Exploring the Dremel Stone Cutter: A Tool for Collectors
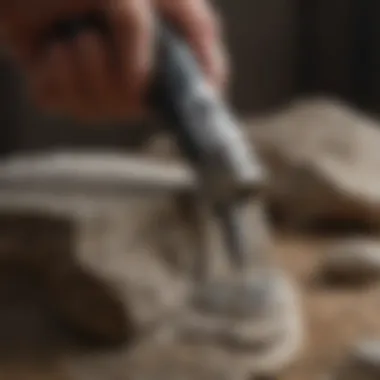
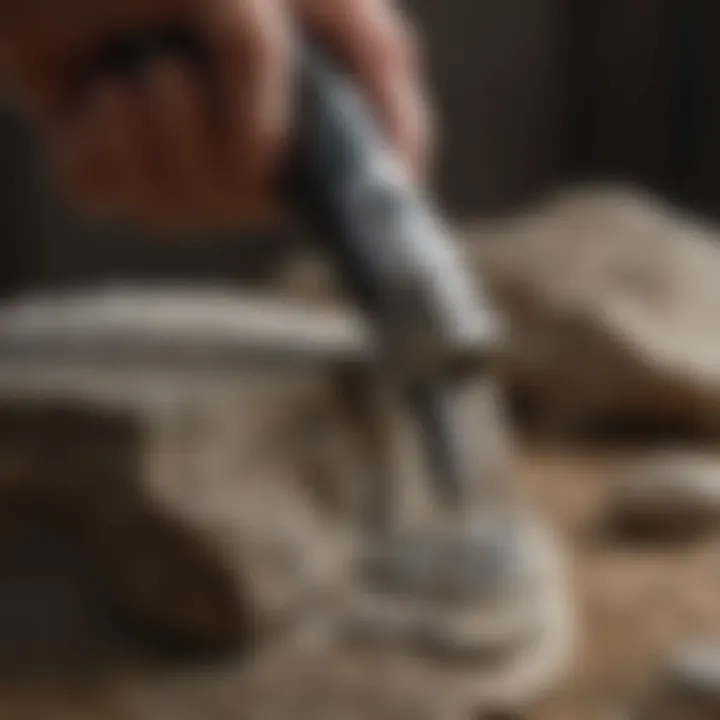
Intro
The Dremel stone cutter has carved a niche among enthusiasts and amateurs alike, particularly for those with a keen eye for rocks and fossils. This tool isn't merely a gadget; it's a bridge connecting passion for geology and the art of crafting. With precision and versatility, it has become indispensable for many collectors who find joy in shaping and refining the natural beauty of stones and fossils.
Whether you're deep in the field unearthing a fossil, or at home polishing a cherished rock specimen, the Dremel stone cutter holds immense potential. Its unique capabilities allow users to explore a myriad of techniques, each unfolding new possibilities for creativity and learning.
As we delve deeper into what makes this tool essential, definitely keep an eye on its features and safety practices. There’s more than meets the eye behind this device that has become beloved among experts and newcomers alike.
Prologue to the Dremel Stone Cutter
The world of stone cutting is both fascinating and demanding, especially for those who delve into the realms of collecting and crafting. The Dremel Stone Cutter, a notable player in this arena, serves as a bridge between creative expression and meticulous craftsmanship. This introductory section unpacks the significance of the Dremel Stone Cutter by examining its history, development, and the attributes that render it an indispensable tool for hobbyists and collectors alike.
History and Development
The origins of the Dremel Stone Cutter trace back to a time when the need for precision tools was paramount. Founded in 1932 by Albert J. Dremel in Racine, Wisconsin, the company initially focused on producing rotary tools for woodworkers. Over the decades, this eager innovation bridged the gap into stone cutting, where collectors and crafters began seeking reliable equipment to work with harder materials.
The advancement of technology and the demands of craftsmen led to the evolution of this tool. Development over time has introduced more ergonomic designs and motor power increases, enhancing both productivity and user comfort. What started as a mere rotary tool evolved into a versatile companion for both amateurs and seasoned professionals in stone carving, jewelry making, and fossil restoration.
Key Features
The Dremel Stone Cutter is not just any run-of-the-mill rotary tool; it boasts specific features that cater to the unique needs of stone cutters. These features include:
- Variable Speed Control: Offers flexibility to adjust RPMs which is crucial when working with different stone types.
- Ergonomic Design: Ensures prolonged use without discomfort, making it user-friendly for those long projects.
- Interchangeable Bits: A variety of attachments allow users to switch seamlessly between cutting, grinding, and polishing depending on their project requirements.
