Mastering Stone Work with the Dremel Tool
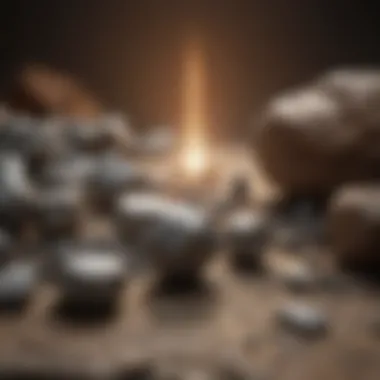
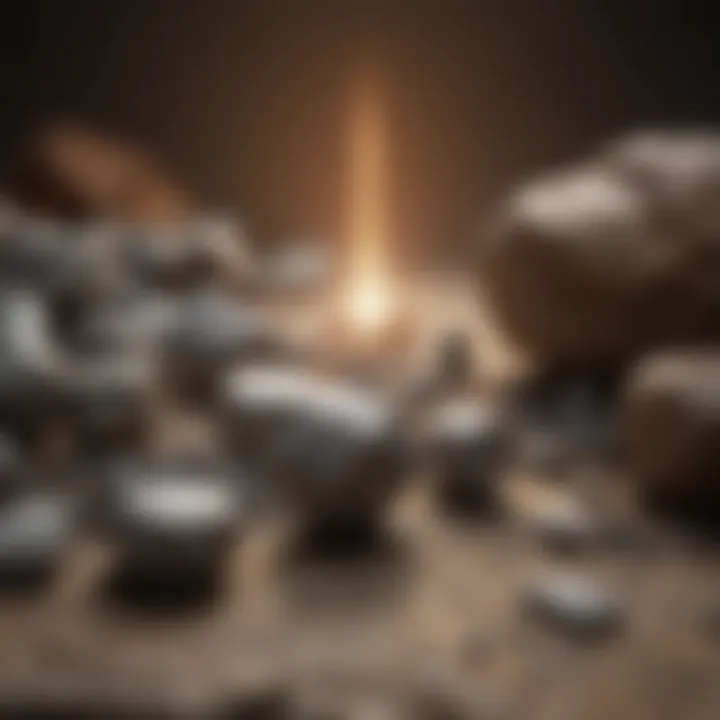
Intro
The world of stone crafting is a fascinating realm where artistry meets practicality. For those who dive into this craft, having the right tools makes all the difference. Among these tools, the Dremel holds a special place. Known for its versatility and precision, it transforms ordinary blocks of stone into masterpieces, whether for sculptures, inlays, or other decorative projects.
In this article, we will unravel the intricacies of the Dremel tool as applied to stone work. We will touch upon its various functionalities, delve into the types of bits one might need, and explore techniques that can elevate a crafter’s work to professional levels. Safety also plays a significant role in crafting, and we’ll address those essential precautions. By the end of this guide, both beginners and seasoned pros should feel equipped to take on their next stone project with confidence.
Before we dig deeper into specifics, let’s first highlight what makes the Dremel tool a staple in the toolkit of stone artisans.
Foreword to Dremel Tools
When it comes to stone work, having the right tools can mean the difference between a project that turns out well and one that goes sideways. Dremel tools have become synonymous with versatility and precision in crafting, particularly when it’s about shaping and finishing stone. This section delves into what makes Dremel tools particularly valuable, covering their adaptability, ease of use, and some critical considerations to keep in mind.
Brief History and Evolution
Dremel’s roots trace back to 1932, when it was founded by a watchmaker named Albert Dremel. The original idea was to create a tool that could perform intricate tasks. Over the years, from a modest rotary tool, Dremel has evolved. It now offers a range of models capable of handling various materials including metals, wood, and, of course, stones.
As technology progressed, so did the capabilities of the tools. For instance, the introduction of more powerful motors and a wider array of compatible bits transformed how enthusiasts and professionals engage with stone. Today’s Dremels are equipped with varying speed settings, allowing for fine adjustments based on the material and the desired finish. This evolution has kept Dremel at the forefront of crafting tools, among both casual users and serious stone workers alike.
Why Use a Dremel for Stone Work
Using a Dremel for stone work offers several benefits that make it an appealing choice:
- Versatility: Dremels can handle a range of tasks, from cutting and engraving to polishing stones. This gives users the flexibility to approach a project in multiple ways without needing to switch tools constantly.
