Understanding Hardness Testing: Methods and Insights
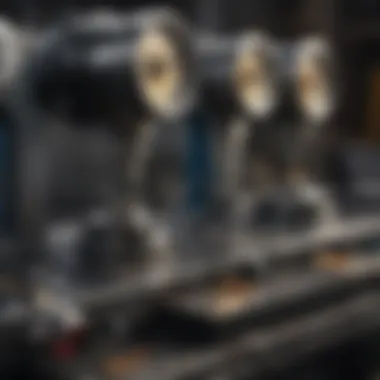
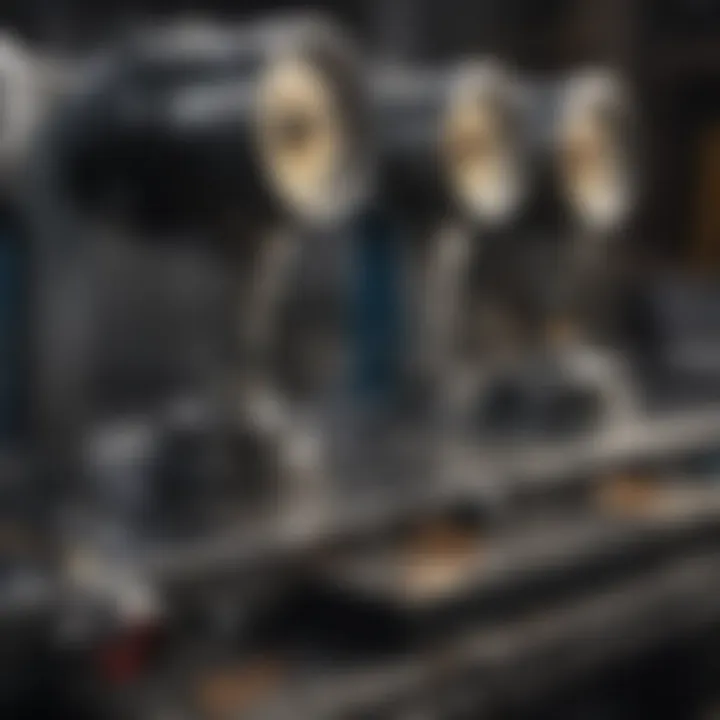
Intro
When it comes to materials science, understanding the properties of substances is crucial. One of the key aspects that experts assess is a material's hardness, which measures resistance to deformation and wear. This measure is significant not just in theory but has practical implications across various industries. From construction to manufacturing, knowing how a material will behave under stress informs decisions about usage and longevity.
Hardness testing is a task rooted in both history and necessity. Different methodologies have evolved over time, reflecting changes in technology and scientific understanding. In this guide, we aim to cut through the noise and present a comprehensive overview—providing insights into the techniques, principles, and real-world applications tied to hardness testing.
Featured Collectible of the Month
Overview
This month, we turn our focus to a fascinating mineral that has garnered attention among collectors and geologists alike: Corundum. Known primarily as the mineral that produces sapphires and rubies, corundum's hardness rating of 9 on the Mohs scale illustrates its durability and resilience.
Historical Significance
Corundum has been valued for centuries, not only for its beauty but also for its utilitarian properties. Historical texts mention its use in making abrasives. Ancient cultures recognized corundum’s potential, using it to craft tools that could cut and scratch softer materials. Thus, corundum stands as a testament to how historical practices in material science have shaped today's applications.
Identification Techniques
Identifying materials can be straightforward or quite complex, depending on the substance in question. Here are a few key techniques used in identifying hardness in minerals.
Visual Characteristics
Often, visual inspections can provide clues about a material's identity. For example:
- Color: While not always definitive, color can aid in distinguishing between different minerals.
- Luster: The way light interacts with a mineral’s surface can help narrow down the category it belongs to.
- Crystal Shape: The geologic conditions under which a mineral formed often lend unique shapes that can assist in identification.
Resources for Identification
A wealth of resources are available for those looking to identify minerals based on their hardness and other characteristics:
- Wikipedia's Mineralogy section: Wikipedia on Mineralogy
- Britannica's article on gemstones: Britannica on Gemstones
- Reddit communities: Engage with fellow collectors for firsthand experience and suggestions.
- Facebook groups: Join specialized groups dedicated to rock and mineral enthusiasts.