- Compact Size: The light weight of the tool means it’s easy to handle while maneuvering along intricate designs or tight spaces.
The advantages of these features extend beyond mere functionality. They inspire confidence among collectors and hobbyists, allowing for more intricate and personalized projects. It’s not simply about cutting stone; with the Dremel Stone Cutter in hand, enthusiasts can unlock creativity and push boundaries in their craft, solidifying it as an essential element in their toolkit.
"For many hobbyists, the Dremel Stone Cutter is more than a tool; it's an instrument of creation and discovery."
In summary, understanding the importance of the Dremel Stone Cutter forms a foundational perspective from which users can appreciate the breadth of its capabilities. Recognizing its history and key features sets the stage for deeper exploration into its mechanisms, applications, and how hobbyists can harness its potential for both practical and artistic endeavors.
Understanding the Mechanism
Understanding how the Dremel stone cutter operates is crucial for any collector or hobbyist looking to utilize it effectively. The functionality of this tool goes beyond mere cutting; it embodies an intricate balance of engineering and user control that empowers a wide range of applications in stone and fossil crafting. Grasping its mechanisms offers insight into optimizing its use, maintenance, and safety.
Components and Functions
At first glance, the Dremel stone cutter may look like a simple tool, but it’s a marvel of precision engineering. The primary components include:
- Motor: The heart of the device, driving all other parts with power and speed. It typically features variable speed settings, allowing users to tailor the cutting speed based on the specific stone material.
- Cutting Bits: These are interchangeable attachments that define the tool's versatility. Whether you're slicing through hard granite or shaping delicate minerals, having the right bit is essential.
- Collet: This part securely holds the cutting bits in place. A snug fit ensures that the bit doesn’t wobble, which could lead to inaccuracies in cutting or grinding.
- Base and Housing: Providing stability, these components also house the motor and protect the user from flying debris.
These fundamental elements work together harmoniously, ensuring smooth operation during various tasks. Each component fulfills a specific role, and knowing how they interact can enhance your efficiency and accuracy when cutting or shaping stone.
Operating Principles
The operating principles of the Dremel stone cutter are rooted in basic mechanics but have applications that can seem quite sophisticated when put into practice. Here’s how it all comes together:
- Power Source: The tool is powered, typically by electricity, converting electrical energy into mechanical energy. This transformation drives the motor, which spins the attached cutting bit at high speeds.
- Rotational Motion: The motor generates rotational motion, which is transferred to the cutting bit. It’s that high-speed rotation which cuts through stone, as the angular velocity creates enough friction to displace material.
- User Control: By adjusting the speed settings, users can control how aggressively the tool operates. Lower speeds are suitable for delicate work, while higher speeds can tackle tougher materials. This responsiveness is vital for achieving desired results, allowing for precision when it matters.
- Guidance: One of the often overlooked aspects is the importance of user guidance. The pressure applied and the angle at which the tool operates can all influence the final outcome. Mastering this element is often the key difference between average cuts and professional results.
Understanding the mechanism behind the Dremel stone cutter not only enhances your cutting precision but also extends the lifespan of the tool by minimizing operational risks.
Equipped with this foundational knowledge, collectors and hobbyists can approach projects with confidence, knowing that they have the skills to fully utilize the Dremel stone cutter’s capabilities.
Applications in Stone Cutting
The Dremel stone cutter plays an integral role in the world of stone cutting, making it an indispensable tool for both hobbyists and collectors. Its diverse functionalities enable users to tackle a wide range of projects, from fine-detail work on delicate stones to rough cutting of larger materials. Understanding how to harness the capabilities of this tool is crucial in optimizing its use for specific applications.