- Precision: The tool's design allows for fine control, which is crucial when dealing with stone - especially softer varieties like soapstone or more intricate projects like gemstone engraving. This enables artisans to achieve a level of detail that larger tools often cannot match.
- Compactness: Unlike larger stone working tools, Dremels are lightweight and easy to handle. This portability is helpful for gathering inspiration from nature by working outdoors or shifting from one task to another without hassle.
- Ease of Use: For those just starting in stone work, Dremels offer user-friendly functions. Many of them come with instructions that guide you step by step, making it simpler to learn the ropes without feeling overwhelmed.
"A Dremel in skilled hands can turn rough edges into masterpieces of stone art."
In essence, Dremel tools not only simplify the crafting process but also enhance creativity, allowing for more intricate designs and applications in stone work. Understanding their history and advantages sets the stage for knowing how to leverage them effectively in your projects.
Understanding Dremel Tool Specifications
Understanding the specifications of Dremel tools is crucial when engaging in stone work. The performance and capabilities of these tools can significantly influence the quality of your projects, whether you're shaping a delicate gemstone or tackling a more robust piece of stone. Knowing your Dremel's specifications not only empowers you to use the tool effectively but also ensures that you choose the right model for your needs. With so many options out there, diving into the details can make all the difference.
Motor Power and Speed Settings
The motor power of a Dremel tool is often one of the first specifications to consider. This is measured in watts, and a higher wattage usually equates to more power for cutting through harder materials. For those who frequently work with tough stones like granite or quartz, a Dremel with at least 150 watts is advisable. On the flip side, softer stones and detailed engraving tasks may not require as much muscle.
Speed settings are equally important. Dremel tools generally come with adjustable speed dials, allowing users to tailor the RPM to their specific tasks. For example, a slower setting around 10,000 RPM might be ideal for precision engraving, while a higher speed upwards of 35,000 RPM could work for flattening or shaping stones. Having that versatility ensures you won’t be caught flat-footed when tackling different materials and intricacies.
"The right RPM can make or break your project, ensure you know your tool's speed capabilities."
Corded vs. Cordless Models
When deciding between corded and cordless Dremel models, consider the specific requirements of your stone working projects. Corded Dremels generally lend themselves to more prolonged use without the worry of battery life. These models often deliver consistent power, which is pivotal when working on tough stone. They’re particularly useful for larger projects that require extensive periods of detailed work, as you won't find yourself scrambling for an outlet halfway through.
On the other hand, cordless Dremels offer unmatched portability. If freedom of movement on-site or in varied locations is an essential factor for you, then a battery-operated model might be your best bet. Keep in mind, however, that the battery's lifespan can become a limiting factor, especially if you're deep into a project. Many newer cordless models boast longer lasting batteries, but balancing power and portability should guide your decision.
In summary, knowing the ins and outs of motor power, speed settings, and the choice between corded or cordless models allows stone workers to make informed decisions and maximize the effectiveness of their Dremel tools. This level of understanding ensures capable hands are at work, wielding the tools to create intricate and stunning stone works.
Types of Bits for Stone Work
The selection of the right bit can make or break your stone working experience when using a Dremel tool. These specialized bits are tailored for various materials and tasks, and choosing the correct one ensures efficiency, longevity, and a quality finish. Not only do different bits cater to distinct techniques, but they also help tackle a variety of stone types—from porous mediums to crystalline ones. A well-informed choice can save both time and frustration while elevating your craft to new heights.
Diamond Bits and Their Applications
Diamond bits stand at the pinnacle of stone working tools. They are renowned for their effectiveness on tough materials, which include granite, marble, and even some types of quartz. The real strength of diamond bits lies in their composition; they are coated with industrial-grade diamonds, allowing for precision cutting and detailed shaping.
