Comprehensive Guide to Drill Bits for Rock Exploration
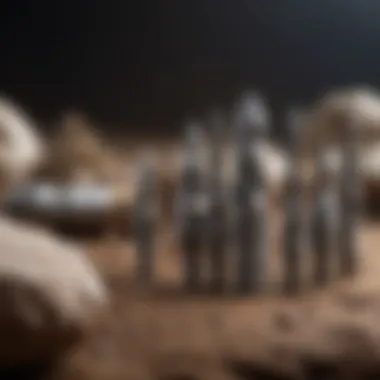
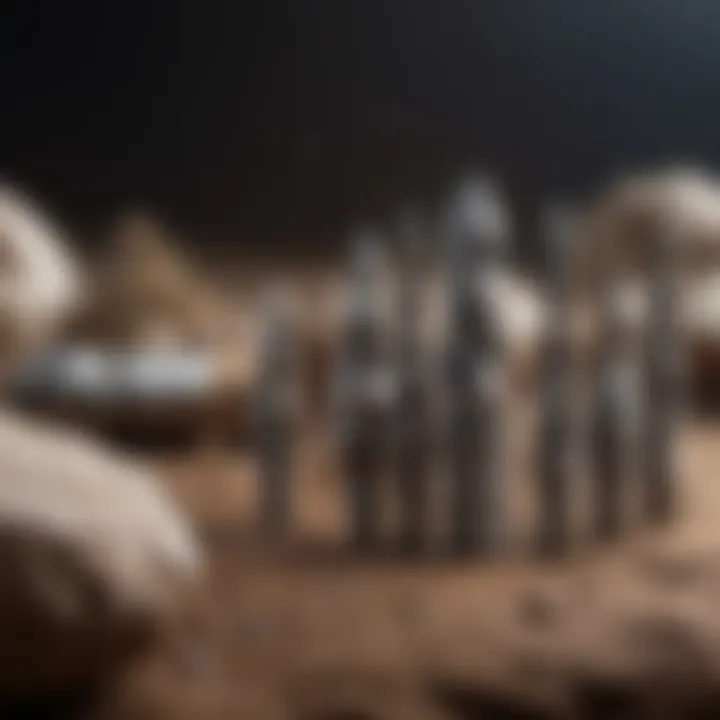
Intro
Drill bits serve as the unsung heroes of rock exploration, a field that has captivated both professionals and enthusiasts with its blend of science and artistry. These tools are not just simple attachments; they are the gateway to uncovering the geological wonders hidden beneath the surface. Understanding the various types of drill bits available, along with their specific uses and maintenance strategies, is essential for anyone looking to navigate the complexities of this adventure.
In this comprehensive guide, we aim to dissect the components and characteristics of drill bits designed for rock drilling. You'll learn about the different drilling environments one might encounter, and how that influences the choice of bit. We’ll also delve into material innovation and look at how advancements in technology have refined drill bit efficiency and durability. A well-informed approach to selecting and caring for your drill bits can not only save time and money, but it can also lead to more successful exploration results.
Whether you're a collector, a hobbyist, or a seasoned pro in the industry, this guide promises to enrich your understanding and appreciation of drill bits. Here, we hope to blend practical information with insightful analysis, creating a resource that resonates with the discerning audience bent on diving deeper into rock exploration.
Understanding Drill Bits for Rock
In the world of rock exploration, understanding drill bits is not just a technical necessity; it's the backbone of success in geological and mining projects. Each drill bit is meticulously designed for unique functions, ensuring that the process of penetrating tough geological layers is efficient and effective. Having a grasp on this subject provides several advantages, not only in operational skill but also in optimizing costs and enhancing safety.
Drill bits serve as tools of exploration, each tailored for the specific types of earth materials they will encounter. For enthusiasts and professionals alike, knowing how to select the right bit can make a significant difference in the efficacy of rock drilling activities. The financial investment in quality drill bits can often be offset by the reduced time and increased precision in the drilling process, making this knowledge crucial.