Techniques for Beginners
Navigating the beginning stages of using the Dremel stone cutter can feel like stepping into uncharted territory, but with a bit of guidance, beginners can effectively get their feet wet without feeling overwhelmed. Here’s a handy breakdown of techniques to securely start your stone cutting journey:
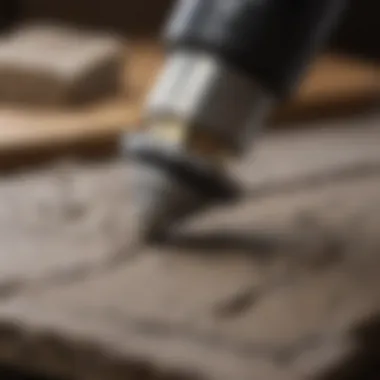
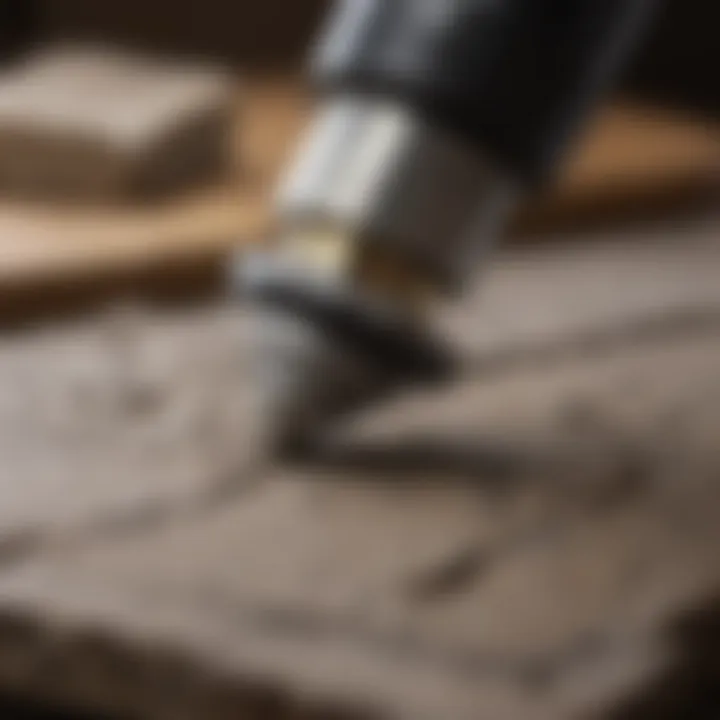
- Choose the Right Bit: Using the correct Dremel bit is foundational. For softer stones like alabaster, consider diamond-tipped bits, while harder materials like granite may require carbide bits. Selecting the right tool directly affects the quality of your work.
- Stable Base: Always work on a solid surface. A workbench or a sturdy table can help keep your material steady, preventing unnecessary accidents. It’s like trying to cut a steak on a wobbly surface; it just doesn’t bode well for the outcome.
- Practice Control: Initially, it’s best to practice on scraps. Developing a steady hand allows you to control the depth and speed of your cuts, leading to smoother results. Think of it as a painter mastering their brush strokes.
- Use the Right Speed: The Dremel offers variable speed settings. Beginners should start with a lower speed to maintain better control, especially on intricate details.
"Even the greatest artists once started as learners, gaining skills through patience and practice."
These techniques create a solid foundation for beginners and encourage a more confident approach to stone cutting.
Advanced Techniques for Experts
As one becomes more proficient with the Dremel stone cutter, the range of possibilities expands significantly. Advanced techniques can transform a project from ordinary to extraordinary, and they involve a deeper understanding of both tools and materials.
- Custom Shaping: Experts often use custom jigs or templates to create intricate shapes that would be difficult to achieve freehand. These devices hold the stone in place and guide the cutter, much like a GPS guiding you on a winding road.
- Multi-Layer Cutting: This technique involves cutting through layers of material to create depth in your designs. It’s particularly useful in projects where contrasting stones are used for visual effects, enhancing the final result.
- Texturing Rocks: Beyond simple cutting, the Dremel can be used to create various textures on stone surfaces. By employing different bits and adjusting speeds, it's possible to achieve finishes that mimic nature itself.
- Engraving Details: For those looking to personalize their creations, engraving techniques using the Dremel can add an extraordinary level of sophistication. Engraving names or designs on stones can turn a simple rock into a treasured keepsake.
- Working with Different Materials: Advanced users often experiment with mixed media, combining stone with resin or metal. This requires a more nuanced approach, but the results can be stunning.
Mastering these advanced techniques not only showcases one’s skill but also allows for creative expression that can elevate any stone project beyond its basic form.
Safety Measures and Best Practices
When wielding the Dremel Stone Cutter, prioritizing safety cannot be overstated. This tool, while incredibly versatile, can pose risks if handled improperly. Focusing on safety measures is not just about protecting oneself; it's about ensuring a smooth crafting experience and maximizing the tool's potential without injury. Collectors and hobbyists engaged in stone and fossil work must adopt both protective gear and a well-considered workspace setup.
Protective Gear
The right protective gear acts as the first line of defense against potential hazards. This gear varies based on the nature of the work but always includes key elements:
- Safety goggles: Made of shatterproof material, these should create a snug fit around the eyes to block out debris.
- Dust mask or respirator: Working with stone creates a fine dust that can be harmful if inhaled. Invest in a respirator with filters suitable for particulate matter to prevent respiratory issues.