You might wonder, "Why go for diamond bits instead of some other type?" The answer is straightforward: longevity and efficiency. While they might be on the pricier side, their durability often compensates for the upfront costs. Here are a few applications where diamond bits shine:
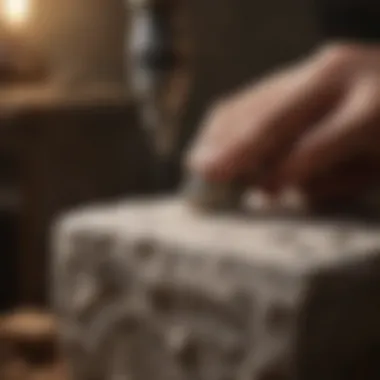
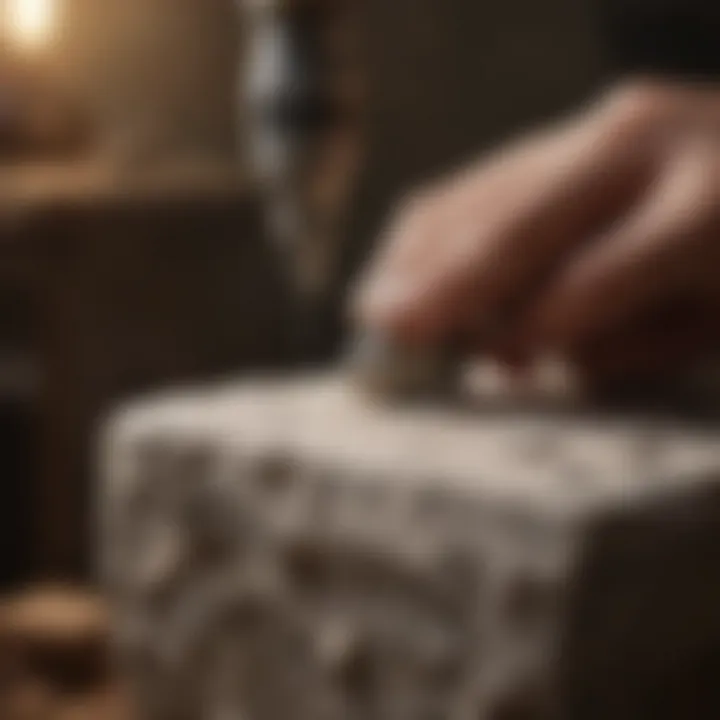
- Cutting intricate designs: When shaping stone into decorative pieces, diamond bits can follow fine lines with precision.
- Grinding edges: They smoothly grind down the edges of stones, making them safe and visually appealing.
- Drilling holes: When you need a hole in dense stone for pendants or hangings, diamond bits handle the job like a champ.
Carbide Bits for Harder Stones
Carbide bits are often the go-to when dealing with exceptionally tough stones. Unlike diamond bits, which shine in detailed work, carbide bits are rough and ready to take on hard materials, including hardened concrete and some forms of basalt. Their ability to withstand substantial wear and tear makes them indispensable for heavier-duty tasks.
If you're getting into stonework, consider these noteworthy characteristics of carbide bits:
- Versatile cutting edge: They can handle a broad spectrum of stones, making them great for various projects.
- Rugged reliability: Carbide is known for its toughness, translating into less frequent bit changes during a project.
- Affordability: Generally, carbide bits are easier on the wallet than diamond variants, striking a balance between cost and performance.
Specialty Bits and Their Uses
Specialty bits can transform your stone working experience, allowing for unique effects and precision tasks that standard bits can't handle. From engraving intricate patterns to adding texture, these bits are designed for specific stone applications.
Several interesting specialty bits include:
- Engraving bits: Designed for creating detailed images and text, engraving bits allow for adding a personal touch to your stone work. Perfect for gifts or personal projects, these bits make customization a breeze.
- Flame bits: Shaped like a flame, these bits are excellent for giving stones a textured finish. Hum-ble flames allow you to create an artistic surface that catches the eye.
- Routing bits: If you're looking to create channels or grooves in stone, routing bits will help you achieve that with more control.
Overall, understanding the types of bits you need can elevate your craftsmanship significantly. The right tools enable you to approach each project with confidence, reducing the learning curve while enhancing your creativity.
"Choosing the right bit is like having the right key for a locked door; it opens up the possibilities for what you can create."
Essential Techniques for Stone Working
When it comes to manipulating stone, having techniques that can produce effective results is essential. Whether you're a hobbyist or a professional, mastering these techniques can make the difference between a botched stone project and a remarkable masterpiece. Dremel tools are incredibly versatile, and knowing how to leverage their capabilities is crucial for achieving desirable outcomes in stone working. This section outlines the various techniques that can enhance your precision, detail, and overall effectiveness when working with stone.
