Choosing the Right Drill for Rock Projects
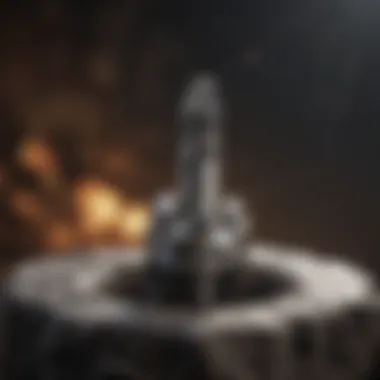
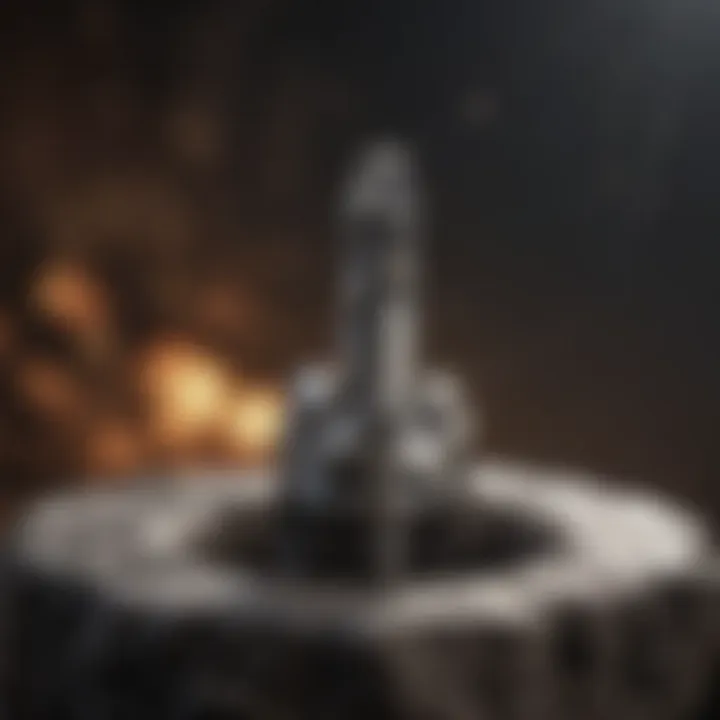
Intro
When it comes to drilling into rock, there's much more at stake than simply renting any ol' drill and hoping for the best. The choice of equipment can significantly impact both the efficiency of your work and the overall outcome of the project. This guide is here to unravel the intricacies of selecting the most suitable drill for your specific needs, covering all bases from understanding rock types to the nitty-gritty of drill specifications.
Every bit of knowledge is crucialâafter all, the last thing you want is to find yourself knee-deep in problems due to a poor choice of tools. Whether youâre an enthusiast looking to embark on your first project or a seasoned pro with a string of successful drilling endeavors under your belt, understanding what makes a drill effective in rock conditions will guide you in making a sound investment and ensure the quality of your work.
Make no mistake, every drill has distinct characteristics that lend themselves best to certain rock types. From hard granite to soft sandstone, each rock presents its own challenges and dictates a careful consideration of the drilling equipment you choose. Throughout this article, you will gain insights into the essential features to look for, how different drills perform under various geological circumstances, and the factors that can enhance your drilling adventures.
With the right information at your disposal, you will not only choose a drill but will also have a firmer grasp of why that choice resonates with the demands of your project. Now, let's dive into the heart of the matter.
Intro to Rock Drilling
A drill is more than just a tool; itâs a vital partner in the journey of rock exploration and collection. The significance of rock drilling can hardly be oversold. Understanding the nuances in drilling can mean the difference between a successful expedition and a frustrating endeavor. For serious rock and fossil collectors, having the right drill is paramount. The process isnât simply about piercing a surface; it involves careful consideration of rock types, project goals, and tool capabilities.
Importance of Choosing the Right Drill
Selecting the correct drill goes beyond mere preference; itâs an essential determinant of your projectâs success. The consequences of a wrong choice can be severe. Not only may you end up wasting time and resources, but you can also risk damage to the rock or fossil itself. For example, a rotary hammer drill might work like a charm on soft sedimentary rocks, but it could shatter delicate igneous specimens, leaving you with a pile of rubble instead of the treasure you sought. Therefore, considering the characteristics of your target rock and the specific requirements of your task becomes critical.