- Gloves: A pair of durable, cut-resistant gloves is essential. They provide grip, protect against sharp edges, and keep hands safe from the heat generated while cutting.
- Ear protection: Dremel tools can become quite noisy. Using earplugs or noise-canceling headphones guards against hearing damage, especially during prolonged sessions.
Using these protective items not only adds to safety but also allows for greater focus on the project without worry. Ensuring that all gear is in good condition and suited for the task at hand is equally important. A chipped pair of goggles or an old dust mask won't offer the necessary protection.
Workspace Setup
An organized and safe workspace is equally as crucial as protective gear. An untidy area can lead to accidents or distractions, which may result in mistakes or injuries. Here's how to create an effective workspace for using the Dremel Stone Cutter:
- Choose an appropriate location: Select a workspace with ample ventilation to disperse dust. Outside or in a dedicated workshop is ideal, as it reduces the need to clean up later.
- Use a stable surface: A sturdy workbench or table that can endure the vibrations of the cutting process is essential. Make sure it’s not cluttered with unrelated items, as a clean space minimizes the risk of accidents.
- Proper lighting: Good lighting is vital. It helps you see the finer details of your project without straining your eyes, making you more accurate.
- Storage for tools and materials: Keep your Dremel, its attachments, and any stones organized. A tool box or a designated shelf prevents clutter and reduces the risk of misplacing essential items when switching tasks.
"An ounce of prevention is worth a pound of cure." Having the right setup and gear can save a lot of hassle down the road.
By incorporating these safety measures and best practices, collectors and hobbyists alike can use their Dremel Stone Cutter with confidence. It’s about enhancing the experience overall while ensuring that the focus remains on the art and science of stone crafting.
Maintenance of the Dremel Stone Cutter
Maintaining the Dremel Stone Cutter is not just a routine chore; it's a vital part of ensuring that this versatile tool operates at its peak performance for years to come. When used frequently by collectors and hobbyists, the wear and tear on the machine can gather like weeds in an untended garden. A little thoughtful care goes a long way in maximizing both the longevity and efficiency of the cutter. By focusing on a couple of key areas—cleaning procedures and understanding replacement parts—you can keep your Dremel stone cutter running as if it were brand-new.
Cleaning Procedures
Keeping your Dremel Stone Cutter clean isn't merely about aesthetics; it directly impacts the tool's effectiveness. Let's face it, a dirty cutter is more like a rusty old key. It won't perform nearly as well. Dust and residue from stones can build up, causing the machine to overheat or perform unevenly. Here’s a straightforward way to keep it spick and span:
- Unplug the Tool: Safety first! Always disconnect your Dremel before you begin any cleaning.
- Use Compressed Air: A quick blast of compressed air can dislodge dust and small particles from the ventilation slots and other crevices. This is often more effective than a damp cloth.
- Wipe the Exterior: After using air, take a soft, lint-free cloth and a mild detergent to wipe down the exterior of the cutter. Get into those nooks and crannies where grime likes to hide.
- Check the Bits: Don’t forget to clean the cutting bits themselves! Soaking them in a solution of warm, soapy water can do wonders. Just make sure to dry them thoroughly afterward.
By adhering to these steps regularly, the performance will not only remain consistent, but the lifespan of the tool can be significantly extended.
Replacement Parts and Upgrades
Even with diligent cleaning, parts will inevitably wear out or need upgrading. It’s like shield replacement for a knight—essential for continued success in battle. Knowing when and what components to replace can save novice users from unnecessary headaches. Here's what to keep an eye on:
- Cutting Bits: These are the workhorses of the Dremel and will wear out faster than the rest of the tool. Keeping a variety of bits on hand ensures you're equipped for any stone you encounter.
- Bearings: Some users might overlook bearings, but they're crucial for smooth operation. If your cutter starts to make an unusual noise, it might be time to swap these out.
- Motor Brushes: Over time, the motor brushes can wear down. Inspect them regularly. Replacing old brushes can breathe new life into your stone cutter.
- Upgrading to the Latest Model: If you find yourself craving more power or features, consider investing in a newer model. Dremel often releases updates with enhanced capabilities, such as improved speed settings or compatibility with more accessories.
Pro Tip: Always use genuine Dremel replacement parts. Off-brand components might save you a buck or two at first, but they often lead to issues down the line.
Remember, taking care of the Dremel Stone Cutter through regular cleaning and timely replacement of parts is not just advisable; it’s essential for any serious hobbyist or collector aiming for excellence.