Shaping and Sculpting Stone
Shaping stone involves more than just cutting; it requires a keen eye and a steady hand. Using a Dremel tool for shaping is especially advantageous, thanks to its ability to handle intricate designs.
- Selecting the Right Bit: Start with a diamond bit or a carbide bit, as both offer durability and the ability to cut through harder stones.
- Technique Matters: When shaping your stone, approach it gradually. Hold the Dremel tool at various angles to achieve different textures and shapes. For instance, a side-to-side motion can create smooth contours, while a more deliberate, steady motion may yield refined edges.
- Take Breaks: Working aggressively can generate a lot of heat; taking breaks allows the stone and tool to cool down, preventing damage.
Ultimately, patience and practice will yield better results. Each stroke should be deliberate, allowing you to understand how the stone reacts to the bit. Experiment with shapes on scrap pieces before diving into your main project.
Finishing Techniques
Finishing techniques can elevate a stone project from good to exceptional. They breathe life into the stone, revealing its natural beauty. Here are some pointers to achieving breathtaking finishes:
- Sanding: After shaping, switch to finer bits, such as sanding drums. Choose various grits, progressing from coarse to very fine to smooth out rough edges and surfaces.
- Polishing: For a truly polished finish, consider using polishing pads specifically made for stone. These pads bring out the stone’s luster, making it shine under light.
- Sealing: Once you are satisfied with the finish, seal your stone. This protects it from wear and helps retain its gloss, ensuring longevity.
Leveraging these finishing techniques not only enhances the visual appeal but also influences how the stone holds up over time.
Engraving Stone with Precision
Engraving adds personalization and flair to stonework. Using a Dremel tool for engraving can produce stunning, detailed designs, but it requires focus and technique. Here's how to do it effectively:
- Choose the Right Design: Start with simple designs before moving to more complex patterns. Use templates or stencils if you’re unsure.
- Steady Hands: A steady grip is vital. A shaky hand can lead to uneven lines. If necessary, brace your hands against a stable surface to minimize movement.
- Vary Pressure: Adjust the amount of pressure applied to the Dremel. Lighter pressure often yields finer lines, while applying more pressure gives bolder designs.
- Practice Makes Perfect: Experiment on a practice stone first. This reduces the likelihood of mistakes on your actual project, ensuring that you achieve a finish that matches your vision.
Engraving transforms stone pieces into personalized artworks, allowing you to express your creativity and skill.
Safety Precautions When Using a Dremel
When it comes to using a Dremel tool for stone work, safety should never take a backseat. Whether you're a beginner or a seasoned stoneworker, having a good understanding of safety practices can safeguard you against potential hazards. Accidental injuries can occur, especially with the high-speed operation of a Dremel tool. Therefore, it’s essential to incorporate safety measures into your workflow. Here’s a closer look at two critical areas: personal protective equipment and work environment considerations.
Personal Protective Equipment
Every artist has their tools, and safety gear is as important as the Dremel itself. Wearing personal protective equipment, or PPE, creates a barrier between you and potential danger. To ensure your safety while working, consider these essential items:
- Safety goggles: Protect your eyes from dust and flying debris. A simple spark can lead to severe eye damage.
- Respirator mask: Dust can quickly fill the air when working with stone; using a mask helps keep harmful particles out of your lungs.
- Gloves: While they may seem unnecessary, gloves can protect your hands from sharp edges and grinding debris. Look for options that provide dexterity, so you can still handle your Dremel comfortably.
- Ear protection: The high pitch noise of a Dremel in action can be harmful to your hearing if used for extended periods. Earplugs or earmuffs can help protect your hearing.