Prelude to Hardness Testing
Understanding hardness testing serves as a cornerstone in the field of material science. This section aims to prepare the reader for a deep dive into the various methods of determining material hardness. By shedding light on the definitions and purposes of hardness testing, we prepare the groundwork necessary to appreciate its importance in both the academic and industrial landscape.
Definition and Purpose
At its core, hardness testing measures a material's resistance to indentation, which in turn provides insights into its mechanical properties. Think of it as testing the durability of a pencil against paper: if the pencil is too soft, it will crumble, yet a harder pencil will create a distinct line without wearing down quickly. This analogy illustrates why hardness is not just a number; it’s an indicator of how a material will perform in real-world applications.
Hardness tests come in various forms, each designed with specific objectives in mind. For instance, the Rockwell hardness test quickly measures hardness under a defined load and a specific indenter shape. Another example is the Vickers hardness test, which can assess a variety of materials through a diamond pyramid indenter. Accurate hardness readings play a vital role in material selection, ensuring that the right material is chosen for demanding applications, whether it is in aerospace components or everyday tools.
In sum, the purpose of hardness testing extends beyond simple numbers. It provides a reliable assessment that informs engineers and sourcing specialists about material suitability. By understanding how well materials resist deformation, one can make educated decisions, minimizing the risk of failure in real-life scenarios.
Importance in Material Science
The significance of hardness testing in material science cannot be overstated. It acts as a vital gauge of a material's overall quality and performance potential. In industries such as aerospace or automotive, where safety is paramount, the hardness of materials impacts functionality and longevity. A component that is too soft may warp under stress, leading to catastrophic failure, while an overly rigid material could become brittle and shatter.
These testing methods also ensure consistency in production—factories rely on established hardness levels to maintain product quality. When a batch of materials consistently meets specific hardness criteria, manufacturers can confidently incorporate them into their products. This reliability extends to fields like geology, where collectors and researchers utilize hardness tests to classify minerals, aiding in both academic study and practical application.
Moreover, by understanding hardness in relation to other physical properties—such as tensile strength and wear resistance—scientists and engineers can design materials tailored to particular needs. For instance, in creating a new alloy for high-temperature environments, knowing the hardness behaviors allows for optimization in performance and durability.
"Hardness testing isn't just about knowing how hard a material is; it's an intricate step in the critical path of material selection and application in engineering processes."
Historical Background
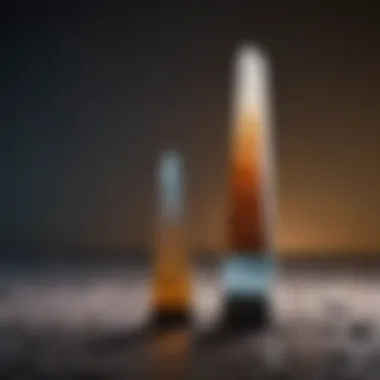
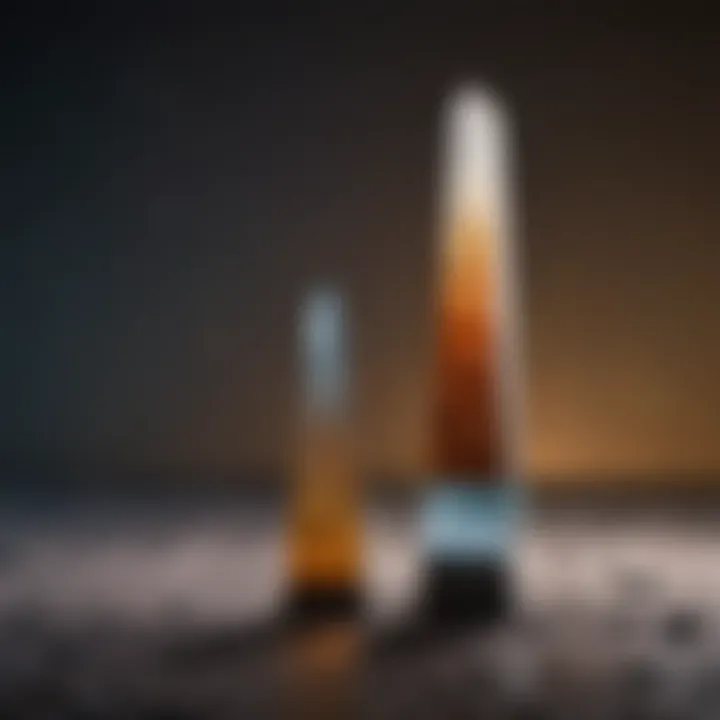
The historical background provides a crucial lens through which one can appreciate the evolution of hardness testing methods. Understanding this context not only sheds light on how far the science has come but also underscores the importance of these methods in contemporary material science applications. Historical awareness allows collectors and enthusiasts alike to grasp the foundational principles that guide modern testing techniques and, in turn, informs their understanding of how these practices affect both geological specimens and industrial applications.