A solid grasp of available options helps in making decisions that align with both functionality and safety. When you select a drill that matches the rock type youâre targeting, youâre essentially stacking the cards in your favor. Furthermore, the right choice can drastically enhance your efficiency on-site, allowing you to extract samples quicker and with less effort.
Project Considerations
Before you even set your sights on a drill, it's essential to outline the objectives of your project. The intricacies of each drilling task can vary greatly. Ask yourself questions like:
- What depth do I need to reach?
- Am I looking at soft rock or something more robust?
- Do I require a drill that can operate in a tight space?
Each project will have its specific needs. For instance, if you're venturing into a remote location for fieldwork, portability can be a significant factor. Try to visualize the overall atmosphere: a bulky drill might do you no favors if you're trekking rocky terrain.
Then thereâs the aspect of budget and project timelines. Picking a high-end rotary hammer might seem tempting, but if it can't fit into your budget or time frame, it wonât serve you well in the long run. Ultimately, clear project goals are the compass that guides you in choosing the best equipment, steering clear of pitfalls and facilitating a more fruitful rock drilling experience.
"The right tool for the right job saves time, energy, and potential heartache."
When you prioritize both the drill choice and project specifications, you not only elevate the quality of your findings, but you also pave the way for a more seamless and enjoyable experience in your rock and fossil collecting journey.
Types of Rock Drills
When it comes to tackling rock drilling projects, the choice of drill type is paramount. The right drill can save time, money, and can even affect the overall success of the undertaking. Letâs plunge into the three primary types of rock drills: rotary hammer drills, percussion drills, and diamond core drills. Each has its own distinct features, benefits, and ideal applications, making them suitable for various rock formations and project needs.
Rotary Hammer Drills
Rotary hammer drills are widely recognized for their ability to drill into concrete and masonry with ease. Utilizing a combination of rotary and pounding action, these drills are particularly effective on tougher rock materials. A notable advantage is their power; they can penetrate hard surfaces without excessive effort from the operator, making them ideal for both amateur hobbyists and professionals alike.
Key characteristics of rotary hammer drills include:
- High impact energy, allowing for efficient drilling through dense materials.
- Versatility in drill bit options, including chiseling and standard drilling.
- Ideal for projects requiring vertical drilling, such as creating holes for rebar in construction.
One common consideration is noise. Rotary hammer drills can be quite loud, which could lead to strained communications on job sites. Thus, hearing protection is a must. Moreover, selecting an appropriate drill bit is crucial; using the right one ensures optimal performance and prevents damaging both the drill and the workpiece.
Percussion Drills
Percussion drills deliver a sharp, rapid pounding action and are often employed when drilling into softer rock types or when precise hole placement is necessary. Instead of relying solely on rotary motion, these drills rely on a hammering action that breaks up rock as it advances.
The benefits of percussion drills include:
- Enhanced control, allowing for precise drilling in fragile materials.
- Simplicity in operation, often requiring less advanced skills than other drilling types.
- Lightweight designs that make them easier to handle during extended use.
However, they might not be as effective on harder rocks, where specialized tools like rotary hammer drills would make a better fit. Users should also be aware of their limitations regarding drill depth and the need for frequent bit changes, especially in mixed materials where drill wear could be more severe.
Diamond Core Drills
Diamond core drills represent the cutting-edge of rock drilling technology. Thanks to their diamond-tipped drill bits, these tools can slice through even the hardest materials, including granite. This makes them a go-to solution for geological surveys or architectural applications requiring precise core samples.
Some of the standout features of diamond core drills include:
- Exceptional durability; diamond bits can last much longer than conventional bits.
- Ability to produce clean, precise holes with minimal debris.
- Versatility in use across various rock types, from igneous to sedimentary.
Despite their capabilities, diamond core drills come with a higher price tag and may require more initial investment. Also, operating these means handling more complex machinery, thus demanding a higher skill level from the operator. Additionally, they require a water supply for cooling, which can complicate some job setups.
Understanding Rock Types and Their Implications
When it comes to selecting the right drill, understanding the types of rock youâre dealing with is key. Each rock type presents its own unique challenges and requirements. Picking the right tool for the job hinges on this fundamental knowledge. Ignoring rock properties can lead to ineffective drilling, damage to equipment, or project delays.