Definition and Purpose
At its core, a drill bit is a cutting tool used to create circular holes in hard materials, especially rock. They come in myriad types and sizes, each serving distinct purposes based on the geological makeup being drilled. Twist drill bits typically bore through softer rock, while specialized options like diamond bits excel in tougher settings.
The primary purpose of drill bits is not only to penetrate the earth’s surface but also to gather samples in a manner that reduces contamination. In geological exploration, these samples are invaluable, providing insights into mineral compositions, soil characteristics, and the overall viability of the drilling location.
History of Drill Bits
The history of drill bits dates back to ancient civilizations, where the need to excavate minerals and create shelter drove the innovation of simple hand tools. Early tools resembled modern-day augers, made from hard materials to scrape through softer earth layers. As technology progressed through the ages, so did the complexity of these tools.
In the late 19th century, advancements like the rotary drill were introduced, allowing for deeper penetration of rock. This marked a milestone in drilling operations, particularly in mining. Notably, the introduction of tungsten carbide in the mid-20th century revolutionized the field, enabling drill bits to withstand extreme conditions and maintain their cutting edge longer.
Each phase of history reflects an ongoing journey of improvement and adaptation in the design of drill bits. What once was a rudimentary procedure has transformed into a sophisticated science, driven by the rigors of exploration and the necessity for efficiency in resource extraction.
"The evolution of drill bits mirrors humanity's quest for knowledge beneath the Earth's crust, shaping how we interact with the raw materials that fuel our modern world."
By understanding these historical contexts, we pave the way for appreciating the latest advancements in drill bit technology, seamlessly blending past ingenuity with future possibilities.
Types of Drill Bits Used in Rock Drilling
When it comes to rock drilling, selecting the right drill bit is of utmost importance. The type of drill bit you use can significantly affect not only the efficiency but also the effectiveness of the drilling operation. Each type serves a unique purpose and is engineered for specific functions, whether that's the nature of the rock, the environment in which you're drilling, or the desired outcome.
Understanding the various types of drill bits enables drillers to tailor their equipment selection based on these factors, optimizing performance and prolonging the life of the bit. Let's delve into the different types of drill bits used in rock drilling, highlighting their specific characteristics and advantages.
Twist Drill Bits
Twist drill bits are often the most recognizable type, commonly seen in workshops and used in various applications. Their design features a helical groove that helps lift debris from the hole while simultaneously providing a cutting edge. Though they're typically used in softer materials like wood or metal, they can also be used in softer rock formations with moderate success.
These bits are effective for drilling small to medium holes but may struggle with harder rocks. Their versatility, however, makes them prevalent in various drilling scenarios where precision is essential, even if the material isn't particularly hard.
Button Bits
Button bits are crafted for tougher challenges. With their spherical tungsten carbide buttons, these bits are specifically designed to penetrate hard rock effectively. Button bits excel in applications like mining and geological exploration, where robust performance is crucial.
One major advantage of button bits is their durability: they reduce wear and tear significantly. Drilling on rocky surfaces can wear down standard bits quickly. However, with button bits, you often get a better cost-per-meter drilled, making them a sensible choice for long-term investments in drilling equipment.
Core Bits
Core bits are specialized tools used mainly for obtaining rock samples, which is vital in geological exploration. Unlike other bits, core bits have a hollow center that allows them to extract a cylindrical sample of the rock as they drill. This is particularly useful for assessing mineral resources and the geological makeup of a site.
Due to their design, core bits can be more expensive than standard drill bits, but the quality of the sample retrieved makes them invaluable for researchers and professionals alike. While they may not be piecing together a whole puzzle on their own, they certainly provide essential clues about the bigger picture.