Early Methods of Measurement
Back in the day, the quest to measure hardness wasn't all about fancy machines. Early methods relied mainly on simple tests and observations. For instance, one of the most primitive techniques used a scratch test, where harder materials would leave a mark on softer ones. Thomas Edison, for instance, favored this scratch method often to assess the durability of various materials he was working with.
Another method was the Mohs scale, developed by Friedrich Mohs in 1812. This scale, rating minerals from talc (1, the softest) to diamond (10, the hardest), utilized comparative scratching. It’s worth noting that many rock collectors still refer to the Mohs scale to determine a mineral's hardness. It laid the groundwork for more precise methodologies that would soon follow.
"The exploration of hardness measures is as old as human curiosity about materials and their nature. It’s remarkable how these ancient techniques still influence current practices."
The simplicity of these early methods has a certain charm. They remind us that behind every scientific advancement lies an instinct, a need to quantify what seems immeasurable.
Evolution of Hardness Testing Techniques
As the world moved from the Industrial Revolution into the 20th century, the need for more accurate and reproducible hardness testing became increasingly apparent. Engineers and scientists sought ways to quantify hardness with greater precision, reflecting the growing complexities of materials being used in construction and manufacturing.
This led to the introduction of mechanical testing machines. The Brinell hardness test, developed by Johan August Brinell in 1900, is a notable example. This test employed a hardened steel ball pressed into the material being tested, offering a value that closely represented its hardness. It paved the way for various methods developed later that made testing more efficient for different materials.
In the mid-20th century, the Rockwell hardness test emerged, providing far quicker results than earlier methods. It utilized a diamond cone, making it particularly effective for metals and other hard materials. Its development signified a shift towards more automated and consistent testing procedures, allowing industries to test materials on an unprecedented scale.
With the rise of computer technology and advanced materials science, newer techniques such as the Vickers and Knoop tests further enriched the discussion around hardness testing methods. These techniques enable precise measurements on micro-scale levels, essential for fields ranging from electronics to modern rock collections.
In sum, the evolution of hardness testing reflects a synthesis of scientific inquiry and technological advancements, influencing countless applications in science and industry today. The strides taken from rudimentary scratching tests to sophisticated techniques demonstrate a compelling journey marked by necessity and innovation. The historical background lays a solid foundation for understanding not just how materials are tested today, but also why those tests matter.
Key Hardness Testing Techniques
When it comes to assessing the quality and durability of materials, understanding the various hardness testing methods is crucial. Not only do they allow for a comprehensive comparison between substances, but they also reflect the material’s ability to withstand wear and tear. Specific elements like precision, ease of use, and applicability to different materials play a vital role in deciding which test to use. Whether you’re a rock collector or someone involved in material sciences, grasping the core techniques of hardness testing can significantly enhance your ability to make informed decisions.
Brinell Hardness Test
The Brinell hardness test is one of the older methods, developed in the early 1900s. This test involves pressing a hard steel or carbide ball, usually 10 mm in diameter, into the surface of the material being tested under a defined load. After removing the load, the diameter of the indentation left in the material is measured. The Brinell hardness number (BHN) is calculated using this diameter and the applied load, giving a measure of hardness.
This method is highly effective for materials with coarse or heterogeneous structures because larger indentations reduce the impact of sampling errors. However, it has limitations. For example, it may not be suitable for very hard or very small materials. The results can also vary significantly with differences in surface finish and test conditions, so always keep in mind the specific context of your material.
Rockwell Hardness Test
Another popular technique is the Rockwell hardness test, which provides a quick and reliable measure of hardness. Unlike the Brinell test, the Rockwell method uses different indenter types, either a steel ball or a diamond cone, depending on the hardness of the material being tested. The test is conducted by applying an initial minor load, followed by a major load, before returning to the minor load, allowing the measurement of depth of indentation.