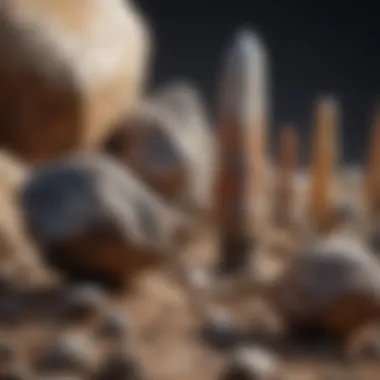
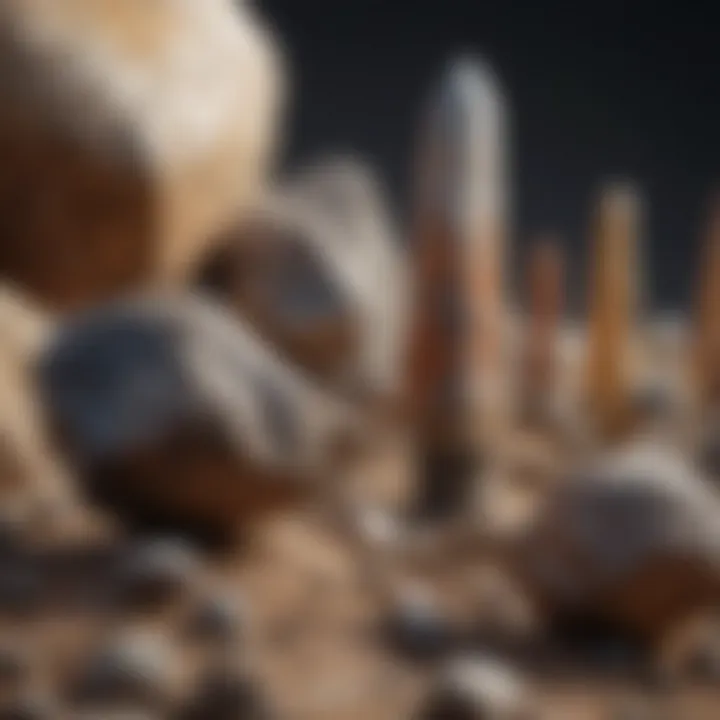
This section will guide you through the three primary types of rocks: sedimentary, igneous, and metamorphic. Weâll dive into what makes each of these rock categories distinct and how those characteristics influence your choice of drill.
Sedimentary Rocks
Sedimentary rocks tell a story of their own. These rocks form from the accumulation of particles, often in layers, over time. Common types include limestone and sandstone. Because they are typically softer than other rock types, they require less powerful drill bits.
Drilling through sedimentary rock may seem straightforward, but there are nuances to keep in mind. The porous nature can sometimes lead to excessive dust, necessitating a drill equipped with a dust extraction attachment. Hereâs what you should consider:
- Bit Type: Spiral or masonry bits are often effective here.
- Speed: A higher RPM helps in efficient drilling.
- Cooling Systems: Adequate cooling can prevent overheating, especially in layered structures.
These characteristics play a significant role in ensuring successful and efficient drilling.
Igneous Rocks
Igneous rocks, formed from cooled magma or lava, are more challenging. Granite and basalt are common examples. Their hardness and density require robust equipment, as these rocks demand higher torque and specialized drill bits.
Drilling in igneous materials might push a drill to its limits, but understanding the nuances can make the difference:
- Bit Material: Tungsten carbide bits are often the best choice due to their durability.
- Drilling Techniques: Employing a percussion method can be beneficial to break through tough surfaces.
- Speed Settings: Moderate speeds can help maintain control while maximizing efficiency.
Attention to these details can save time, energy, and resources.
Metamorphic Rocks
Metamorphic rocks, such as marble and slate, are perhaps the trickiest of the three categories. Formed under extreme temperature and pressure, these rocks often have varying properties even within a single specimen.
Choosing the right drill for metamorphic rock can feel like walking a tightrope:
- Tool Selection: Diamond-drill bits or diamond-core drills are essential for their extreme hardness and sharpness.
- Cooling Requirements: High-performance cooling systems help to avoid drill bit degradation.
- Drilling Technique: Slow speeds paired with consistent pressure yield the best results without damaging both the rock and the drill.
Gaining a deeper understanding of these rock types not only equips you with insight into choosing the right drill but also highlights the importance of employing the right techniques for each.
"Choosing the right drill isnât just about speed; itâs about matching your tool to the task at hand, ensuring both efficiency and effectiveness."
By honing in on the specific characteristics of sedimentary, igneous, and metamorphic rocks, you become better prepared to tackle any drilling project, reducing the margin for error and enhancing overall productivity.