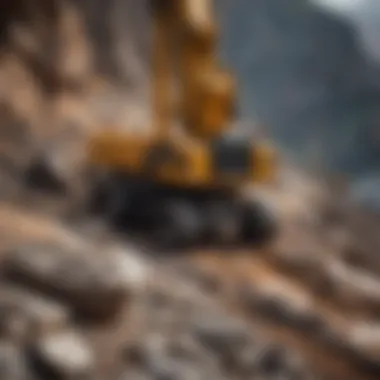
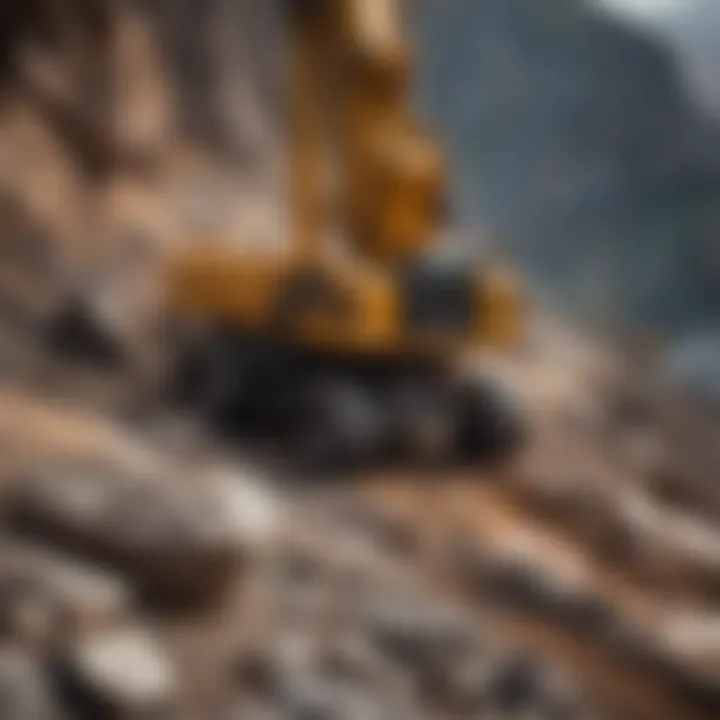
PDC Bits
Polycrystalline Diamond Compact (PDC) bits are crafted with synthetic diamond particles, allowing them to cut through tough rock efficiently. Their design is especially effective for drilling in shale or limestone formations. The unique geometry of PDC bits enhances their ability to maintain consistent drilling rates, reducing downtime and maximizing productivity.
These bits shine in applications where durability and penetration speed are paramount. Though they carry a higher initial cost, the longevity and performance of PDC bits can lead to lower overall drilling costs, turning the initial investment into a smart choice for serious drillers.
Diamond Bits
As their name implies, diamond bits contain real diamonds that help them effectively pulverize extremely hard rock. These bits are essential in situations where other drill bits would falter. They are widely used in mining operations and high-precision tasks that require unmatched cutting prowess.
Nevertheless, diamond bits come with a higher price tag, often making them the tool of last resort when all else fails. The high cost is countered by their performance, allowing projects requiring precision drilling in hard rock to progress more swiftly and efficiently.
The choice of drill bit can determine the success and cost-efficiency of any drilling operation. Understanding the different types is critical to making informed decisions that can save time and resources.
In summary, various drill bits have their niches and specific applications in the realm of rock drilling. By understanding these differences, you can choose the best equipment for your next drilling project.
Selecting the Right Drill Bit
Selecting the appropriate drill bit is crucial when embarking on rock exploration. Each type of drill bit has its own unique attributes, designed to tackle specific challenges associated with various rock formations. This selection process not only influences the efficiency and speed of drilling but also has substantial implications for both cost-effectiveness and the quality of samples obtained. By understanding how to choose the right drill bit, practitioners can avoid common pitfalls that hinder their work and ensure that they are equipped to meet the demands of their specific project.