Complementary Tools for Collectors
When diving into the world of stone cutting, especially for collectors of rocks and fossils, the Dremel stone cutter shouldn’t be the sole hero in your toolbox. While it’s a fantastic device on its own, adding complementary tools can optimize precision, enhance safety, and even broaden the range of creative possibilities for hobbyists. Understanding what other tools pair well with the Dremel can maximize its use and allow for more nuanced projects.
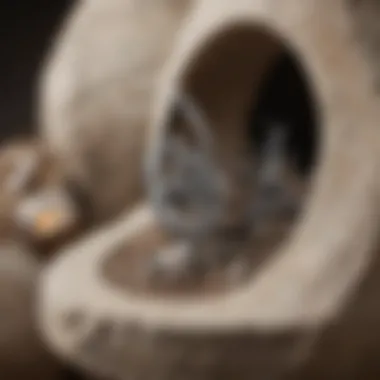
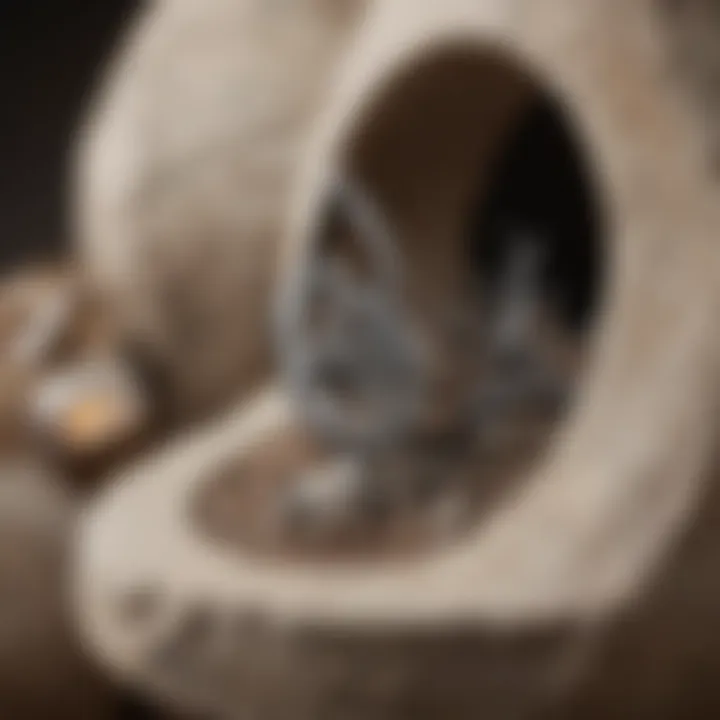
Hand Tools for Precision Work
In any crafting or collecting endeavor, precision matters greatly, and hand tools provide that meticulous touch the Dremel may sometimes lack. Popular among avid collectors, tools such as chisels, files, and rasps can help shape stones more delicately. These tools allow for finer control and detail.
- Chisels: A range of chisels in assorted shapes and sizes can help you carve out specific regions of a stone. They offer significant versatility for getting into tight spots where a power tool can't reach.
- Files: When it comes to smoothing the edges of freshly cut stones, files can be your best friends. Selecting a variety of files – from coarse to fine-grained – can yield different finishing effects.
- Rasps: Rounding off corners or shaping surfaces can be done efficiently with rasps, great for creating organic shapes in your pieces.
The beauty of hand tools lies in their tactile and immediate nature, allowing artisans to respond dynamically as they work. Not only does this improve the quality of the finish, but it also provides a deeply rewarding experience that is often missing with solely electric tools.
Power Tools Integration
While the Dremel stone cutter is undoubtedly a star player, the integration of other power tools can elevate your projects to new heights. Not all jobs can be performed efficiently with a single tool, especially when large stones or tough materials come into play. Here’s what to consider for enhancing your toolkit:
- Angle Grinder: For heavy lifting, angle grinders can cut through tougher materials and larger stones. They are powerful enough to handle bulk operations, which can then be refined with the Dremel.
- Rotary Sanders: After you’ve cut your stone into the desired shape, a rotary sander can help polish and add shine. This is particularly critical for collectors looking to display their items, as a smooth, gleaming piece can catch the eye.
- Dust Extraction: Power tools can create a significant amount of debris. A good dust extraction system is imperative to maintain a safe workspace and improve visibility during projects.
Integrating power tools with the Dremel allows for versatility; it means you can transition seamlessly from rough shaping to finishing touches. Each tool plays its role, contributing to a finished project that is both aesthetically pleasing and unique.
The combination of power tools with hand tools creates a comprehensive workflow, maximizing efficiency and creativity.