Key Specifications to Consider
When it comes to drilling into rock, not all tools are created equal. Selecting the appropriate drill isnât just a matter of picking the first one you see; it involves understanding the key specifications that can make or break your project. The right specifications cater not only to the type of rock youâre drilling into but also to the goals you aim to achieve. So, letâs explore the key specifications you must take into account.
Power Source
The power source effectively dictates the performance of a rock drill. There are three primary options: electric, gas-powered, and pneumatic. Each has its strengths and weaknesses that can heavily influence your decision.
Electric Drills
Electric drills are often favored for their convenience and efficiency. Their lightweight and manageable design lends itself well to smaller projects or residential tasks. One significant characteristic of electric drills is their quiet operation, making them suitable for urban areas or places where noise is a concern. This aspect often makes electric drills a popular choice among those who may have noise restrictions or vanity concerns regarding their neighbors.
However, it's essential to consider the limited mobility compared to gas-powered alternatives. Since they often require an outlet or a generator, this can restrict your operational range, especially in remote environments where power sources are scarce.
Gas-Powered Drills
Gas-powered drills pack a punch when it comes to raw power. One prominent feature is their independence from electricity, allowing for a higher level of mobility. This characteristic is especially appealing for large-scale drilling operations in expansive landscapes or rugged terrains where electricity is a luxury. They are also known for their robust performance, cutting through dense rock efficiently.
However, gas-powered drills come with their own set of disadvantages. They typically require more maintenance and may produce more emissions, which could be a dealbreaker for environmentally conscious users. If youâre planning long hours of drilling in one go, the noise emitted can also be a significant factor, potentially irritating not just the user but also nearby individuals.
Pneumatic Drills
Pneumatic drills utilize air pressure to function, which gives them a unique edge in terms of consistency and speed. They are particularly effective for heavy-duty applications and can maintain performance without overheating, a common issue found in electric or gas-powered drills. Their performance is usually unmatched when drilling through harder rock types, making them a strong choice for professional applications.
On the flip side, pneumatic drills require a compressor. This could limit your mobility and adds an extra component to ensure your project runs smoothly. Also, they tend to be a bit heavier, making them less approachable for casual users.
Chuck Size and Type
The chuck size and type play a pivotal role in ensuring that you can use the correct bits for various tasks. The right chuck size allows for a more secure fit, providing better stability during drilling. Different drilling scenarios may necessitate the usage of varied chuck types â from keyed to keyless options. Keyless chucks offer quick adjustments and convenience, while keyed chucks often deliver added security but require more time for changing bits. Proper chuck selection can enhance your drilling experience and lead to more precise results.
Impact Mechanisms
The impact mechanism can influence drilling efficiency, particularly in harder rock types. Tools equipped with a dual-mode mechanism, which allows for both rotary motion and impact, often provide versatility. This feature is crucial when tackling diverse projects that demand adaptability. Understanding the impact mechanism helps you gauge whether the drill can handle mixed drilling tasks without compromising on performance.
In summary, understanding the power source, chuck size and type, and impact mechanisms will guide you toward making the most informed decision when selecting a rock drill.
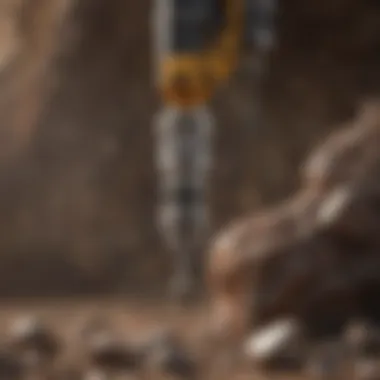
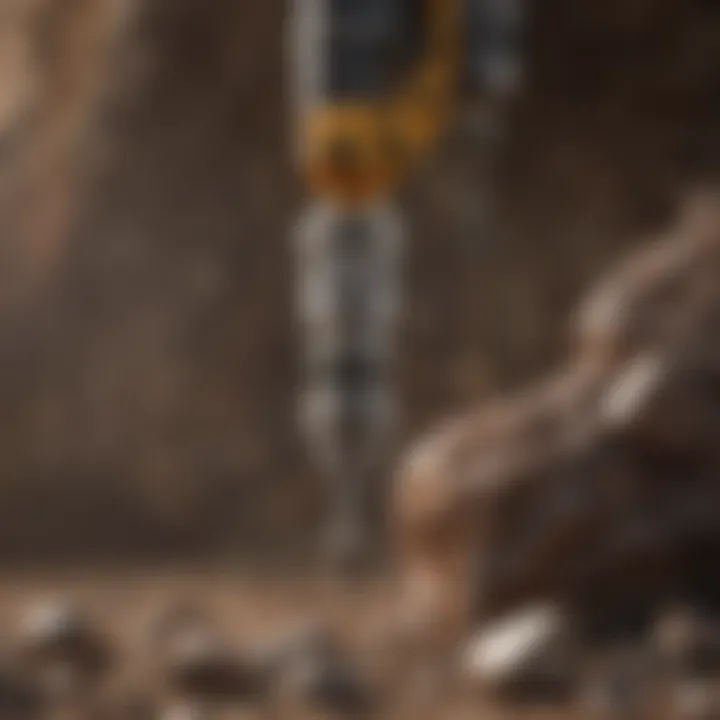
By focusing on these specifications, you align your drill choice with both your project requirements and your preferences. Prioritize carefully and the project will likely move ahead as smooth as butter.