Assessing Rock Type
Before anything else, evaluating the type of rock is a fundamental step in the selection process. Different rocks possess varying hardness levels, abrasiveness, and structural properties. For instance, while softer sedimentary rocks like limestone might allow for easier drilling with twist drill bits, harder igneous formations such as granite require specialized core bits or diamond bits for effective penetration.
- Hardness Classes: Rocks can be assessed based on the Mohs hardness scale. A granite will rank around 6-7, while softer rocks may score between 3-4. Understanding this ranking informs the selection of a suitable drill bit.
- Abrasive Characteristics: Some rocks contain minerals that can severely impede drill bit performance, such as silica in sandstone. A not-so-harsh rock type will not require the same robust gear as something highly abrasive.
It’s important to pay close attention to the specific characteristics of the rock layer you are tackling. Knowing if you have to contend with fractured granite or a stable limestone bed can make a world of difference.
Drilling Conditions Considerations
The drilling environment is another critical factor when selecting drill bits. Diverse conditions, including temperature, moisture, and the presence of water or gas, can influence how well a drill bit functions. In cases where moisture is prevalent, employing a bit with enhanced cooling features may improve performance.
Consider the following points:
- Alignment and Tolerance: Misalignment and poor tolerance can lead to excessive wear on a drill bit. Ensuring that the chosen bit aligns properly with the drilling equipment is key.
- Temperature Effects: High temperatures can affect bit integrity, particularly in harder rock types. Utilizing diamond bits may be beneficial in such conditions as they can withstand elevated temperatures better than some other bits.
Paying attention to the specific conditions can prevent you from facing unexpected struggles during the drilling process.
Bit Thickness and Size
Bit thickness and size play a vital role in selecting the right drill bit. Larger bits typically remove more material in a single pass, which can be advantageous for initial penetration. However, they may also demand more torque and can lead to quicker wear on the drill head. On the other hand, thinner bits may provide more precise control and less resistance but often require more time to achieve the same depth.
- Choosing Diameter: The diameter of the drill bit should correspond to the desired hole size and depth of the exploration task. For example, a larger diameter is often essential in mining operations when retrieving larger samples, while smaller diameters may suffice in geological surveys.
- Length Considerations: The depth of the drill also matters. A longer bit can reach deeper layers but can make it more susceptible to breakage or bending in harder rock layers without adequate support.
Selecting a drill bit that suits both the task and the specific parameters of the operation can go a long way in improving overall drilling effectiveness and efficiency.
Important Note: Never underestimate the consequences of a poor choice in drill bit selection; it could lead to excessive costs and potential project delays.
By taking into account rock types, drilling conditions, and specific dimensions, one can make a more informed decision that not only enhances performance but also ensures that rock exploration efforts yield valuable insights.
Technological Advancements in Drill Bit Design
In the realm of rock exploration, the technological advancements in drill bit design mark a significant leap forward in terms of efficiency, safety, and overall performance. As the industry grapples with tougher rock formations and the increasing demand for precision in drilling, these advancements become not just beneficial but imperative. New materials, improved geometries, and innovative performance enhancements are at the forefront of this evolution, ensuring that drill bits can withstand harsher environments while maximizing productivity.