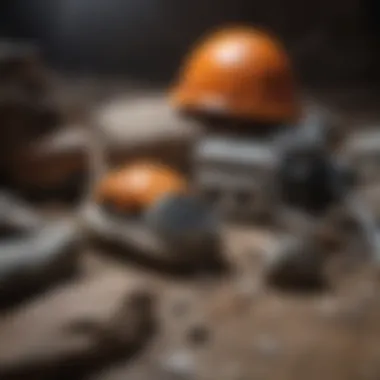
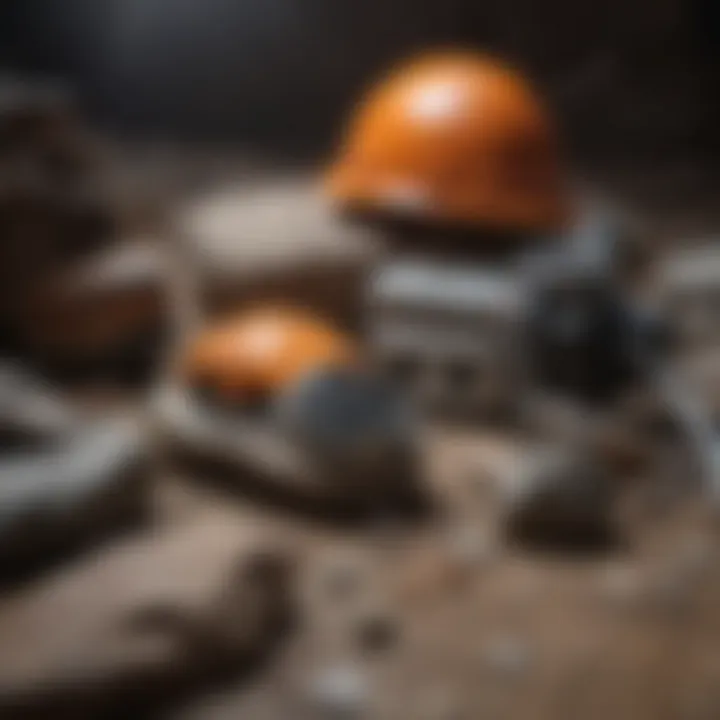
Bear in mind that your PPE is your first line of defense. It's not just about looking the part; it's about being smart and keeping yourself safe.
Work Environment Considerations
Another critical aspect to consider is the environment in which you're working. A cluttered or improperly set up workspace can lead to accidents that might easily be avoided. Here are some factors to take into account:
- Ventilation: Working with a Dremel can create a considerable amount of fine dust. Make sure your workspace is well-ventilated to help dissipate any airborne particles. Open windows or use a fan to keep air circulating.
- Clear clutter: Ensure that your workspace is tidy. Remove any unnecessary items that could be tripping hazards or could clutter your tool area.
- Stable surface: Use your Dremel on a stable and secure workbench. If you’re working on stones, make sure they are firmly held in place to prevent slipping.
- Proper lighting: Good lighting is key in ensuring that you maintain accuracy while working. A poorly lit area can lead to mistakes, which may be dangerous.
Fostering a safe working environment not only protects you but enhances the overall quality of your projects. Remember, taking the time to implement these basic safety precautions can make all the difference between a successful stoneworking session and an unfortunate mishap.
"Safety isn’t expensive, it’s priceless."
By equipping yourself with the right gear and maintaining a clean workspace, you'll be well on your way to enjoying the many benefits of using your Dremel tool safely.
Maintenance of Your Dremel Tool
Proper maintenance of your Dremel tool is crucial for the long-term functionality and effectiveness of your stonework endeavors. Many users underestimate the significance of this aspect, but regular upkeep not only ensures optimal performance but also extends the life of the tool. By investing a little time and effort into maintaining your Dremel, you can avoid many common pitfalls, including diminished cutting power, overheating, or even irreparable damage.
When you keep your tool in good condition, you also maintain the quality of your work. Clean and well-maintained equipment provides smoother operations and better results in your stone projects. Moreover, regular maintenance can save you money over time by preventing the need for expensive repairs or replacements.
Cleaning and Care for Longevity
Keeping your Dremel clean is fundamental for its longevity. After every use, it's wise to inspect the tool and remove any dust or debris that may have collected on it. A soft brush can be particularly effective in reaching tight spots. Note that accumulated particles can hinder performance and create wear and tear on the internal mechanisms.
Here are steps to ensure your Dremel remains in prime condition:
- Wipe the Exterior: Use a damp cloth to wipe the outer surfaces after each use. This removes dust, oil, and finger smudges that can accumulate over time.
- Maintain the Ventilation: Make sure that the ventilation slots are clear of any obstruction to prevent overheating. Blocked vents can lead to overheating which affects the tool's performance.
- Check the Motor: Occasionally, look inside the motor housing. Use compressed air to blow out dust if necessary. Be cautious, though, as access to the motor should only be done if you are comfortable with it.