The simplicity and efficiency of the Rockwell test make it a favorite in manufacturing and industrial applications. It produces immediate results and requires minimal preparation. However, the choice between various Rockwell scales can be confusing. Knowledge of which scale is appropriate for the material is essential to avoid inaccurate outcomes.
Vickers Hardness Test
The Vickers hardness test, developed in the 1920s, is another versatile testing technique. This method uses a diamond pyramid indenter and applies a specific load, much like the Brinell and Rockwell tests. However, the unique shape of the Vickers indenter enables it to provide values even for very hard or thin materials. The resulting indentation is measured typically using a microscope, allowing for greater precision in determining hardness levels.
One of the standout features of the Vickers test is its applicability across a wide range of materials, which makes it invaluable in research settings. Unlike Brinell, no limit is placed on the thickness of the material, and the test can be conducted on very thin sheets. However, this precision can come at the cost of longer testing time compared to Rockwell.
Knoop Hardness Test
Lastly, the Knoop hardness test is a method that shines when dealing with very brittle materials. This test uses an elongated diamond indenter, which creates a diamond-shaped indent in the material. The unique geometry allows for measurement along one dimension, making it an ideal choice for brittle materials or thin coatings.
The main advantage of the Knoop test is its ability to measure very small and delicate samples while leaving minimal damage to the material. It is particularly applicable in fields like semiconductor technology and coatings. The downside? The measurement process can be more intricate and may require specialized equipment.
"Though different techniques are used to determine hardness, each provides unique insights into the material's wear resistance, ultimately steering the choice of the right materials in various applications."
In summary, understanding these key hardness testing techniques forms the bedrock for effective material selection and evaluation. The comparative strengths and limitations of each method should not be overlooked, especially when it comes to delicate materials or specific industry requirements. Making informed choices lays the groundwork for optimal quality in production and research.
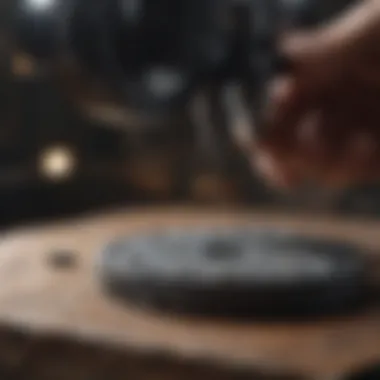
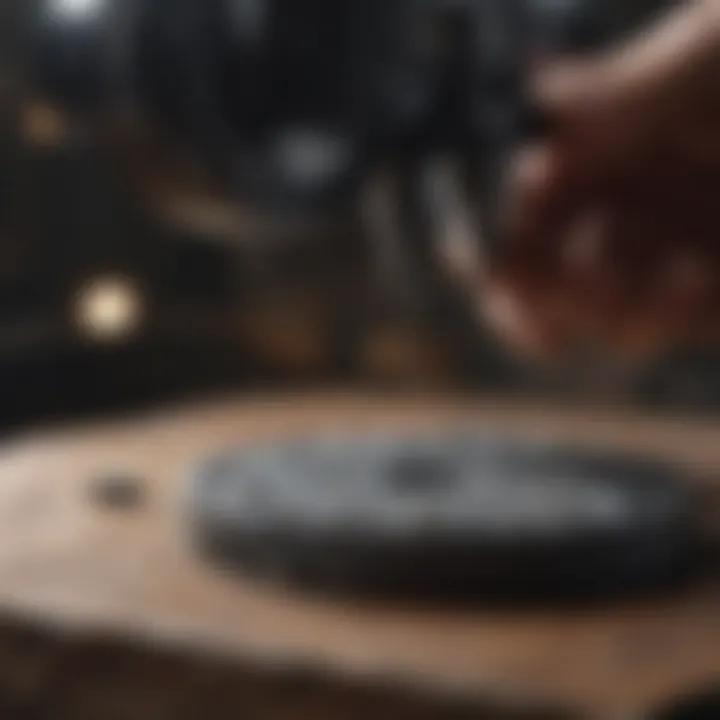
Comparison of Hardness Testing Methods
When it comes to assessing materials in the field of hardness testing, understanding the different methods available is vital. Each testing technique has its strengths and limitations, which directly influence the results and the applicability in various scenarios. By comparing these methods, professionals can make informed decisions that enhance the efficiency and effectiveness of their assessments. A thorough evaluation of these methods ensures that the right choice is made for specific materials, leading to better material selection and quality control in various industries.