Material Innovations
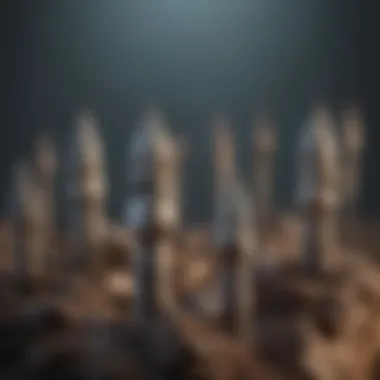
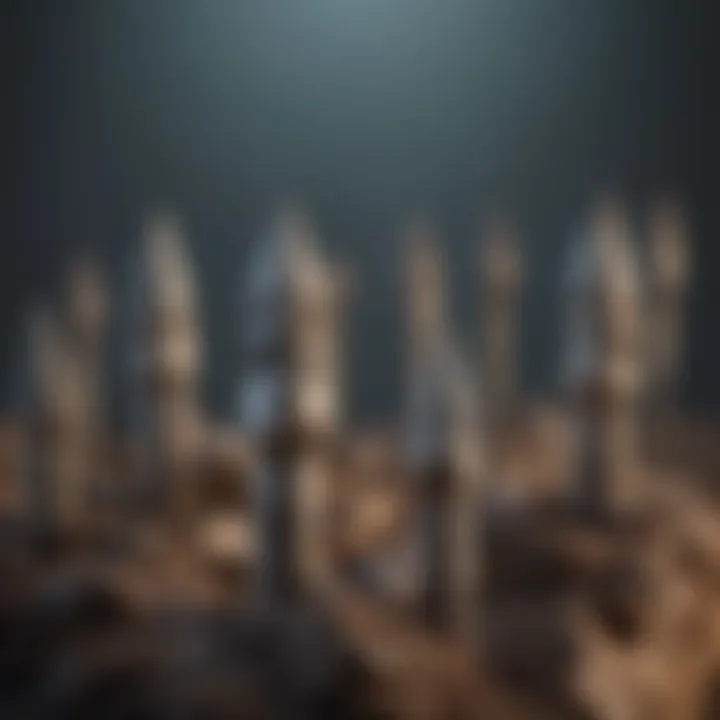
The backbone of any drill bit's performance lies within its material composition. Recent innovations have seen the use of advanced materials, such as tungsten carbide and ceramic composites, transforming traditional construction methods. These materials offer an edge in wear resistance, thus prolonging the lifespan of the drill bits. However, it’s not just about thickness or density; the micro-structural makeup of these materials allows for better heat dissipation and durability when drilling through various rock types.
Additionally, coatings like titanium nitride or diamond-like carbon have emerged, providing extra protection against abrasion and heat. These coatings lead to a significant reduction in friction between bit and rock, allowing for smoother operations. Adopting such materials means reduced downtime for replacing worn bits, ultimately leading to significant cost savings and better project timelines.
Geometric Design Improvements
Another substantial area of evolution is geometric design, which plays an essential role in determining how well a drill bit can penetrate rock. Modern bit designs incorporate features such as variable pitch spiral configurations, which help minimize vibration while drilling. With a well-calibrated design, the load distribution across the bit is optimized, allowing for better energy transfer from the drill to the rock, ensuring effective drilling.
Beyond just shapes, advancements in computer-aided design (CAD) allow for intricate patterns and designs that cater specifically to the type of rock being drilled. For instance, a bit designed for limestone will have different geometrical properties than one intended for granite. This tailored approach can lead to significantly improved penetration rates and reduced energy consumption during drilling tasks.
Performance Enhancements
The last pillar of technological advancement is directly related to performance enhancements. The integration of sensors and IoT technology into drill bits represents a shift towards smarter drilling. These sensors can monitor temperature, vibrations, and even the rate of penetration in real time, providing data that can guide adjustments during the drilling process. With this insight, drill operators can instantly adapt their techniques to minimize wear and maximize output.
Moreover, advances in fluid dynamics have led to improved designs optimizing how drilling fluids are used. When properly designed, drill bits can better channel these fluids, which are vital for cooling the bit and removing debris from the drill hole. This can result in cleaner and faster drilling operations, which is particularly important in geological exploration where precision is key.
"The advancements in drill bit technology are akin to upgrading from a horse-drawn carriage to a high-speed train. Efficiency and effectiveness scale new heights, making exploration tasks quicker and more reliable.”
Maintenance of Drill Bits
Maintaining drill bits is essential for ensuring their optimal performance and longevity. Neglecting maintenance can lead to decreased efficiency, increased costs, and the need for premature replacements. For rock drilling, this is especially critical, as the wear and tear on bits can directly affect drilling accuracy and time. A well-maintained bit can save significant resources and frustrations down the line.