Performance Metrics of Rock Drills
When it comes to rock drilling, understanding the performance metrics is crucial. These metrics not only dictate how effective a drill will be in various situations but also impacts the overall success of your project. Knowing the nuances of these performance indicators can save time and resources while ensuring the chosen equipment meets the specific demands of your drilling application.
Drill Speed and Torque
Drill speed refers to how fast the drill bit rotates while in operation. Measured in revolutions per minute (RPM), this metric plays a pivotal role in determining how quickly you can penetrate rock surfaces. Higher speeds are often required for softer rock, while slower speeds are necessary for denser, harder materials. The key is to strike a balance - too fast might lead to overheating or damage, while too slow can hinder progress.
Torque, on the other hand, is the rotational force that allows a drill to cut into solid materials. Itâs essential for effective drilling, especially in harder rock types. Insufficient torque could lead to a drill stalling, which is frustrating and time-consuming.
When evaluating drill speed and torque, consider the following:
- The type of rock youâll be drilling through: different rock types require different speeds and torque levels.
- The nature of your project: larger projects may necessitate drills with higher torque for consistency.
- Your own experience level: higher torque may require more skill to handle effectively.
"Selecting a drill with the right balance of speed and torque can mean the difference between an efficient job and a frustrating ordeal."
Durability and Longevity
Durability and longevity are paramount when selecting a rock drill. You want a tool that can withstand the rigors of demanding environments. A durable drill not only survives the harsh conditions often encountered in rock drilling, but it also minimizes the need for frequent replacements or repairs, thus saving you money in the long run.
Factors contributing to a drillâs durability include:
- Material Composition: Drills made from high-quality materials such as hardened steel or tungsten carbide tend to last longer.
- Build Quality: Well-constructed drills are designed to handle vibrations and impacts without losing effectiveness.
- Regular Maintenance: Just like any tool, regular upkeep can significantly extend a drillâs lifespan. Ensure youâre familiar with the manufacturerâs maintenance recommendations.
When pondering durability, think about the following:
- The conditions under which the drill will be used: extreme weather or highly abrasive materials can shorten a drillâs life.
- The available support and warranty offered by manufacturers: a solid warranty can indicate confidence in the productâs durability.
In summary, considering performance metrics like drill speed, torque, durability, and longevity is essential to making an informed choice. With these metrics in mind, you can select a rock drill that will not only perform well but also endure the test of time, making your investment worthwhile.
Feature Enhancements
When selecting a drill for rock, the conversation often leaps straight to power and torque, leaving subtle yet crucial features in the background. Instead of overlooking these enhancements, itâs essential to understand how they can boost overall efficiency and user experience. Features such as anti-vibration systems and dust extraction capabilities donât just add flair; they serve to make the work smoother and more efficient.
Every little detail matters when youâre tackling tough rock faces. These enhancements can enhance performance, safeguard your equipment, and ensure a better working environment. Letâs delve into two key features that significantly impact how effectively and safely you can operate a rock drill.
Anti-Vibration Systems
Anti-vibration systems are more than a luxury; they are a necessity for anyone aiming for precision in rock drilling. These systems use technology to mitigate the physical impact of vibrations on the drill handle and user. By absorbing excessive vibrations, they reduce strain on the operator's hands and arms, which can lead to fatigue or even long-term issues if youâre not careful.