Ultimately, the right set of complementary tools can transform the stone crafting experience, taking it from simple cutting to a full-fledged artistic pursuit. A holisitic approach not only enhances the process but can also lead to more innovative techniques and outcomes.
Innovative Techniques Using the Dremel Stone Cutter
When it comes to utilizing the Dremel stone cutter, imagination is an invaluable asset. Beyond its primary function of cutting stone, this tool can be employed in a myriad of innovative ways. Harnessing its versatility opens doors to artistic opportunities and enhances the capabilities of hobbyists and collectors alike.
With the rise of personalized crafts, the Dremel stone cutter has found a secure place in the hearts of jewelry makers and collectors seeking to create unique pieces. The potential in utilizing this tool effectively can transform raw materials into one-of-a-kind treasures, adding aesthetic value and personal touch.
Fitting Stones for Jewelry Making
Fitting stones for jewelry making is one of the most captivating applications of the Dremel stone cutter. It allows artisans to shape and polish stones with precision, ensuring they fit perfectly into their desired settings, whether that be rings, necklaces, or earrings. The process often starts with selecting the right stone; think of beautifully colored agates or sparkling quartz. Once a suitable candidate is chosen, the Dremel can help refine its edges and surface.
Utilizing a diamond-tipped bit, you can carefully guide the cutter along the stone, creating a smooth and contoured finish. Because most stones can be quite tough, having the right technique is key. A gentle touch coupled with the right speed setting makes all the difference.
Key benefits of this technique include:
- Customization: Tailor each stone to your specific design requirements.
- Efficiency: Save time compared to manual methods.
- Transportation of Ideas: Effectively bring your visions to life with accuracy.
Before you begin, it’s a good idea to practice on scrap stones to hone your skills. A solid grip and steady hand will yield the best results, and safety glasses are a must. Dremel tools also come with various attachments that can further assist in the polishing process, allowing for different finishes that suit your style.
In addition, connecting with communities on platforms like Reddit can provide inspiration and tips from seasoned jewelers who might share their techniques and insights.
Creating Custom Collectible Displays
Another standout use of the Dremel stone cutter is in creating custom collectible displays. Whether you own a collection of rare fossils or exquisite minerals, displaying these pieces can elevate the aesthetics of your space while showcasing their natural beauty. The Dremel provides the ability to adapt bases or mounts tailored to the distinct shapes and sizes of your treasures.
For example, when designing a display for fossils, you might want to craft a specialized stand that highlights the specimen’s profile. This can involve cutting stones to create a sturdy pedestal or drilling holes to insert supports. The sturdy nature of stone ensures that your collectibles stand the test of time while maintaining an elegant look.
Benefits related to creating custom displays include:
- Personalization: Craft displays that resonate with your unique collection.
- Enhanced Appeal: A well-done display can capture the eye and stimulate interest.
- Flexibility: The Dremel allows for intricate adjustments, helping to create flawless designs.
To map out your ideas effectively, consider sketching designs before diving into the cutting process. This can help clarify how you want each piece to interact with others, ensuring a cohesive and aesthetically pleasing arrangement. Similarly, sharing your creations on platforms like Facebook can also yield feedback and suggestions from fellow collectors.
In addition, as you navigate the world of cutting and displaying stones, remember that experimentation is part of the journey. Embrace the trial and error; it’s where new techniques are often born. The Dremel stone cutter isn’t just a tool. It’s a gateway to artistic expression and craftsmanship.
Case Studies: Successful Projects
In delving into the practical applications of the Dremel Stone Cutter, case studies serve as an essential bridge between theory and practice. They illuminate the myriad ways this tool can be employed, offering both concrete examples and valuable insights into the benefits and challenges faced by collectors and hobbyists. Through these studies, readers not only see the potential that the Dremel Stone Cutter unlocks, but they also gain an appreciation for the precision required in stone working. Each project exemplifies unique techniques and showcases how innovations can be applied effectively, making the Dremel an invaluable ally in any collector's toolkit.
Restoration of Fossils
Fossil restoration is a meticulous process that requires both skill and patience. The Dremel Stone Cutter, with its various attachments, provides the needed versatility to tackle such intricate projects. One notable case involved the restoration of a fossilized dinosaur bone, which required removing excess rock and sediment while retaining the integrity of the bone itself. This delicate balance demanded not just the right tools but also a thoughtful approach.