Strengths and Limitations
In each hardness testing method, certain strengths stand out, but there are also limitations that must be understood. Here’s a closer look:
- Brinell Hardness Test
Strengths: - Rockwell Hardness Test
Strengths: - Vickers Hardness Test
Strengths: - Knoop Hardness Test
Strengths:
- Suitable for materials with a coarse or uneven structure.
- Provides an average hardness of the tested area, which is useful for heterogeneous materials.
Limitations: - Not ideal for very hard materials due to the test balls being prone to wear.
- Larger indentation may affect the aesthetics of smaller samples.
- Fast and straightforward, yielding quick results.
- Various scales available, making it versatile for multiple material types.
Limitations: - Can be affected by surface roughness, leading to inconsistent results.
- Less accurate for soft materials in comparison to harder types.
- Applicable to all types of materials, including thin sections.
- Provides continuous hardness values, allowing for detailed testing.
Limitations: - Can be time-consuming as it requires optical measurement of indentation.
- More sensitive to operator skill, which can lead to variability in results.
- Excellent for brittle materials and thin films.
- Produces minimal damage due to the small indentation size.
Limitations: - Like Vickers, it requires optical equipment for measurement.
- Can be less reliable if the material has a rough surface.
Understanding these strengths and weaknesses is crucial for anyone involved in material science, as it shapes the path toward selecting the most appropriate testing method for a job.
Choosing the Right Method for Specific Materials
Deciding on the right hardness testing method hinges on several factors related to the materials in question. Here are some considerations that can help guide the decision-making process:
- Material Type: Different materials either excel or struggle with various testing methods. For instance, metals with coarse grain structures often respond better to Brinell tests, whereas thin or brittle materials are more suited for Knoop hardness testing.
- Sample Size and Shape: The dimensions of the sample can restrict options. Vickers tests are particularly adaptable to small or irregular shapes, making them a good choice in such cases.
- Desired Accuracy: If precise measurements are necessary, Rockwell might not suffice, particularly for softer materials where more sensitive techniques like Vickers or Knoop come into play.
- Testing Environment: Conditions such as temperature and surface finish can affect outcomes. Hardness tests done in controlled environments yield more reliable data.
- Industry Standards: Some industries may have established standards that dictate specific testing methods. Adhering to these can ensure compliance and quality assurance.
Ultimately, selecting a hardness testing method is not just a matter of preference; it's a calculated choice contingent on the specific circumstances surrounding the material being tested. By keeping these factors in mind, professionals can navigate the complexities of hardness testing with confidence.
Applications of Hardness Testing
Hardness testing isn't just a lab exercise; it has real-world implications across various industries. Understanding the applications helps one grasp not just its significance, but also how it shapes material choices and quality benchmarks. Many professionals, especially in sectors like engineering, manufacturing, and mining, depend heavily on the results of hardness tests to guide their decisions. The reliable data these tests provide can save time and resources, reduce waste, and ensure that products meet stringent quality standards.
Material Selection in Industry
When it comes to choosing materials for a project, hardness testing plays a critical role. Materials with the appropriate hardness can lead to enhanced performance, longevity, and cost-effectiveness. For instance, in automotive manufacturing, the hardness of metals like aluminum and steel can determine a part's ability to withstand wear and tear.
- Applications:
- Importance:
- In selecting components for engines, gears, and other high-stress applications, hardness testing helps ensure the material can handle expected loads and conditions.
- Harder materials often offer better resistance to deformation, making them ideal for specific uses.
- Using the proper hardness criteria, engineers can prevent costly failures and product recalls.
- Materials that are too soft could fail prematurely, while excessively hard materials might be too brittle, leading to fractures over time.
Quality Control Measures
Hardness tests are integral to quality assurance processes. Consistent and accurate hardness measurements can act as a useful indicator of a material's overall quality. This is particularly crucial in production environments.
- Routine Testing:
- Cost-Effectiveness:
- Regular hardness tests on products during manufacturing can help detect variances before they escalate into larger quality issues.
- Certain hardness levels can serve as benchmarks, ensuring each batch meets specified standards.
- Implementing hardness testing as part of regular quality control can help companies save both time and money by avoiding faults in production.