- Benefits:
- Comfort: A drill with advanced anti-vibration features allows you to work longer without discomfort. This is vital when your project requires multiple hours of continuous drilling.
- Accuracy: By minimizing vibrations, these systems help you maintain better control of your drill, resulting in cleaner and more accurate holes. This is crucial, especially in geological drilling where precision matters.
- Longevity: Less vibration also means reduced wear and tear on your drill. Your equipment stays in good shape longer, which translates to fewer repairs.
Incorporating drills with robust anti-vibration systems can transform a grueling task into a more manageable one, allowing you to focus on your project rather than on discomfort.
Dust Extraction Capabilities
Dust control is another integral consideration when drilling rock. The act of drilling doesnât just break through a solid surface; it sends particles flying â and that dust can be a nuisance or a significant hazard. Drills equipped with dust extraction systems can significantly reduce airborne, harmful particles, enhancing both safety and visibility.
- Benefits:
- Health: Breathing in rock dust can cause respiratory issues over time. Dust extraction helps protect your health, making each drilling project safer.
- Visibility: Dust clouds obscure your view, potentially leading to mistakes. By keeping the work area clear, you can see more clearly what youâre doing, increasing accuracy and safety.
- Efficiency: Extracting debris reduces the need for cleanup after a drilling session. You can move on to the next task without wasting time clearing away dust.
In todayâs world, where safety regulations are increasingly stringent, having dust extraction capabilities isnât just a nice-to-have â itâs becoming the norm.
The inclusion of features like anti-vibration systems and dust extraction capabilities isnât merely about adding bells and whistles; it's about ensuring you can drill effectively, efficiently, and safely over the long haul.
By paying attention to these enhancements, youâll not only make better use of your tools but also create a more pleasant and effective work environment as you tackle various drilling challenges.
Brand Comparisons
Choosing a drill for rock isn't just about picking whateverâs on sale at the local hardware store. Many brands have carved out their niche in the market, each boasting unique features and capabilities. Understanding these differences is crucial to making an informed choice that suits your specific drilling needs.
Many users often overlook the significance of brand reputation when selecting tools. A reputable brand often means quality assurance, reliability, and robust customer support. On the other hand, lesser-known brands may provide cheaper products but often lack the reliability and service that established brands offer.
Top Manufacturers and Their Offerings
Some manufacturers have set the bar high when it comes to rock drills. Companies like DeWalt, Bosch, and Makita are often at the forefront. They consistently provide models that blend power and durability, tailored for different types of rock and user requirements.
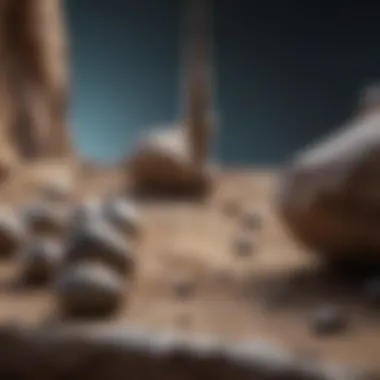
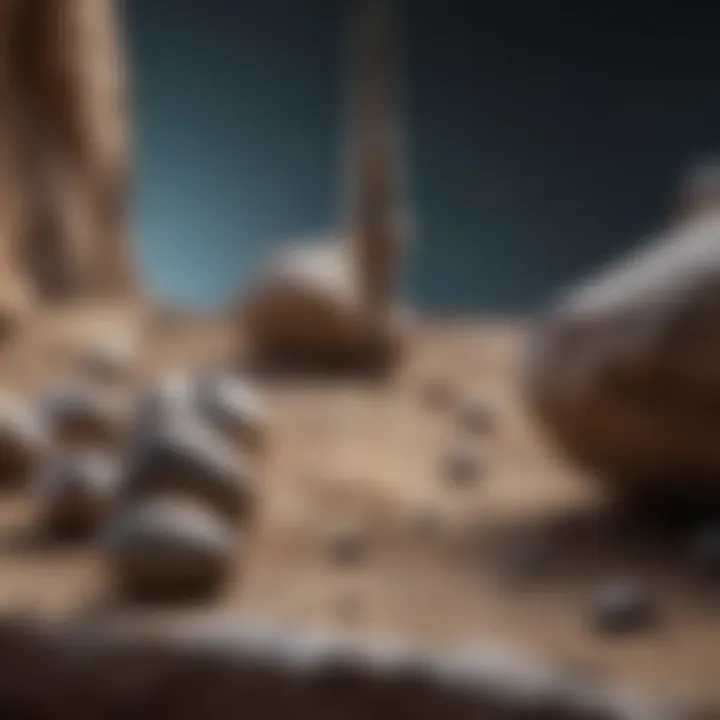
- DeWalt: Known for their robust construction drills, DeWalt usually delivers great torque and longevity. Their hammer drills incorporate advanced technology for improved efficiency.