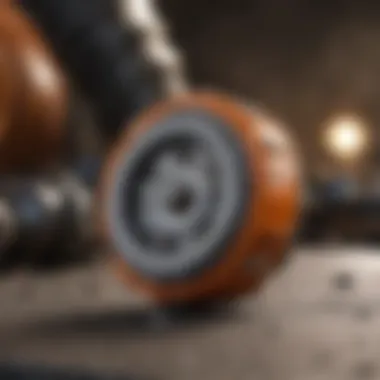
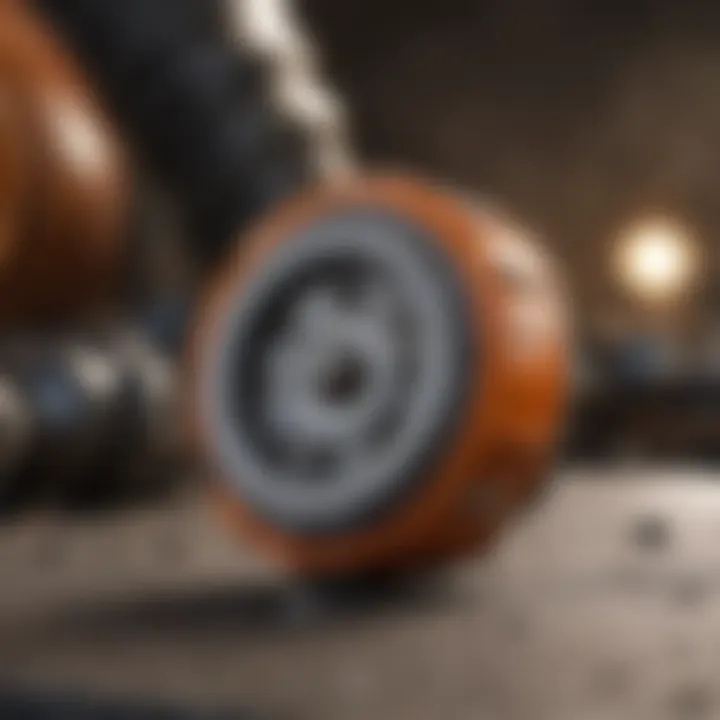
Using a fine grinding attachment, hobbyists can carefully expose the details of a fossil. Here, the precision of the Dremel plays a pivotal role. Many enthusiasts emphasize the importance of work in small increments; by doing so, they can prevent over-excavation. It's like trying to unspool a delicate thread from a tightly woven tapestry—you don’t want to yank on it too hard or risk tearing the entire fabric.
There are also some important considerations to keep in mind:
- Choice of Bits: Using the right grinding bits can make a world of difference. Specific attachments allow for different levels of precision, a key factor in fossil restoration.
- Technique: Employing a light touch and a gentle angle of approach reduces the risk of breakage during restoration.
- Patience is Key: Slow and steady wins the race here; rushing through the process often leads to mishaps.
"Restoration isn’t just about fixing; it’s about understanding the story behind each piece. It requires a careful hand and a keen eye."
The Dremel Stone Cutter furthers this understanding by making it easier to navigate these sensitive operations.
Unique Rock Sculptures
The artistry of rock sculpture is perhaps one of the more fascinating applications of the Dremel Stone Cutter. Artists have leveraged this tool for soft stone mediums to create unique, eye-catching sculptures—from intricate floral designs to detailed animal figures. One striking example is the work of an artist who used the Dremel to carve a series of small owls out of soapstone. Each piece conveys exceptional detail, from textured feathers to delicate facial expressions.
Scultping with the Dremel offers several advantages:
- Versatility: With the many attachments available, artists can switch between shaping, grinding, and polishing with ease.
- Control: The hand-held nature of the Dremel allows for a level of maneuverability that larger tools simply can’t offer. This aspect is crucial for delicate tasks and fine details.
- Rapid Execution: Compared to traditional chiseling methods, the Dremel significantly reduces the time taken to complete a sculpture, allowing for more experimentation.
However, sculptors must remain mindful of specific challenges:
- Material Selection: Not all stones are created equal. Some harder stones may require a different approach than softer ones, impacting the choice of attachments and the overall technique.
- Safety Measures: The process can be dusty and noisy, requiring precautions in the workspace, like wearing a mask and safety goggles.
These case studies illustrate the profound possibilities available to both amateur and expert users of the Dremel Stone Cutter. The tool does not just serve functional purposes; it also acts as a conduit for creativity and restoration. Whether diving into the past with fossils or carving a unique sculpture, the potential for innovation is vast, and the results can be nothing short of extraordinary.
Common Challenges and Solutions
In the realm of stone cutting, even the most seasoned users can encounter obstacles. Understanding these common challenges and their solutions is essential for maintaining workflow and achieving high-quality results. For rock and fossil collectors alike, knowing how to navigate difficulties can greatly enhance the experience of using the Dremel stone cutter. This section addresses two specific challenges: dealing with breakage and addressing power issues.