Cleaning Procedures
To guard against buildup that can hinder performance, it's vital to establish a regular cleaning routine. After each use, drill bits should be thoroughly cleaned using a soft brush to remove any debris, dirt, or rock particles. Depending on the bit type, soaking in a mild detergent solution can help soften more stubborn residues. This not only helps in maintaining their effectiveness but also minimizes the risk of corrosion or further damage.
- Tip: Always ensure that bits are completely dry before storing to avoid oxidation.
Storage Recommendations
Storing drill bits might seem straightforward, but there are important considerations to keep in mind. Upon returning from a drill site, bits should be stored in a dry, cool place to avoid moisture buildup that can lead to rust. A dedicated toolbox or container with foam padding can protect the bits from physical damage during transit. Keeping bits organized not only facilitates easy access but also ensures that you can quickly find the right tool for the job.
- Pro Tip: Labeling containers with the type and size of drill bits can make a significant difference in efficiency.
Inspection for Wear and Damage
Regular inspections are crucial in identifying signs of wear and damage that can compromise a drill bit's performance. It's advisable to inspect bits before and after use. Look for any signs of chipping, dullness, or unusual wear patterns. If a bit shows significant wear or is not functioning correctly, it should be replaced. Neglecting this can lead to less effective drilling and potentially damage the rock being drilled.
Remember: "A stitch in time saves nine." Taking just a few moments to check and maintain bits can save a fella from headaches and costly downtime.
Whether you’re working on geological exploration or construction projects, keeping your drill bits in great shape will not only enhance their performance but will also save you time and money in the long run.
Applications of Drill Bits in Rock Drilling
Drill bits are the unsung heroes in various fields, pivotal to both practical applications and explorative endeavors within rock drilling. Their significance cannot be overstated, as they directly impact the efficiency and success of drilling projects. Understanding these applications is key for professionals and enthusiasts aiming to leverage the most suited tools for their specific needs.
Construction and Engineering
Construction and engineering projects rely heavily on reliable drilling methods to ensure solid foundations and underground structures. For instance, drilling is crucial for creating deep holes for piles in bridge construction or securing stable support in tunnel excavations.
- Precision and Depth: Specialized drill bits, such as core bits, allow engineers to obtain samples of subsurface materials. This is particularly valuable for assessing soil conditions and rock quality, which shape overall project risk and feasibility.
- Adaptability: Projects vary in requirements; in some situations, rapid drilling is necessary, demanding bits that can cut through dense rock without frequently needing replacement. For instance, button bits made of tungsten carbide provide durability and efficiency in hard rock layers.
Every drill bit used serves a purpose, informed by the geological conditions and the desired engineering outcome.
Mining Operations
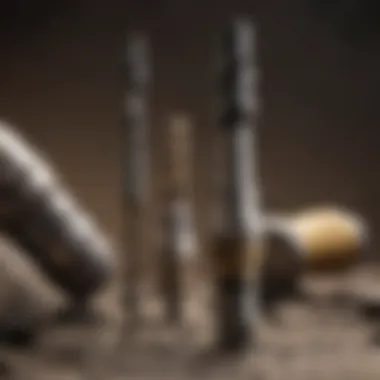
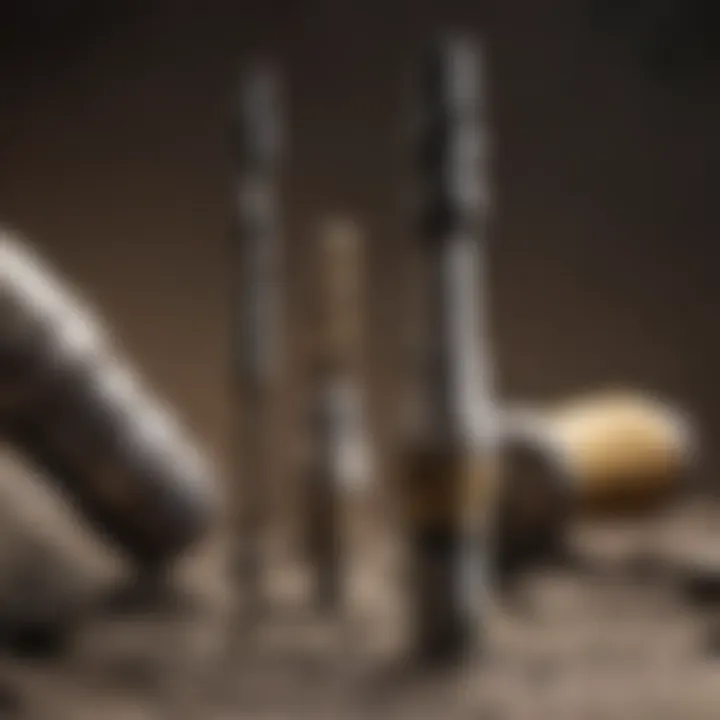
Drill bits are the backbone of mining operations, fundamentally determining how effectively resources such as minerals and ores can be extracted. The choice of the right bit can lead to significant economic benefits or costly inefficiencies.