- Bosch: Craftsmanship is Bosch's strong suit; their products often feature ergonomic designs and powerful motors. They offer various models, from compact to heavy-duty options.
- Makita: This brand is recognized for its versatility and affordability. Makita drills often come packed with features that cater to both the novice and experienced user.
Each of these brands has a range of offerings tailored for diverse drilling demands. It's worth spending some time browsing their catalogs to identify what matches your needs.
Quality versus Price Analysis
When considering rock drills, the balance between quality and price serves as a pivotal factor. Some users may find themselves tempted by lower-priced options, but there are hidden costs associated with cheaper tools. For instance, lower-priced models often use inferior materials, leading to reduced longevity and efficacy.
A premium drill, while it may demand a higher upfront investment, can save money in the long run. High-quality tools typically provide:
- Longer Lifespan: A well-made drill not only lasts longer but often works better, translating to fewer repairs or replacements.
- Enhanced Performance: A high-quality drill can withstand more demanding projects, making it suitable for varied rock types.
- Better Support Services: Established brands generally offer more reliable customer service, warranties, and replacement parts, which can be invaluable down the line.
Ultimately, itâs essential to weigh the benefits of investing in a reputable brand against opting for a more economical choice. Sometimes, the lower initial outlay can lead to a cycle of purchasing replacements, which could turn out costlier in the long run.
Think of it this way: paying a little more today could save you a headache tomorrow.
In the world of rock drilling, detailed brand comparisons and a thorough understanding of what each manufacturer stands for can make a significant difference in the success of your project!
User Reviews and Experiences
When it comes to selecting the right drill for rock excavation or collection, diving into the opinions and experiences of actual users can be invaluable. Reviews offer a lens into real-world applications and outcomes that specs and marketing campaigns can't always reveal. In a field as varied as rock drilling, every detail matters; user feedback steers potential buyers towards informed decisions, enhancing overall satisfaction with their purchases.
Customer Feedback Analysis
Customer reviews serve as a treasure trove of insights about performance, usability, and reliability. Users often share stories about how their drills handled specific rock types or difficult conditions. The more firsthand experiences one can access, the clearer the picture becomes. For example, a rotary hammer drill favored for its power might receive mixed reviews regarding its weight and ease of handling. Users frequently underscore the balance between might and manageability, shedding light on how even top-tier brands can have their quirks.
- Power Ratings: Many reviewers mention how the product holds up over time, discussing issues like overheating during extensive drilling. Performance metrics matter greatly here, as they reveal which models can take a beating versus those that might flounder under pressure.
- Ease of Use: Newbies often share their experiences with drills that offer a steep learning curve while seasoned users may favor models that provide more control.
- Customer Service: A drill is just a tool, but poor support can often sour the experience. Customers frequently comment on the responsiveness and helpfulness of a manufacturer's service team, which can make or break a decision.
Relying on this kind of collective knowledge can save both time and money; after all, no one likes to be a guinea pig when it comes to investment in equipment.
Common Challenges and Solutions
Of course, every tool has its limitations, and drills are no exception. Common challenges arise frequently in user feedback, born out of shared experiences. Users have particular tales about overcoming obstacles, and this community often provides solutions found through trial and error.
- Drilling through Hard Rock: Some users struggle with dense materials that push their equipment to the limit. They might recommend specific drill bits designed for tougher terrains, like tungsten carbide or diamond-encrusted bits, known for their durability.
- Vibration Issues: Equipment can shake quite a bit, and avid drillers often report on the vibrations that can wear down both tool and user. Many point toward anti-vibration handles or systemsâfeatures that seem to separate the wheat from the chaff in product offerings.
- Maintenance Gaps: Another challenge that rears its head in reviews is inconsistent maintenance. Affected users often highlight their experiences with regular upkeepâgreasing parts, cleaning vents, adjusting settingsâwhich greatly prolongs a drill's lifespan.