- It also aids in sustaining the reputation for quality, a vital asset in competitive markets.
"Hardness measurement is fundamental to ensuring that the right materials endure in tough working environments and maintain their integrity over time."
Research and Development Implications
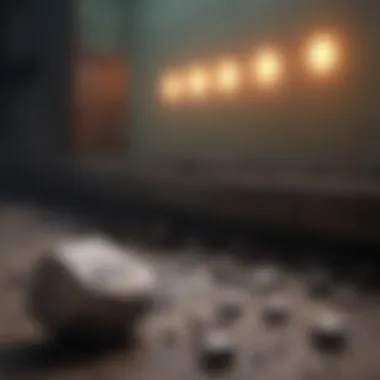
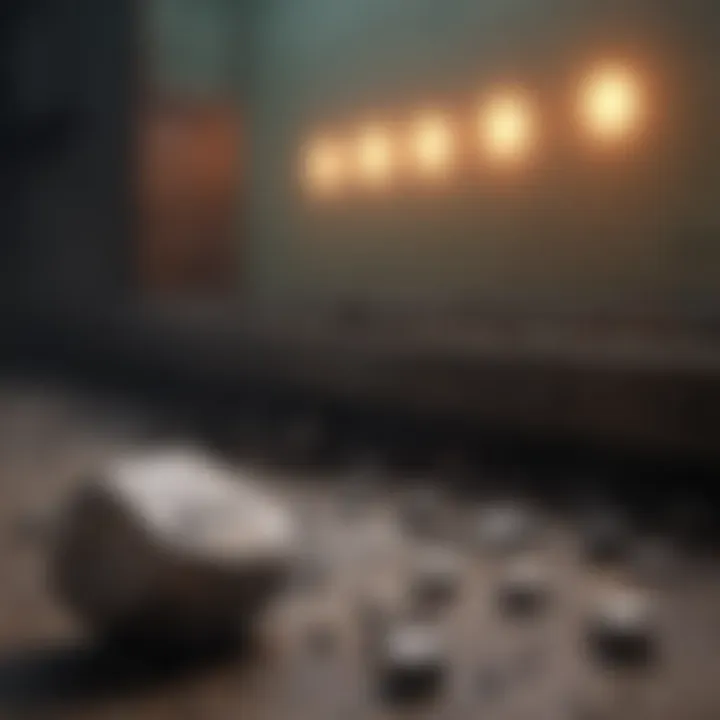
In the field of research and development, hardness testing has a multifaceted role. It’s not just about knowing how hard a material is; it's about pushing the boundaries of what materials can do. Innovations often arise from understanding how different compositions respond to hardness tests.
- Material Innovations:
- Testing New Hypotheses:
- By studying the hardness of new alloys or composites, researchers can identify potential applications that weren’t previously feasible.
- Insights from these tests can lead to the development of stronger, lighter materials that revolutionize industries from aerospace to construction.
- As new materials are synthesized, hardness tests provide crucial data to validate whether they meet the desired qualities.
- From creating cutting-edge ceramics to high-performance plastics, hardness data drives innovation and informs design choices.
Understanding these layers of application for hardness testing illuminates its pivotal role in ensuring that high standards are set and maintained in material performance across various domains.
By recognizing its relevance, professionals can tailor their approaches to leverage hardness testing for optimizing material selection, reinforcing product quality, and stimulating innovation.
Best Practices for Conducting Hardness Tests
In the realm of materials science, the reliability of hardness testing hinges greatly on adherence to established best practices. Such practices not only ensure the accuracy of results but also facilitate the repeatability of tests across different setups. Fostering a strong foundation in the essential methodologies can lead to highly consistent outcomes, ultimately impacting material choice in various applications. This section delves into two pivotal elements: sample preparation and equipment calibration.
Preparing Samples for Testing
The quality of test results can often be traced back to how well the samples were prepared. Ignoring this phase can lead to misleading data. Here are some crucial points to consider:
- Surface Condition: The surface must be smooth and free from contaminants. Any debris, oil, or rust can skew the results. A meticulous cleaning process is necessary; using solvents like acetone can yield a pristine surface.
- Uniformity: Ensure that the samples are of uniform thickness and composition, as variations can result in drastic differences in hardness readings. Performing a visual check can often help catch obvious inconsistencies.
- Geometry: Adhere to specific geometric standards suitable for each hardness test type. For instance, Brinell testing requires a specific diameter for testing balls to be effective.