- Types of Resources: Differentiating between mining applications is crucial. For instance, diamond bits are often preferred when exploring for precious minerals like diamonds or gold, while PDC bits are utilized in searching for natural gas or petroleum.
- Directional Drilling: Modern mining operations frequently require precise drilling to minimize environmental impact and optimize resource recovery. Mined lands are often re-engineered afterward, so thoughtful planning and execution greatly enhance future usability.
In this context, understanding how the characteristics of bits such as size and shape affect drilling efficiency can lead to improved operational strategies.
Geological Exploration
Geological exploration uses drilling to gather critical data about subsurface formations. This application is essential for resource development, environmental studies, and understanding geological history.
- Data Collection: Core bits, for example, help geologists obtain cylindrical samples of rock layers, revealing information about their composition, age, and structure. The insights gained can lead to the discovery of potentially lucrative resource deposits or identify hazardous geological conditions.
- Environmental Monitoring: Advances in drill technology also allow for more environmentally conscious practices. Minimizing waste while maximizing informational yield is now more achievable with specialized bits designed for precision and reduced impact.
In the world of geology and exploration, the drill bit is not merely a tool; it is a vital device that unlocks the mysteries beneath the earth's surface.
Safety Considerations When Using Drill Bits
When delving into rock exploration with drill bits, safety should never take a back seat. The importance of adopting the right safety protocols cannot be overstated. The work environment can be precarious, and preventing injuries is imperative not just for the individual, but for the entire team involved in the drilling operation. By being mindful of safety considerations, one can ensure that the equipment is used efficiently and risks are minimized.
Personal Protective Equipment
Wearing appropriate personal protective equipment (PPE) is fundamental when operating drill bits, as it serves as the first line of defense against potential hazards. Depending on the specific environment, PPE should typically include:
- Safety goggles: To protect the eyes from flying debris and dust. Without proper eye protection, even a small particle can cause significant harm.
- Ear protection: Drill operations can get noisy. Using earplugs or earmuffs can prevent long-term hearing damage caused by excessive noise levels.
- Respirators or masks: In some cases, airborne particles can harm respiratory health. Choosing the right mask helps filter out harmful dust.
- Steel-toed boots: These shoes protect against heavy equipment dropping on feet, which is a common risk on worksites.
- Gloves: Protecting hands is necessary to avoid cuts and abrasions when handling tools or materials.
By ensuring each team member is equipped with the right gear, risks associated with drilling operations can be significantly reduced.
Proper Operating Techniques
Proper operating techniques go hand-in-hand with safety. Knowing how to use drill bits effectively not only improves the efficiency of drilling but also minimizes the chances of accidents. Key techniques include:
- Maintain a firm grip: Always hold drill equipment firmly. A loose grip can lead to slips and unintended movements, causing injury.