- Lubricate Moving Parts: Apply a small amount of machine oil to the moving parts of the tool. This ensures that everything runs smoothly without excessive friction.
Adhering to these cleaning practices may seem like a chore, but it’s worth it for keeping your Dremel running like a well-oiled machine.
Replacing Bits and Accessories
Knowing when and how to replace your bits and accessories is essential in maintaining your Dremel tool’s effectiveness. Dull bits can not only slow down your work but also impact the quality of your projects. As the saying goes, a sharp tool is a happy tool.
Consider the following when replacing:
- Inspect Regularly: After a few projects, check the condition of your bits. Look for signs of wear such as chips or dull edges. If they no longer cut or engrave effectively, it's time for a replacement.
- Choose Quality Materials: Not all bits are created equal. Opt for high-quality replacements from reputable brands to ensure compatibility and performance.
- Store Properly: After use, store your bits in a designated container rather than tossing them into a drawer. This protects them from damage and helps prolong their life.
- Stay Informed: Keep up with new accessories that can improve your Dremel use. Some may offer innovative features that enhance your stone working experience.
By proactively replacing worn-out bits and properly caring for your accessories, you lay the groundwork for both your current and future stonework projects.
Enhancing Your Stone Working Experience
Enhancing your stone working experience with the Dremel tool is not just about utilizing the tool itself; it involves cultivating a skill set and interface with various accessories to achieve the best results. The right accessories can elevate your craftsmanship from ordinary to extraordinary, directly impacting the precision, efficiency, and creativity of your projects. Additionally, it’s crucial to understand how to integrate your Dremel with other tools to maximize its potential.
When it comes to stone work, there’s a whole world of creative possibilities waiting to be explored. Knowing which accessories to use can significantly improve your workflow and the quality of your finished products. Think of accessories as the seasoning that brings out the flavors of a dish. If you skimp on them, you might end up with bland results.
Recommended Accessories
The Dremel tool shines brightest when paired with the right accessories. For those working with stone, several types of bits and attachments are essential to delivering high-quality results.
- Diamond-Coated Bits: These are your go-to for any cutting or engraving task on stone. They come in various shapes and sizes, perfect for different tasks like shaping or detailing.
- Carbide Bits: Stronger than your average steel, carbide bits are beneficial for working with harder stones. They maintain their sharpness longer, making them cost-effective in the long run.
- Sanding Discs and Bands: After shaping your stone, these accessories allow for smooth finishing. They come in different grits, so you can choose how fine you want to go.
- Flexible Shaft Attachment: This isn’t just about versatility; using a flexible shaft lets you get into tighter spaces or work from awkward angles without straining your wrist.
- Dust Collection Attachments: Keeping your workspace clean while working with stone is crucial. Dust collectors help you maintain visibility and keep your breathing air cleaner, adding an extra layer of health safety.
By investing in these accessories, you're not just purchasing materials; you're investing in the quality of your craft.
Combining Techniques with Other Tools
The beauty of working with a Dremel tool is its adaptability. Combining techniques with other tools enhances your abilities and opens the door to diverse styles and projects. Pairing up can provide various advantages that you might miss out on when relying solely on a single tool.
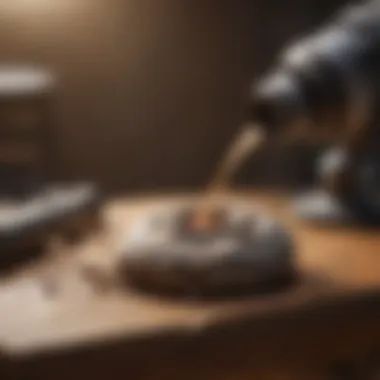
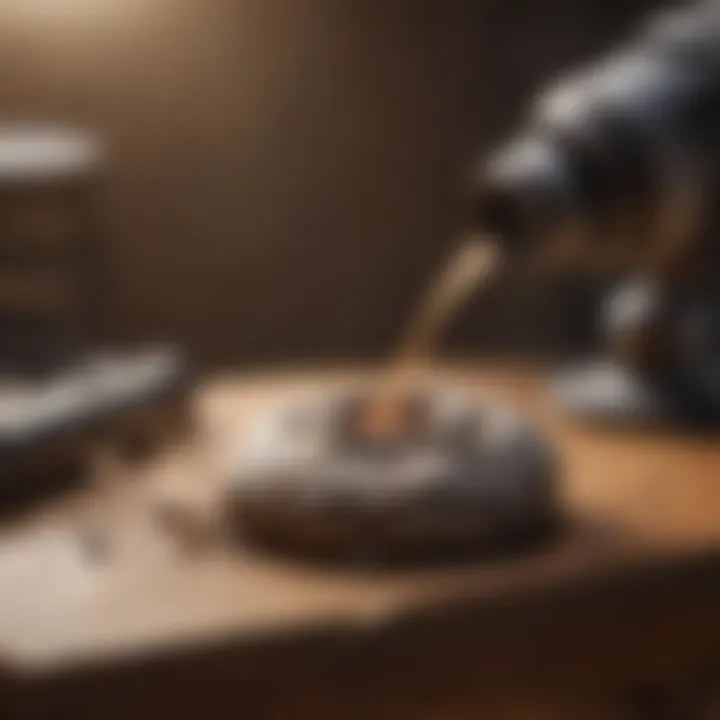
- Hand Tools: Sometimes the old-fashioned way is the best. Tools like chisels can be used for rough shaping before you get to the fine details with your Dremel. A simple hammer and chisel can carve out the bulk of material quickly.