Dealing with Breakage
Breakage of stones can be a real heartbreaker, especially when working on deeper cuts or intricate designs. It's important to recognize that some stones are more fragile than they appear. For instance, while quartz may seem sturdy, its internal structures can make it prone to splitting if not handled correctly. Here are some strategies to reduce the risk of breakage:
- Choose the Right Bit: Always match the cutting bit to the specific stone type. For softer stones, using a more aggressive bit can create fractures. A finer bit allows for more control.
- Slow and Steady Wins the Race: Maintain a steady hand and apply gentle pressure. Rushing can cause unexpected chips, disrupting your work.
- Monitor the Temperature: Excessive heat can lead to thermal shock. Consider using a little water during cutting to keep things cool. This simple tip can often prevent a major headache.
"The key to cutting stone is patience; a few moments of caution can save a piece that might otherwise break."
These practices not only safeguard your stones but also enhance the quality of your work, providing you with pieces that are aesthetically pleasing and intact.
Addressing Power Issues
Power issues can derail even the best-planned projects. Whether you're in the middle of a groove or on the verge of completing a custom piece, nothing is more frustrating than a tool that gives out. This can happen due to several reasons:
- Battery Health: If you're using a cordless Dremel stone cutter, ensure your battery is in good health. Over time, batteries will experience degradation. Regularly check for performance, and consider investing in a replacement if necessary.
- Power Supply Stability: For corded tools, the connection to an outlet must be secure. A loose connection can cause intermittent power, leading to inconsistent cuts. Ensuring a snug fit with minimal extension cable use can help maintain a consistent power supply.
- Regular Maintenance: Dust and debris can clog vents and impact performance, especially during prolonged use. Take time to clean your cutter after sessions to keep it in top shape.
Addressing these power-related concerns can save not just time but also frustration, allowing enthusiasts to focus on their craft rather than rectify issues.
Overall, understanding how to tackle breakage and power issues leads to a smoother operation and greater satisfaction from your stone cutting projects. Collectors and hobbyists should view these challenges as opportunities for learning and improvement rather than as setbacks.
The Future of Stone Cutting Technology
The evolution of tools designed for stone cutting marks not just progress in functionality but also shows how critical these advancements are for collectors and hobbyists alike. The Dremel stone cutter is at the forefront of innovation, serving both seasoned professionals and aspiring enthusiasts. The importance of focusing on future technologies in stone cutting comes from its potential to enhance precision, efficiency, and creativity in various projects.
When considering the importance of advancements, one must first appreciate the benefits they bring. Future technologies could streamline the cutting process, offering faster turnaround without sacrificing quality. Imagine tools that integrate artificial intelligence to guide users through complex cuts or enhance the control over the cutting process with improved feedback mechanisms. Such developments hold promise not only for enhancing the quality of work but also for increasing the accessibility of stone cutting to everyone, regardless of skill level.
Emerging Innovations
In the realm of stone cutting, emerging innovations are being developed continuously, with several trends setting themselves apart. One notable example is the integration of smart technology into stone cutting tools. These tools could utilize sensors to adjust speed and pressure automatically based on the density of the material being cut. Moreover, the incorporation of augmented reality could provide real-time visual guides during the crafting process, allowing users to visualize the final product before making a single cut.
Another innovation gaining traction is the use of eco-friendly materials and practices. With growing concerns regarding environmental sustainability, manufacturers are finding ways to create more energy-efficient tools or those that use materials which are more easily recyclable. This shift isn't merely a trend but reflects a broader understanding of the responsibility that comes with crafting and collecting.
As the landscape of technology broadens, we should also keep an eye on software developments that accompany these tools. Programs that assist in the design phase, offering detailed simulations of projects, can galvanize creativity and enhance planning accuracy.
Trends in Collecting and Crafting
Trends in collecting and crafting are equally significant. Today's collectors are not just passive observers; they are increasingly becoming active participants who seek unique and personalized experiences. Customization options are on the rise—hobbyists can now find tools that allow for personal modifications, thereby increasing their attachment to projects and collected items.
Moreover, there’s a notable rise in trends focusing on community engagement. Social media platforms and forums like reddit.com enable collectors to connect, share tips, and showcase their work. Participation in workshops, whether in-person or online, fosters a sense of belonging and collective learning. More people are realizing that collaborating with others, exchanging ideas, and learning from diverse perspectives can elevate their craft and collecting experience exponentially.