In the end, previous users present invaluable knowledge that can dramatically influence purchasing decisions. By analyzing feedback and recommendations, potential buyers unveil not just what works, but what's best suited for their individual needs.
Practical Tips for Using Rock Drills
Using rock drills is not just about choosing the right tool but also about knowing how to use it safely and effectively. Practical tips for using rock drills can enhance not only the efficiency of your projects but also ensure your safety throughout the drilling process. Knowing these tips can mitigate common issues that arise, thus making your drilling endeavors more fruitful and less problematic.
Safety Precautions
When operating rock drills, safety should be your top priority. Here are some essential safety precautions:
- Wear Protective Gear: Always put on safety goggles, hard hats, and ear protection. Rocks can shatter or produce dust that can be harmful if inhaled.
- Check Equipment Before Use: Regularly inspect your drills and drilling accessories. Ensure there are no loose parts, as this can lead to malfunction or accidents.
- Stabilize Your Position: Keep a stable stance while drilling. Your footing should be secure. If working on a sloped surface, be extra cautious.
- Keep Work Area Clear: Maintain a clean and organized workspace. Debris or obstacles can lead to accidents during drilling.
âSafety first is safety always.â This adage rings true in any operation involving equipment, especially something as powerful as a rock drill.
You should also be aware of environmental factors, such as weather conditions. Drilling in wet or icy locales may call for more cautious movements and extra gear to avoid slipping or machine malfunction.
Operational Techniques
Using a rock drill efficiently means employing the right techniques. Understanding these can make all the difference:
- Start With the Right Angle: The angle at which you drill can affect both speed and effectiveness. In most cases, a 90-degree angle to the rock surface provides optimal performance.
- Maintain Steady Pressure: Applying constant pressure helps to maintain drill performance. Avoid excessive pressure, as this can slow down the drill and cause wear.
- Use the Correct Speed Settings: Different rock types require varying speeds. Harder rocks benefit from slower speeds, while softer ones might need a quicker pace.
- Employ Water or Dust Suppression: Using water during drilling can help cool the bit and minimize dust. Dust suppression not only aids visibility but also helps maintain a cleaner working environment.
- Regularly Check Drill Bits: Inspect drill bits for wear during breaks. Replacing or sharpening them when needed improves efficiency and prolongs the life of your tool.
Every operator can benefit from knowing these operational techniques. They optimize performance while prolonging the life of the equipment. Good practices, when combined with the right tools, can inevitably lead to a productive and safe working experience.
The End
Choosing the right drill for rock is not just a matter of picking a tool off the shelf. Itâs an intricate dance between understanding the specific demands of your project and the capabilities of various drill technologies. As weâve seen throughout the article, this choice can significantly affect both the quality of work and the efficiency of your efforts.
For anyone delving into rock drilling, itâs essential to recap the critical factors discussed. This includes knowing the types of rock youâre working with, as each presents its own challenges and requirements for drilling equipment. Moreover, the specifications such as power source, chuck size, and impact mechanisms directly influence how well a drill will perform in your context.
Recap of Key Points
- Types of Drills: Understand the major categoriesârotary hammer, percussion, and diamond core drillsâand their respective strengths.
- Rock Characteristics: Identify if youâre dealing with sedimentary, igneous, or metamorphic rock, as this can steer your drill selection.
- Specifications Matter: Consider the power source, chuck size, and type of impact mechanisms that fit your project needs.
- User Experiences: Learn from others by reviewing customer feedback on specific models, which can provide real-world insights.
- Safety and Technique: Apply the best practices in operational techniques and safety to ensure a successful and secure drilling experience.
"The tools we choose affect the outcome of our labor. A poor choice can change the trajectory of a project completely."
Final Thoughts on Choosing the Best Drill
In light of all these considerations, choosing the best drill must come down to a well-informed decision that factors in not just the immediate needs, but also future implications. Investing time in understanding both the tool and the material can mean the difference between a quick job well done and a laborious struggle that could have been avoided.
When in doubt, consult user reviews and donât hesitate to reach out to manufacturers or experienced users for guidance. Technology evolves, and so do rock drilling methods. Keeping abreast of the latest advancements, while adhering to tried-and-true practices, will empower you to tackle any rock drilling endeavor with confidence.
Ultimately, a successful drilling project hinges on informed decisions, quality tools, and a solid understanding of your specific requirements. Embrace the knowledge and let your drilling prowess reflect the careful consideration youâve invested in it.