- Angle Grinders: For more robust materials, angle grinders can take on major shaping duties. After you’ve done the heavy lifting, you can switch to your Dremel for the precision work.
- Polishing Machines: If you’re looking for a glass-like finish, employing polishing machines can truly elevate your stone pieces. The Dremel can then be utilized for intricate detailing and final touches.
- Rotary Tools for Drilling: Some projects might require holes for mounting. Using a dedicated drill before detailing with the Dremel allows you to achieve holes that are precise and clean.
Combining these techniques with your Dremel can help you become a more versatile craftsman and push creative boundaries.
Remember, the aim is to foster a holistic approach to stone crafting, making your Dremel tool a key player in your toolkit.
The intersection of accessories and techniques ultimately shapes your overall stone working experience. It’s not merely about having the right tools; it’s about knowing how to deploy them effectively to bring your artistic vision to life.
Common Challenges and Solutions
When working with stone using a Dremel tool, enthusiasts often encounter various hurdles that can impact their creativity and productivity. Understanding these challenges and how to address them is essential for both quality work and enjoyment. This section sheds light on some common issues faced by users, providing insights into effective strategies to navigate these obstacles. Knowing how to tackle these problems not only saves time but also enhances the overall stoneworking experience.
Dust Management Strategies
Working with stone can create a significant amount of dust, which poses not only visibility problems but also health risks. Proper dust management is, therefore, paramount for anyone serious about stone work.
- Use a Dust Hood or Collection System: Installing a dust hood or using a vacuum attachment specifically designed for your Dremel setup can greatly minimize airborne dust. A vacuum can collect debris in real-time, which keeps your workspace clean while allowing you to focus on your project.
- Wet Methods: Where possible, wetting the workspace can help control dust. Spraying water on the stone while working can create a slurry that binds the dust together, making it easier to clean up.
- Work Outdoors: If your project allows it, take your work outside. Natural airflow will help disperse the dust much more effectively than a confined workspace. Be mindful of wind conditions, though, as gusts can carry dust back toward you.
- Personal Protective Equipment (PPE): Always wear a good dust mask or respirator to protect your lungs from harmful particles. Additionally, goggles with side shields can protect your eyes from fine debris.
"Safety is not just about protecting yourself while working; it’s also about enhancing your ability to work for the long haul."
By implementing these strategies, you not only preserve your health but also improve your focus on fine details of your work.
Overcoming Material Limitations
Stone varies in density and hardness, which can present unique challenges during projects. Here are some tactics to effectively manage these limitations:
- Know Your Material: Understanding the type of stone you’re working with is crucial. Softer stones, like soapstone, require different techniques and bits compared to harder materials such as granite. Researching ceramics or crystals can also inform your approach.
- Select the Right Bits: Using the right bit for your specific stone type is essential. As mentioned previously, diamond bits excel on tougher materials, while carbide bits are generally useful on softer stones. Each bit has its strengths, and knowing their limits can help avoid premature wear and tear.
- Adjust Speed Settings: Many Dremel models allow you to change the speed. When working with tough stones, using a lower speed may actually yield better results, as it reduces heat build-up and prolongs bit life. Conversely, higher speeds can help finesse more delicate projects.