- Size Limitations: Larger samples might not fit all testing machines, affecting how the test is conducted. Assess the capabilities of the testing equipment beforehand to choose the right sample size.
In summary, proper sample preparation is paramount to achieving reliable hardness measurements. Invest time in this step to establish a solid groundwork for testing.
Calibration and Maintenance of Equipment
The precision of any testing outcome is closely tied to the condition and calibration of the equipment used. A well-calibrated machine can mean the difference between a good and a borderline test result. Here’s what you need to consider:
- Regular Calibration: Calibration should be performed regularly, as recommended by the manufacturer. This ensures the equipment maintains its accuracy over time. Having a professional conduct this service can provide an added layer of trust in your results.
- Daily Checks: Before conducting tests, perform daily checks to ensure the equipment is functioning properly. A quick operational check can save time in the long run. Just running a few basic tests can indicate whether the machine is ready for action.
- Environmental Factors: Keep an eye on the environmental conditions where the tests will be held. Factors like temperature and humidity can affect the machine’s performance. A stable environment can enhance the consistency of your results.
- Documentation and Record Keeping: Maintain a log of all calibrations and maintenance performed on the equipment. This not only aids in quality control but also serves as a reference point for future calibrations.
Adhering to these steps will ensure that the hardness tests are not just routine processes but are robust indicators of a material's properties. Healthy equipment ensures accurate results, which makes any future material selection more educated and reliable.
Limitations of Hardness Testing
Hardness testing plays an essential role in evaluating materials, yet it's vital to recognize that this method comes with its limitations. Understanding these drawbacks is just as important as grasping the benefits of the tests themselves. These limitations can influence both the interpretation of results and the subsequent decision-making processes in fields like material selection and product development.
Nature of the Material Tested
The inherent properties of the material under examination can affect the accuracy and applicability of hardness tests. For instance, when testing heterogeneous materials, such as composites or certain types of rock formations, a single hardness value may not do justice to the diversity within the sample. Different minerals or inclusions within a rock can yield significantly different hardness readings, leading to potentially misleading conclusions.
Moreover, some materials possess anisotropic qualities, meaning their hardness may vary based on the direction of the applied load. In simpler terms, an object might be tougher in one orientation than in another. When relying solely on hardness testing, one might overlook critical aspects of a material's overall behavior in practical applications.
Thus, testers must take the nature of samples into account, recognizing these nuances. Failure to do so can lead to erroneous assessments, resulting in material choices that might not hold up under stress.
Influence of Surface Conditions
The condition of the surface of a material is another crucial factor that can skew hardness testing results. Surface treatments, coatings, or even pre-existing wear can significantly modify the hardness observed during testing. For example, a metal piece that's been subjected to hardening processes like quenching may appear much harder than it actually is, only because of the specific surface layer formed.
Roughness and cleanliness of the tested surface also play pivotal roles. An uneven or contaminated surface can lead to inconsistent contact between the indenter and the material, which can impact the measurement. Thus, it is essential to thoroughly prepare the surface prior to testing to ensure a reliable outcome.
"Knowing what you’re testing is just as important as knowing how you’re testing it."
Emerging Trends in Hardness Testing
As the landscape of materials science continually evolves, the realm of hardness testing is not left behind. Emerging trends in this field underscore the intersection of traditional methodologies with cutting-edge technology. This section delves into these developments, exploring how they can enhance the processes of hardness measurement and material evaluation.
Integration with Advanced Technologies
With the advent of sophisticated technologies, the integration into hardness testing is proving to be a game-changer. For instance, digital hardness testers now combine precision measurements with automation and data analysis capabilities. This leap towards digital means accuracy is significantly improved, reducing human error while streamlining the testing process.
Moreover, machine learning algorithms are beginning to play a pivotal role. These systems can analyze vast datasets to provide insights into material behavior under various conditions. By understanding patterns in hardness data, manufacturers can predict performance, leading to better material choices. For rock and fossil collectors, this evolution means more accurate assessments of specimens, aiding in everything from valuation to preservation strategies.
Additionally, portable hardness testers have made significant strides thanks to advancements in sensor technology. These devices, which can be taken on-site, allow for real-time testing of samples in their native environments. This is especially beneficial for collectors who wish to assess the hardness of their specimens without transporting them to a lab.