blades and the integrity of the gemstones.
Here's what makes these innovations so compelling:
- Efficiency: Faster processing times without compromising quality.
- Quality Control: Enhanced precision means fewer mistakes, resulting in better finished products.
- User Experience: Simplifies complex tasks, making it accessible for beginners and advanced users alike.
Sustainable Practices in Lapidary Work
The growing concern for environmental sustainability has seeped into every field, and lapidary work is no exception. This topic is not just a buzzword; it's a call to action for collectors and artists alike. Sustainable practices in lapidary work mean not only being responsible about the materials sourced but also revolutionizing how the cutting and polishing processes are conducted.
One aspect of sustainability is the push toward using eco-friendly materials. This includes blades and abrasives that minimize harmful emissions and are easier to dispose of responsibly. Moreover, the use of water in lapidary processes has become a focal point. Adopting water-efficient techniques helps reduce waste and offers a cleaner working environment, which is essential for both artistry and health.
Recycling materials has also gained traction; many artists now repurpose offcuts and remnants into unique pieces of art or jewelry, managing waste more effectively. Such practices not only contribute to a greener planet but also spark creativity. For lapidary workers:
- Feedback Loops: Sourcing gemstones ethically encourages positive community relationships.
- Resource Conservation: Using less water and energy reduces costs and environmental impacts.
- Creative Reuse: Finding new life for waste materials can lead to innovative designs.
"Innovation and sustainability in lapidary work are intertwined, ensuring that the craft can thrive for generations to come."
By focusing on these aspects, future lapidary technology is poised to redefine our approach to cutting and processing stones. As we stand on the brink of these advancements, collectors and artists have the chance to shape a future that values efficiency without sacrificing creativity or sustainability.
Epilogue
As we wrap up our exploration of lapidary cutting machines, it’s clear that these tools hold tremendous significance for both hobbyists and professionals in the field of stone cutting. Understanding their functionality and nuances is not just about operating machinery; it means diving into a world where art meets science, creating exquisite pieces from raw materials. The information presented here not only clarifies technical aspects but also emphasizes key considerations when selecting and maintaining these machines.
Summarizing Key Points
- Diverse Machinery: Lapidary cutting machines come in various forms—from diamond blade saws to polishers—each serving a distinct purpose that caters to a range of applications in lapidary work.
- Maintenance is Critical: Regular upkeep of machines ensures longevity and performance, preventing costly replacements and ensuring safety during operation.
- Safety First: Prioritizing safety protocols and wearing appropriate protective gear cannot be stressed enough. The nature of the materials cut and the machinery operated warrants this caution.
- Innovative Techniques: The blend of traditional and modern techniques allows for greater creativity, enabling collectors to explore new artistic avenues in their stone work.
"In the world of lapidary, the right machine is a collector's best friend, and safety and maintenance are paramount."
The Importance of Lapidary Cutting Machines in Collecting
Lapidary cutting machines are more than just tools; they act as gateways for transforming nature's masterpieces into collectible works of art. For rock and fossil enthusiasts, these machines bring dreams to life. The ability to shape, grind, and polish stones holds intrinsic value, turning rough gems into showpieces for display. The machines allow individuals to express their creativity while honing skills that have been passed down through generations.
Considerations on the role of these machines also extend beyond the individual to the greater community of collectors. By mastering the use of lapidary tools, collectors not only enrich their own experience but also contribute to an appreciation of the artistry behind stones and fossils among a wider audience.