- Use Consistent Pressure: When working with hard materials, applying consistent pressure is important. Too much force might lead to bit breakage, while too little can decrease effectiveness. Find a balance that allows the bit to do its work without pushing too hard.
Exploring Creative Possibilities
The realm of stone working with Dremel tools isn’t just about achieving functional results; it’s also a canvas for unearthing creativity. The Dremel enables users to embark on unique artistic journeys, where imagination can flourish alongside craftsmanship. Embracing creative possibilities allows both beginners and seasoned users to explore unconventional uses of the tool, pushing boundaries beyond traditional stone crafting.
When considering creative avenues, it’s vital to recognize several specific elements that can enhance the experience. One such element is the variety of bits available, each lending itself to different textures and finishes. Moreover, the adaptability of the Dremel means it can cater to various projects, from delicate engravings to robust sculpting. Using these innovative methods can result in pieces that not only serve a purpose but also spark conversations.
A key benefit of exploring these avenues is the potential for personal expression, which is at the heart of artistic endeavors. Stone, in its raw form, has its own character, but when shaped with tools like the Dremel, it transforms into something that echoes the creator’s vision. As such, creating a personal piece can offer a deep sense of fulfillment.
Considering the nuances of the Dremel's application also opens avenues for honing skills further. As users interact with the material, they develop an instinct for how to shape it effectively. Whether one is aiming for a simple engravement or a more cohesive art piece, understanding the subtleties makes all the difference.
"Art enables us to find ourselves and lose ourselves at the same time."
— Thomas Merton
To maximize the creative potential, a few factors come into play:
- Experimentation: Don't shy away from trying various techniques. The mistakes often lead to unexpected masterpieces.
- Inspiration from Others: Looking at community projects or even browsing online platforms can spark new ideas.
- Adapting Tools: Sometimes, creative transformations happen when tools are used in unexpected ways. A common bit might yield different effects based on the technique employed.
The nature of the materials can also provide guidance. For example, softer stones may allow for more intricate designs, while harder variants might require robust techniques. Thus, understanding the differences in materials also heightens the creative journey.
Lastly, accommodating personal preferences, habits, and inspirations is crucial for those seeking to push limits. Through project ideas uniquely tailored to both beginners and advanced users, the possibilities become endless.
End
In wrapping up our in-depth look at the Dremel tool for stone work, it becomes clear how essential this device is for both hobbyists and professionals alike. Rather than viewing it merely as a tool, it serves as a gateway into the world of advanced stone crafting, allowing individuals to express their creativity and technical skill in various projects. From shaping raw stone to creating intricate designs, the Dremel tool simplifies processes that would otherwise require significant manual effort or more complex equipment.
Summarizing Key Takeaways
Several key insights stand out when reflecting on the topics discussed:
- Versatility: The Dremel tool's adaptability across different types of stone materials showcases its broad usability. The variety in bits and attachments means that it can cater to a multitude of tasks, from basic cutting to delicate engraving.
- Safety First: We highlighted the critical nature of safety precautions when operating a Dremel. Wearing appropriate personal protective equipment and ensuring a clean workspace are paramount to preventing accidents and injuries.
- Maintenance Matters: Regular maintenance practices, such as cleaning and changing bits, significantly extend the life of the tool. Understanding the maintenance routine can save time and money in the long run.
- Creative Exploration: The possibilities with the Dremel are extensive, with any stone as a potential canvas. The journey of stone working can lead to projects that both challenge and fulfill.
Encouragement for Further Exploration
It’s important to delve deeper and continue cultivating both skills and knowledge in stone work. Don't let a few setbacks with tricky stones or intricate designs discourage you; instead, use them as learning opportunities. Consider joining online forums or local groups dedicated to rock and fossil collecting. Engaging with peers can provide fresh perspectives, innovative techniques, and new project ideas.
Innovate by experimenting with textures, colors, and shapes you haven't tried before. Visit resources like Reddit for communities sharing experiences and projects, or explore articles on Britannica for a broader understanding of stone materials and their characteristics.
Ultimately, whether you're a novice just starting your journey or a seasoned expert, the world of stone crafting with a Dremel tool is as boundless as your imagination. So, pick that tool up, get your stones in place, and let your creativity flow in ways that may surprise you.