- Check the equipment: Before beginning any drilling task, inspect the drill bit and machine for signs of damage or wear. Faulty equipment can result in malfunctions that might cause accidents.
- Use the right bit for the job: Choosing the appropriate drill bit that matches the rock type is crucial. Using the wrong bit can lead to breakage, which could be dangerous.
- Follow operational directions: Each drilling equipment comes with its own set of guidelines. It's vital to adhere to those instructions to ensure safety and effectiveness.
These practices ensure that operations run smoothly, thereby reducing the likelihood of incidents.
Emergency Procedures
In the event of an emergency, knowing the right procedures can be a lifesaver. Preparedness is key; here is what every team involved in drilling should have in place:
- First-aid kits: Ensure that a fully stocked first-aid kit is readily accessible on-site. It should contain various items such as bandages, antiseptics, and pain relievers.
- Emergency contact list: Keep contact information for local medical facilities and emergency services visibly posted. Quick action can make a world of difference when time is critical.
- Evacuation plan: Have a clear evacuation path in case of emergencies, especially if working underground or in isolated areas. Periodic drills can ensure everyone knows the procedure, reducing panic during actual emergencies.
- Fire safety equipment: Depending on the materials being drilled, flammable debris could pose a risk. Ensure that fire extinguishers are nearby and that staff are trained in their use.
"An ounce of prevention is worth a pound of cure." Each precaution taken reinforces a safety culture within the team that prioritizes health and well-being.
Future Trends in Drill Bit Technology
The realm of drilling technology is consistently evolving, mirroring advancements in related fields and adapting to the needs of the modern world. As challenges in rock exploration become more complex, the development of future trends in drill bit technology plays a pivotal role in ensuring efficiency, cost-effectiveness, and sustainability. This section highlights critical future developments to watch out for in drilling technology, mainly focusing on sustainability and automation.
Sustainability in Manufacturing
Sustainability in drill bit manufacturing is no longer a mere buzzword; it's a critical element that affects resource management and environmental stewardship. Traditional drilling methods often rely on materials and processes that can be detrimental to the environment. New manufacturing techniques aim to remedy this.
- Use of Recycled Materials: Manufacturers are increasingly utilizing recycled metals and composites, reducing the need for virgin resources. This practice not only cuts costs but also decreases the carbon footprint of drill production.
- Eco-friendly Coatings: Innovative coatings are being developed that enhance performance while being far less toxic than traditional options. These coatings can improve a bit's durability, ultimately leading to less waste and fewer replacements.
- Energy-efficient Production Processes: New technologies in production workflows help reduce energy consumption. Using renewable energy sources in manufacturing processes represents a critical step toward sustainable practices.
The shift toward sustainability in this industry isn't just a trend; it is a response to demands from stakeholders who prioritize environmental responsibility. This approach can also yield considerable financial savings in the long run, making it an attractive option for companies looking to balance profit with principle.
Automation and Robotics in Drilling
Automation and robotics are set to revolutionize not just drilling practices, but also the entire exploration landscape. By integrating advanced technologies into drilling operations, companies can significantly enhance productivity and safety. Here’s how:
- Precision and Consistency: Automated drill rigs equipped with advanced sensors can achieve greater accuracy. This precision means fewer errors and less wasted materials during exploration projects.
- Remote Operations: With the rise of robotics, operators can now control drills from afar, reducing the need for on-site personnel. This not only improves safety by minimizing human exposure to hazardous conditions but also cuts labor costs.
- Data Collection and Analysis: Automated systems can collect vast amounts of data in real-time, providing insights into performance and geological conditions. This information is invaluable for making informed decisions regarding drilling strategies and selecting appropriate drill bits for differing rock types.
Incorporating robotics into drilling operations not only paves the way for efficiency but could also lead to breakthroughs in discovering resources previously considered unreachable.